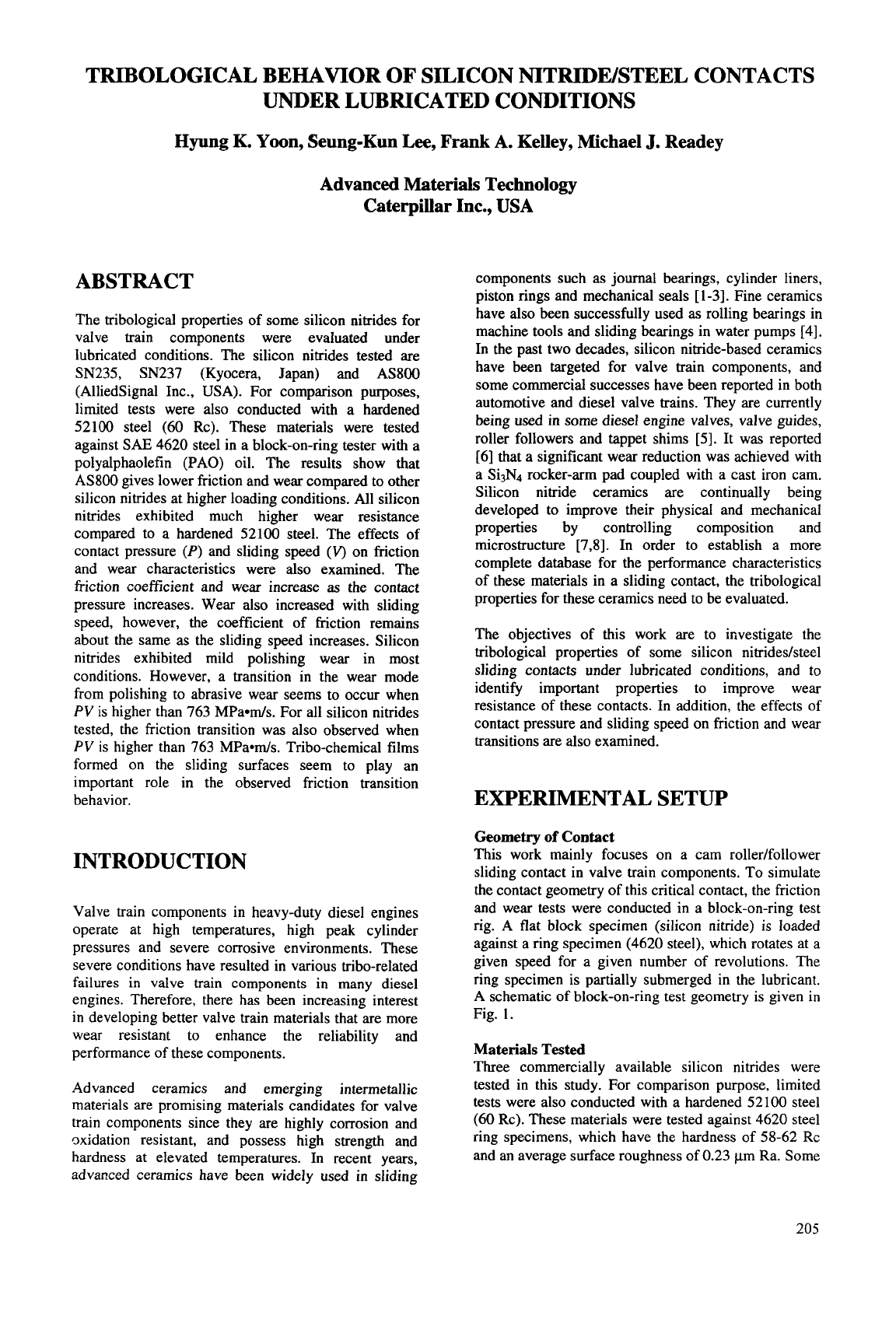
TRIBOLOGICAL BEHAVIOR
OF
SILICON NITRIDEBTEEL CONTACTS
UNDER LUBRICATED CONDITIONS
Hyung
K.
