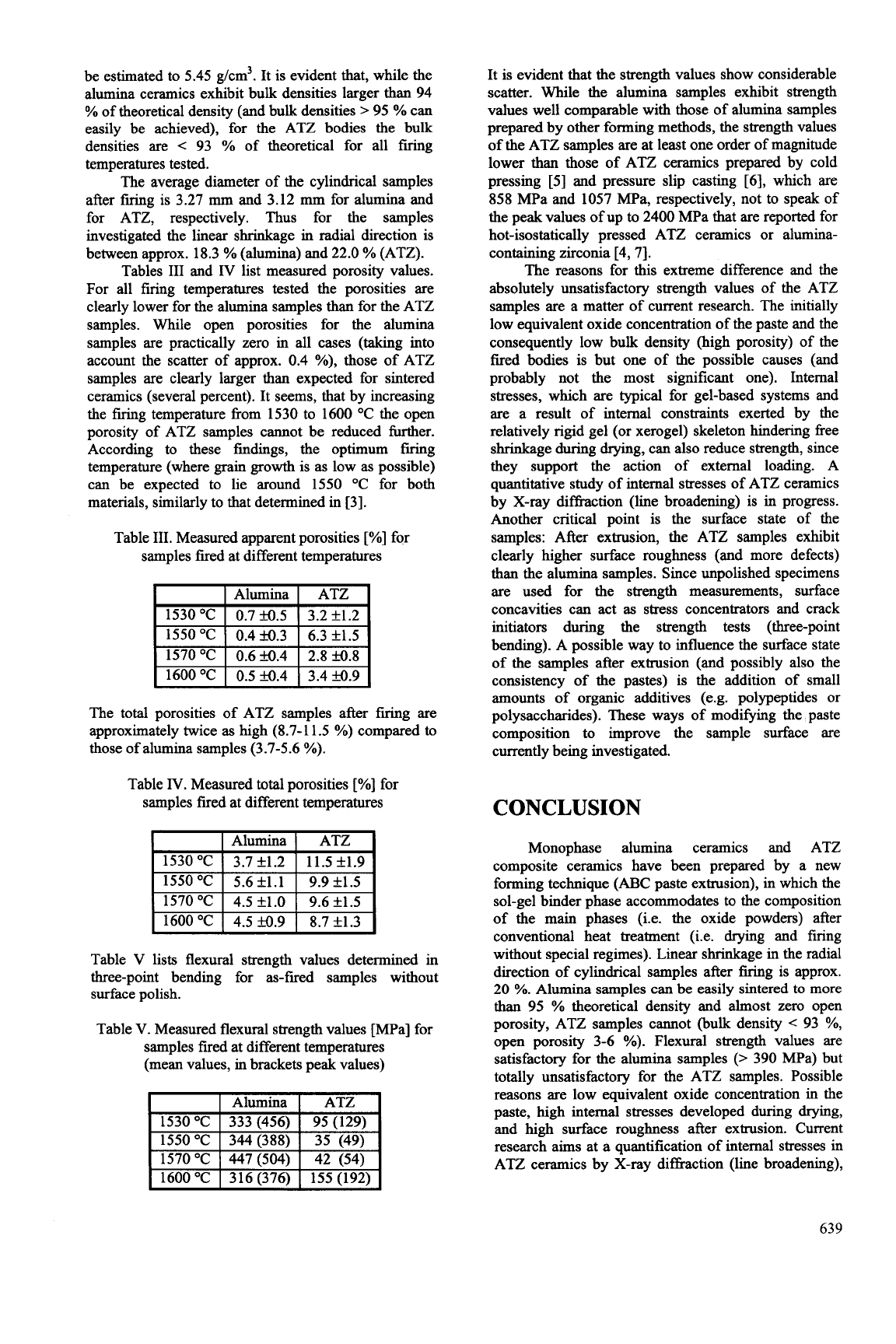
be estimated to 5.45 g/cm3. It is evident that, while the
alumina ceramics exhibit bulk densities larger than 94
%
of theoretical density (and bulk densities
>
95
%
can
easily be achieved), for the ATZ bodies the bulk
densities are
<
93
%
of theoretical for all firing
temperatures tested.
