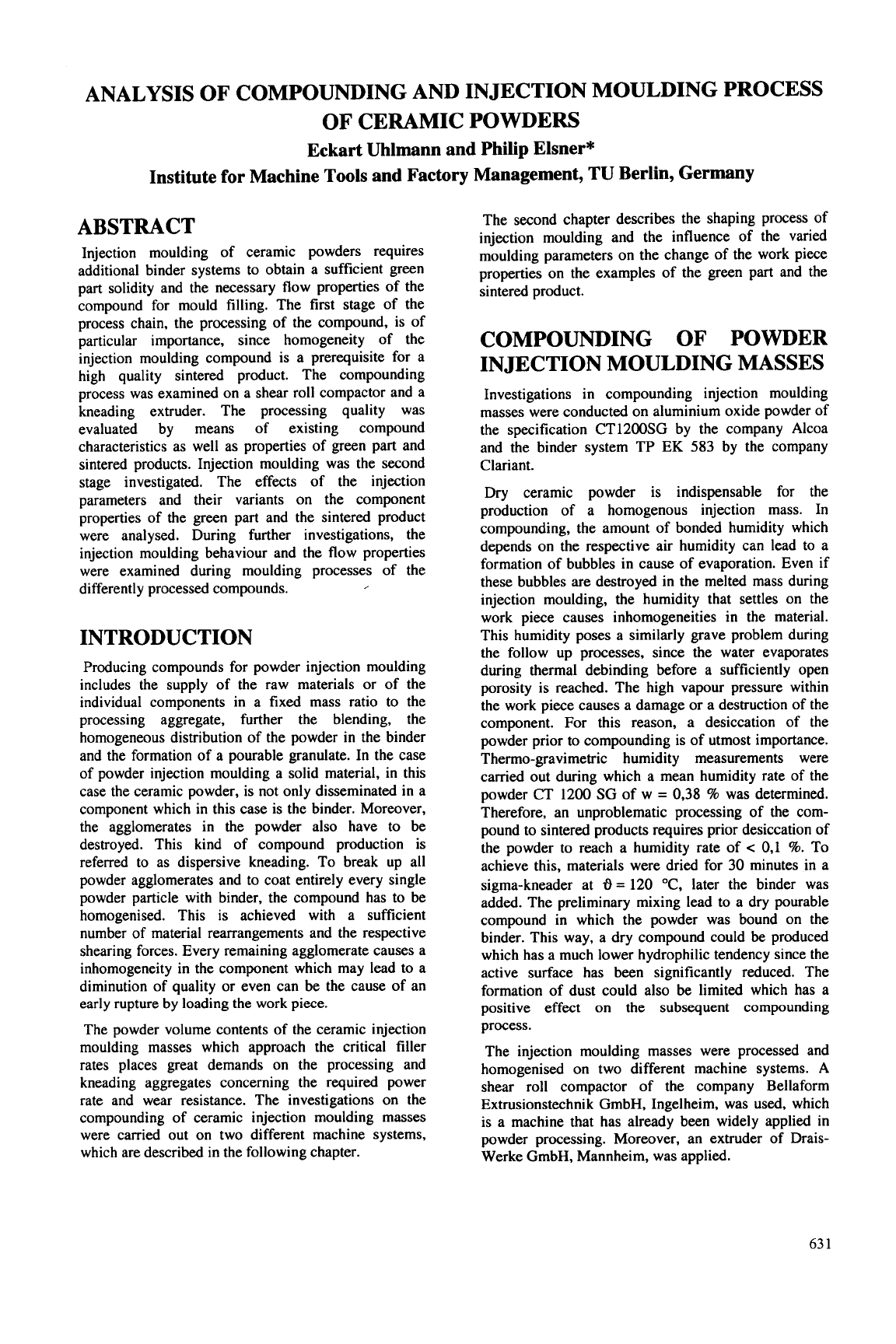
ANALYSIS
OF
COMPOUNDING AND INJECTION MOULDING PROCESS
OF
CERAMIC POWDERS
Eckart Uhlmann and Philip Elsner*
Institute for Machine Tools and Factory Management, TU Berlin, Germany
ABSTRACT
Injection moulding of ceramic powders requires
additional binder systems to obtain a sufficient green
part solidity and the necessary flow properties of the
compound for mould filling. The first stage of the
process chain, the processing of the compound, is of
particular importance, since homogeneity of the
injection moulding compound is a prerequisite for a
high quality sintered product. The compounding
process was examined on a shear
roll
compactor and a
kneading extruder. The processing quality was
evaluated by means of existing compound
characteristics as well as properties of green part and
sintered products. Injection moulding was the second
stage investigated. The effects of the injection
parameters and their variants on the component
properties of the green part and the sintered product
were analysed. During further investigations, the
injection moulding behaviour and the flow properties
were examined during moulding processes of the
differently processed compounds.
