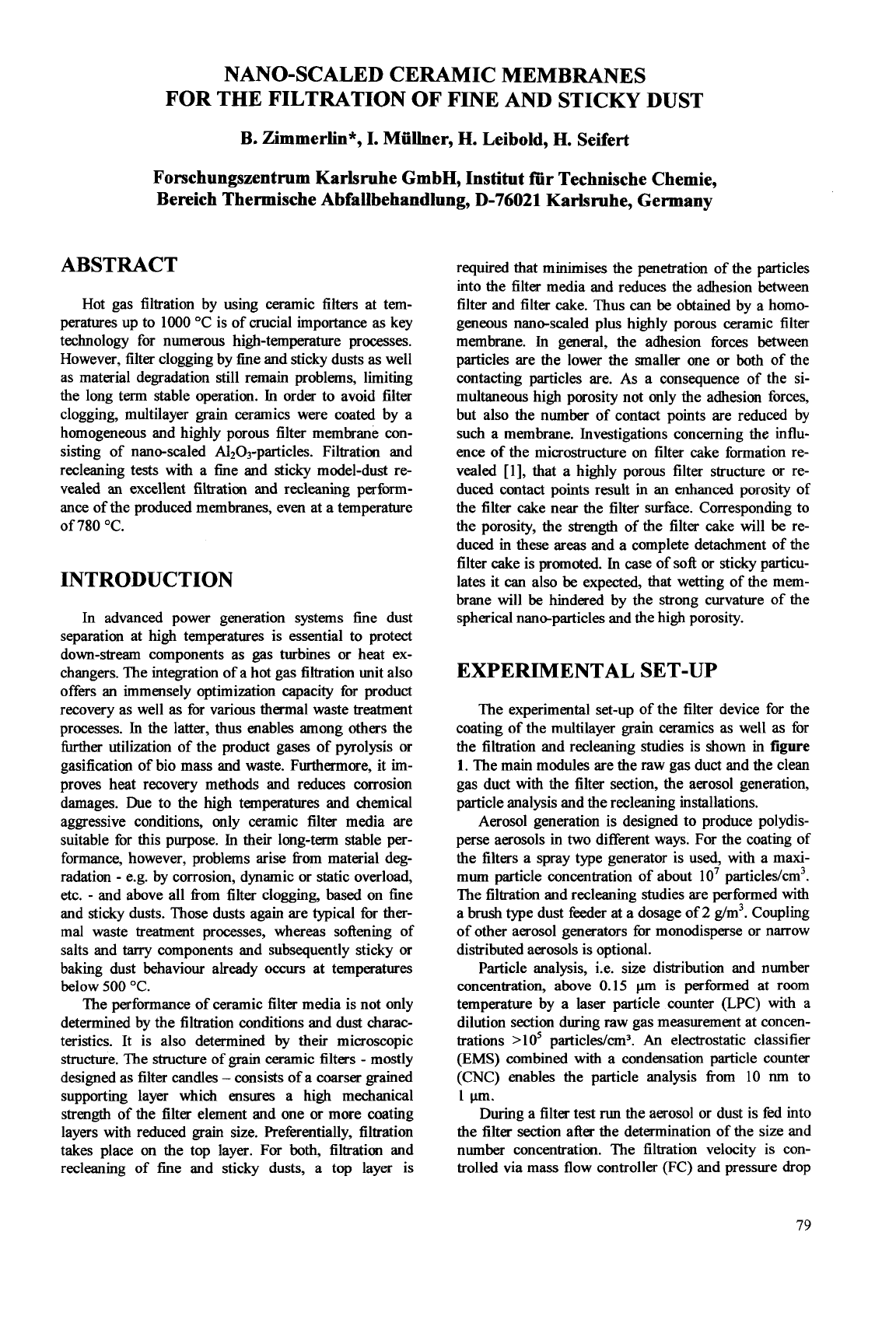
NANO-SCALED CERAMIC MEMBRANES
FOR THE FILTRATION OF FINE AND STICKY DUST
B. Zimmerlin*, I. Miillner,
H.
Leibold, H. Seifert
Forschungszentrum Karlsruhe GmbH, Institut fir Technische Chemie,
Bereich Thermische Abfallbehandlung,
D-76021
Karlsruhe, Germany
ABSTRACT
Hot gas filtration by using ceramic filters at tem-
peratures up to
1000
"C is of crucial importance as key
technology for numerous high-temperature processes.
