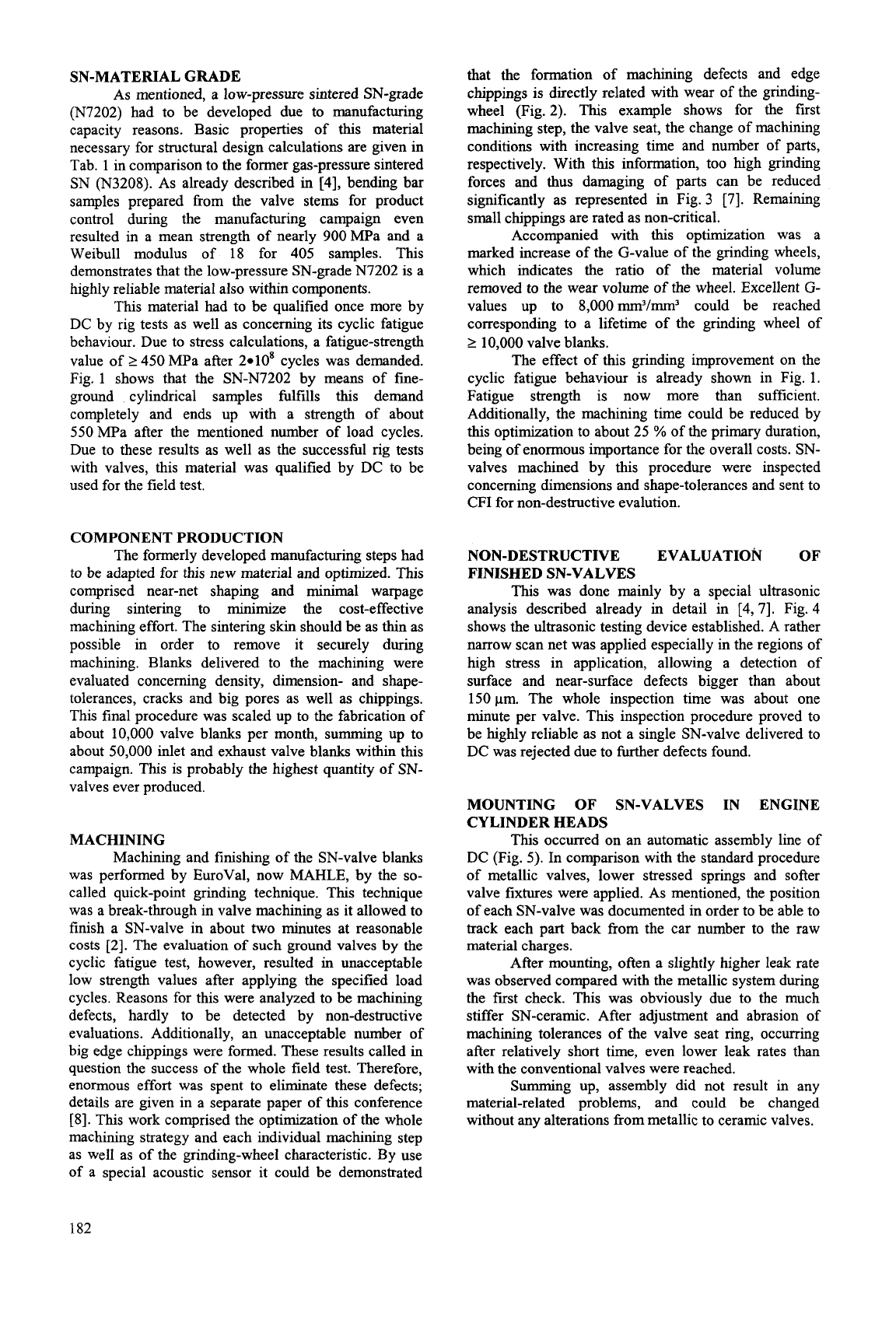
SN-MATERIAL GRADE
As mentioned, a low-pressure sintered SN-grade
(N7202) had to be developed due to manufacturing
capacity reasons. Basic properties of this material
necessary for structural design calculations are given in
Tab.
1
in comparison to the former gas-pressure sintered
SN (N3208). As already described
in
[4],
bending bar
samples prepared from the valve stems for product
control during the manufacturing campaign even
resulted in a mean strength of nearly
900
MPa and a
Weibull modulus of
18
for
405
samples.
This
demonstrates that the low-pressure SN-grade N7202 is a
highly reliable material also within components.