Yoon, Seung-Kun
Lee,
Frank
A.
Kelley, Michael
J.
Readey
Advanced
Materials
Technology
Caterpillar Inc.,
USA
ABSTRACT
The tribological properties of some silicon nitrides for
valve train components were evaluated under
lubricated conditions. The silicon nitrides tested are
SN235, SN237 (Kyocera, Japan) and AS800
(AlliedSignal Inc., USA). For comparison purposes,
limited tests were also conducted with a hardened
52100 steel (60 Rc). These materials were tested
against
SAE
4620 steel in a block-on-ring tester with a
polyalphaolefin (PAO) oil. The results show that
AS800 gives lower friction and wear compared to other
silicon nitrides at higher loading conditions. All silicon
nitrides exhibited much higher wear resistance
compared to a hardened 52100 steel. The effects of
contact pressure
(P)
and sliding speed
(V)
on friction
and wear characteristics were also examined. The
friction coefficient and wear increase
as
the contact
pressure increases. Wear also increased with sliding
speed, however, the coefficient of friction remains
about the same as the sliding speed increases. Silicon
nitrides exhibited mild polishing wear in most
conditions. However, a transition in the wear mode
from polishing to abrasive wear seems to occur when
PV
is higher than 763 MPa*m/s. For all silicon nitrides
tested, the friction transition was also observed when
PV
is higher than 763 MPa*m/s. Tribo-chemical films
formed on the sliding surfaces seem to play an
important role in the observed friction transition
behavior.
INTRODUCTION
Valve train components in heavy-duty diesel engines
operate at high temperatures, high peak cylinder
pressures and severe corrosive environments. These
severe conditions have resulted in various tribo-related
failures in valve train components in many diesel
engines. Therefore, there has been increasing interest
in
developing better valve train materials that are more
wear resistant to enhance
the
reliability and
performance of these components.
Advanced ceramics and emerging intermetallic
materials are promising materials candidates
for
valve
train components since they are highly corrosion and
oxidation resistant, and possess high strength and
hardness at elevated temperatures. In recent years,
advanced ceramics have been widely used in sliding
components such as journal bearings, cylinder liners,
piston rings and mechanical seals
[
1-31. Fine ceramics
have also been successfully used
as
rolling bearings in
machine tools and sliding bearings in water pumps 141.
In the past two decades, silicon nitride-based ceramics
have been targeted for valve train components, and
some commercial successes have been reported in both
automotive and diesel valve trains. They are currently
being used in some diesel engine valves, valve guides,
roller followers and tappet shims [5]. It was reported
[6]
that a significant wear reduction was achieved with
a Si3N4 rocker-arm pad coupled with a cast iron cam.
Silicon nitride ceramics are continually being
developed to improve their physical and mechanical
properties by controlling composition and
microstructure [7,8]. In order to establish a more
complete database for the performance characteristics
of these materials in a sliding contact, the tribological
properties for these ceramics need to be evaluated.
The objectives of this work are to investigate the
tribological properties of some silicon nitrideshteel
sliding contacts under lubricated conditions, and to
identify important properties to improve wear
resistance of these contacts. In addition, the effects of
contact pressure and sliding speed on friction and wear
transitions are also examined.
EXPERIMENTAL SETUP
Geometry
of
Contact
This work mainly focuses on a cam roller/follower
sliding contact in valve train components. To simulate
the contact geometry of this critical contact, the friction
and wear tests were conducted in a block-on-ring test
rig. A flat block specimen (silicon nitride) is loaded
against a ring specimen (4620 steel), which rotates at a
given speed for a given number of revolutions. The
ring specimen is partially submerged in the lubricant.
A
schematic
of
block-on-ring test geometry is given in
Fig.
1.
Materials
Tested
Three commercially available silicon nitrides were
tested in this study. For comparison purpose, limited
tests were also conducted with a hardened 52100 steel
(60 Rc). These materials were tested against 4620 steel
ring specimens, which have the hardness
of
58-62 Rc
and an average surface roughness of 0.23 pm Ra. Some
205