However, filter clogging by he and sticky dusts
as
well
as material degradation still remain problems, limiting
the long term stable operation. In order to avoid filter
clogging, multilayer grain ceramics were coated by a
homogeneous and highly porous filter membrane con-
sisting of nano-scaled A1203-particles. Filtration and
recleaning tests with a fine and sticky model-dust re-
vealed an excellent filtration and recleaning perform-
ance
of
the produced membranes, even at a temperature
of
780
"C.
INTRODUCTION
In advanced power generation systems fine dust
separation at high temperatures is essential to protect
down-stream components as
gas
turbines or heat ex-
changers. The integration of a hot gas filtration unit also
offers an immensely optimization capacity for product
recovery as well as for various thermal waste treatment
processes. In the latter, thus enables among others the
fiuther utilization of the product gases
of
pyrolysis or
gasification of bio mass and waste. Furthermore, it
im-
proves heat recovery methods and reduces corrosion
damages. Due to the high temperatures and chemical
aggressive conditions, only ceramic filter media are
suitable for this purpose. In their long-term stable per-
formance, however, problems arise from material deg-
radation
-
e.g. by corrosion, dynamic or static overload,
etc.
-
and above all from filter clogging, based on fine
and sticky dusts. Those dusts again are typical for ther-
mal waste treatment processes, whereas softening of
salts and
tarry
components and subsequently sticky or
baking dust behaviour already occurs at temperatures
below
500
"C.
The performance of ceramic filter media is not only
determined by the filtration conditions and dust charac-
teristics. It is also determined by their microscopic
structure. The structure of grain ceramic filters
-
mostly
designed as filter candles
-
consists
of
a coarser grained
supporting layer which ensures a high mechanical
strength
of
the filter element and one or more coating
layers with reduced grain size. Preferentially, filtration
takes place on the top layer. For both, filtration and
recleaning of fine and sticky dusts, a top layer is
required that minimises the penetration of the particles
into the filter media and reduces the adhesion between
filter and filter cake. Thus
can
be obtained by a homo-
geneous nano-scaled plus highly porous ceramic filter
membrane. In general, the adhesion forces between
particles are the lower the smaller one or both of the
contacting particles are. As a consequence of the si-
multaneous high porosity not only the adhesion forces,
but also the number of contact points are reduced by
such a membrane. Investigations concerning the influ-
ence of the microstructure on filter cake formation re-
vealed
[l],
that a highly porous filter structure
or
re-
duced contact points result
in
an enhanced porosity
of
the filter cake near the filter surhce. Corresponding to
the porosity, the strength of the filter cake will
be
re-
duced in these areas and a complete detachment of the
filter cake is promoted. In case of
soft
or sticky particu-
lates it
can
also
be
expected, that wetting of the mem-
brane will be hindered by the strong curvature of the
spherical nano-particles and the high porosity.
EXPERIMENTAL SET-UP
The experimental set-up of the filter device for the
coating of the multilayer grain ceramics as well as for
the filtration and recleaning studies is shown in
figure
1.
The main modules are the raw gas duct and the clean
gas duct with the filter section, the aerosol generation,
particle analysis and the recleaning installations.
Aerosol generation is designed to produce polydis-
perse aerosols in two different ways. For the coating
of
the filters a spray type generator is used, with a maxi-
mum
particle concentration of about
lo7
particles/cm3.
The filtration and recleaning studies are performed with
a brush type dust feeder at a dosage of
2
g/m3. Coupling
of other aerosol generators for monodisperse or narrow
distributed aerosols is optional.
Particle analysis, i.e. size distribution and number
concentration,
above
0.15
pm
is
performed at room
temperature by a laser particle counter (LPC) with a
dilution section during raw gas measurement at concen-
trations
>
1
o5
particles/cm3.
AII
electrostatic classifier
(EMS)
combined with a condensation particle counter
(CNC) enables the particle analysis fiom
10
nm
to
1
pm.
During a filter test
run
the aerosol or dust is fed into
the filter section after the determination of the size and
number concentration. The filtration velocity is con-
trolled via mass flow controller (FC) and pressure drop
79