This material had to be qualified once more by
DC by rig tests as well as concerning its cyclic fatigue
behaviour. Due to stress calculations, a fatigue-strength
value of
2
450 MPa after 2-10' cycles was demanded.
Fig.
1
shows that the SN-N7202 by means of fine-
ground cylindrical samples fulfills
hs
demand
completely and ends up with a strength of about
550MPa after the mentioned number of load cycles.
Due to these results as well as the successful rig tests
with valves, this material was qualified by DC to be
used for the field test.
COMPONENT PRODUCTION
The formerly developed manufacturing steps had
to be adapted for this new material and optimized.
This
comprised near-net shaping and minimal warpage
during sintering to minimize the cost-effective
machining effort. The sintering skin should be as thin as
possible in order to remove it securely during
machining. Blanks delivered to the machining were
evaluated concerning density, dimension- and shape-
tolerances, cracks and big pores as well as chippings.
This final procedure was scaled up to the fabrication of
about 10,000 valve blanks per month, summing up to
about
50,000
inlet and exhaust valve blanks within this
campaign. Ths is probably the highest quantity of SN-
valves ever produced.
MACH IN IN G
Machining and finishmg of the SN-valve blanks
was performed by EuroVal, now MAHLE, by the
so-
called quick-point grinding technique. This technique
was a break-through in valve machining as it allowed to
finish a SN-valve in about
two
minutes at reasonable
costs
[2].
The evaluation of such ground valves by the
cyclic fatigue test, however, resulted in unacceptable
low strength values after applying the specified load
cycles. Reasons for thls were analyzed to be machining
defects, hardly to be detected by non-destructive
evaluations. Additionally, an unacceptable number of
big
edge chippings were formed. These results called in
question the success of the whole field test. Therefore,
enormous effort was spent to eliminate these defects;
details are given in a separate paper of this conference
[8].
This work comprised the optimization of the whole
machining strategy and each individual machining step
as well as of the grinding-wheel characteristic. By use
of a special acoustic sensor it could be demonstrated
that the formation of machming defects and edge
chippings
is
directly related with wear of the grinding-
wheel (Fig. 2).
This
example shows for the first
machining step, the valve seat, the change of machining
conditions with increasing time and number of parts,
respectively. With this information, too hgh grinding
forces and thus damaging of parts can be reduced
significantly as represented in Fig. 3 [7]. Remaining
small chippings are rated as non-critical.
Accompanied with this optimization was a
marked increase of the G-value of the grinding wheels,
which indicates the ratio of the material volume
removed to the wear volume of the wheel. Excellent
G-
values up to
8,000mm3/mm3
could be reached
corresponding to a lifetime of the grinding wheel of
2
10,000 valve blanks.
The effect of this grinding improvement on the
cyclic fatigue behaviour is already shown in Fig.
1.
Fatigue strength is now more than sufficient.
Additionally, the machining time could be reduced by
this optimization to about 25
%
of the primary duration,
being of enormous importance for the overall costs. SN-
valves machined by this procedure were inspected
concerning dimensions and shape-tolerances and sent to
CFI for non-destructive evalution.
NON-DESTRUCTIVE EVALUATION
OF
This
was done mainly by a special ultrasonic
analysis described already in detail in [4,7]. Fig.
4
shows the ultrasonic testing device established.
A
rather
narrow scan net was applied especially in the regions of
high stress in application, allowing a detection of
surface and near-surface defects bigger than about
150
pm. The whole inspection time was about one
minute per valve. Ths inspection procedure proved to
be highly reliable as not a single SN-valve delivered to
DC was rejected due to further defects found.
FINISHED SN-VALVES
MOUNTING
OF
SN-VALVES IN ENGINE
CYLINDER HEADS
This occurred on an automatic assembly line of
DC (Fig.
5).
In comparison with the standard procedure
of metallic valves, lower stressed springs and softer
valve fixtures were applied. As mentioned, the position
of each SN-valve was documented in order to be able to
track each part back from the car number to the raw
material charges.
After mounting, often a slightly higher leak rate
was observed compared with the metallic system during
the first check.
This
was obviously due to the much
stiffer SN-ceramic. After adjustment and abrasion of
machining tolerances of the valve seat ring, occurring
after relatively short time, even lower leak rates than
with the conventional valves were reached.
Summing up, assembly did not result in any
material-related problems, and could be changed
without any alterations from metallic to ceramic valves.
182