INTRODUCTION
Producing compounds for powder injection moulding
includes
the
supply of the raw materials
or
of the
individual components in a
fixed
mass ratio to the
processing aggregate, further the blending, the
homogeneous distribution of the powder
in
the binder
and the formation of a pourable granulate. In the case
of powder injection moulding a solid material,
in
this
case the ceramic powder, is not only disseminated
in
a
component which
in
this case is the binder. Moreover,
the agglomerates
in
the powder also have to be
destroyed. This kind of compound production is
referred to as dispersive kneading. To break up all
powder agglomerates and to coat entirely every single
powder particle with binder, the compound has to be
homogenised. This is achieved with a sufficient
number of material rearrangements and the respective
shearing forces. Every remaining agglomerate causes a
inhomogeneity in the component which may lead to a
diminution of quality
or
even can be the cause of an
early rupture by loading the work piece.
The powder volume contents of the ceramic injection
moulding masses which approach the critical filler
rates places great demands on the processing and
kneading aggregates concerning the required power
rate and wear resistance. The investigations on
the
compounding
of
ceramic injection moulding masses
were carried out on two different machine systems,
which are described
in
the following chapter.
The second chapter describes the shaping process of
injection moulding and the influence of the varied
moulding parameters on the change
of
the work piece
properties on the examples of the green part and the
sintered product.
COMPOUNDING OF POWDER
INJECTION MOULDING MASSES
Investigations in compounding injection moulding
masses were conducted on aluminium oxide powder of
the specification CT1200SG by the company Alcoa
and the binder system TP EK
583
by the company
Clariant.
Dry ceramic powder is indispensable for the
production of a homogenous injection mass. In
compounding, the amount of bonded humidity which
depends on the respective air humidity can lead to a
formation of bubbles in cause of evaporation. Even
if
these bubbles are destroyed in the melted mass during
injection moulding, the humidity that settles on the
work piece causes inhomogeneities in
the
material.
This humidity poses a similarly grave problem during
the follow up processes, since the water evaporates
during thermal debinding before a sufficiently open
porosity is reached. The high vapour pressure within
the work piece causes a damage
or
a destruction of the
component.
For
this reason, a desiccation of the
powder prior to compounding is of utmost importance.
Thermo-gravimetric humidity measurements were
carried out during which a mean humidity rate of the
powder CT 1200 SG of w
=
0.38
%
was determined.
Therefore, an unproblematic processing of the com-
pound to sintered products requires prior desiccation of
the powder to reach a humidity rate of
<
0.1
%.
To
achieve this, materials were dried for
30
minutes in a
sigma-kneader at
6=
120 "C, later the binder was
added. The preliminary mixing lead to a dry pourable
compound in which the powder was bound on the
binder. This way, a dry compound could be produced
which has a much lower hydrophilic tendency since the
active surface has been significantly reduced. The
formation of dust could also be limited which has a
positive effect on
the
subsequent compounding
process.
The injection moulding masses were processed and
homogenised on two different machine systems.
A
shear roll compactor of the company Bellaform
Extrusionstechnik GmbH, Ingelheim, was used, which
is a machine that has already been widely applied in
powder processing. Moreover, an extruder of Drais-
Werke GmbH, Mannheim, was applied.
63
1