The average diameter of the cylindrical samples
after firing is 3.27 mm and 3.12
mm
for alumina and
for ATZ, respectively. Thus for the samples
investigated the linear shrinkage in radial direction is
between approx. 18.3
%
(alumina) and 22.0
%
(ATZ).
Tables
I11
and IV list measured porosity values.
For all firing temperatures tested the porosities are
clearly lower for the alumina samples than for the ATZ
samples. While open porosities for the alumina
samples are practically zero in all cases (taking into
account the scatter of approx. 0.4
YO),
those of ATZ
samples are clearly larger than expected for sintered
ceramics (several percent).
It
seems, that by increasing
the firing temperature from 1530 to 1600 OC the open
porosity of ATZ samples cannot be reduced further.
According to these findings, the optimum firing
temperature (where grain
growth
is
as
low
as
possible)
can be expected to lie around 1550 OC for both
materials, similarly
to
that determined in [3].
1570 OC
1600 OC
Table
111.
Measured apparent porosities
[%I
samples fired at different temperatures
0.6 M.4 2.8
B.8
0.5
M.4 3.4 M.9
for
The total porosities of ATZ samples after firing are
approximately twice
as
high (8.7-1 1.5
%)
compared
to
those of alumina samples (3.7-5.6
%).
Table IV. Measured total porosities
[YO]
for
samples fired at different temperatures
1
I
Alumina
I
ATZ
1
Table V lists flexural strength values determined in
three-point bending for as-fired samples without
surface polish.
Table V. Measured flexural strength values [MPa] for
samples fired at different temperatures
(mean values, in brackets peak values)
I
I
Alumina
I
ATZ
1
It is evident that the strength values show considerable
scatter. While the alumina samples exhibit strength
values well comparable with those of alumina samples
prepared by other forming methods, the strength values
of the ATZ samples are at least one order of magnitude
lower than those of ATZ ceramics prepared by cold
pressing [5] and pressure slip casting [6], which are
858
MPa and 1057 MPa, respectively, not to speak of
the peak values of up to 2400 MPa that are reported for
hot-isostatically pressed ATZ ceramics or alumina-
containing zirconia [4,7].
The reasons for this extreme difference and the
absolutely unsatisfactory strength values of the ATZ
samples are a matter of current research. The initially
low equivalent oxide concentration of the paste and the
consequently low bulk density (high porosity) of the
fired bodies is but one of the possible causes (and
probably not the most significant one). Internal
stresses, which are typical for gel-based systems and
are a result of internal constraints exerted by the
relatively rigid gel (or xerogel) skeleton hindering free
shrinkage during drying, can also reduce strength, since
they support the action of external loading. A
quantitative study of internal stresses of ATZ ceramics
by X-ray diffiction (line broadening) is in progress.
Another critical point is the surface state of the
samples: After extrusion, the ATZ samples exhibit
clearly higher surface roughness (and more defects)
than the alumina samples. Since unpolished specimens
are used for the strength measurements, surface
concavities can act
as
stress concentrators and crack
initiators during the strength tests (three-point
bending). A possible way to influence the surface state
of the samples after extrusion (and possibly also the
consistency of the pastes) is the addition of small
amounts of organic additives (e.g. polypeptides or
polysaccharides). These ways of modifying the paste
composition to improve the sample surface are
currently being investigated.
CONCLUSION
Monophase alumina ceramics and ATZ
composite ceramics have been prepared by a new
forming technique (ABC paste extrusion), in which the
sol-gel binder phase accommodates to the composition
of the main phases (i.e. the oxide powders) after
conventional heat treatment (i.e. drying and firing
without special regimes). Linear shrinkage in the radial
direction of cylindrical samples after firing is approx.
20
YO.
Alumina
samples
can
be
easily sintered
to
more
than 95
%
theoretical density and almost zero open
porosity, ATZ samples cannot (bulk density
<
93
%,
open porosity 3-6
%).
Flexural strength values are
satisfactory for the alumina samples
(>
390 MPa) but
totally unsatisfactory for the ATZ samples. Possible
reasons are low equivalent oxide concentration in the
paste,
high
internal stresses developed during drying,
and high surface roughness after extrusion. Current
research aims at a quantification of internal stresses in
ATZ ceramics by X-ray diffiction (line broadening),
639