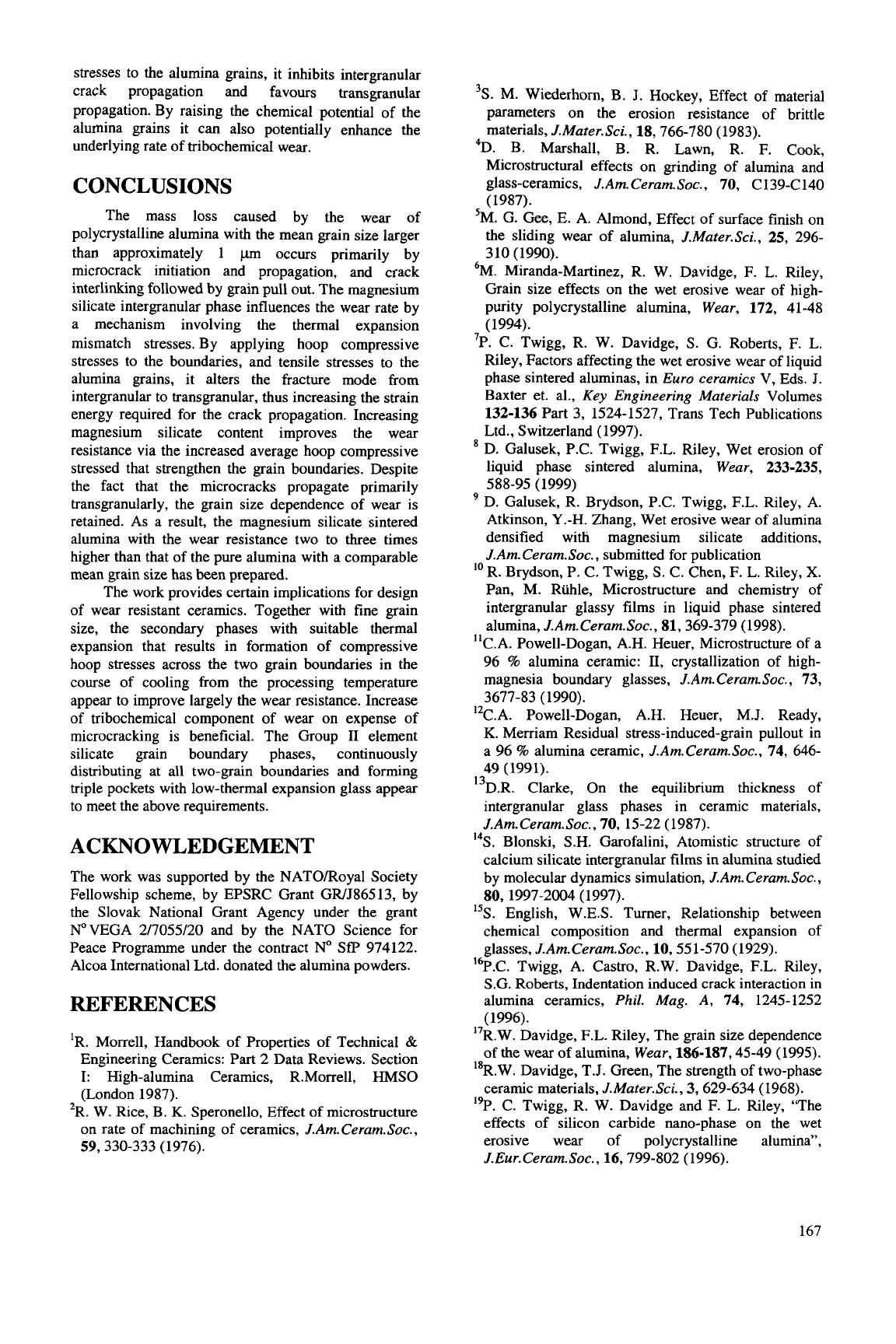
stresses to the alumina grains, it inhibits intergranular
crack propagation and favours transgranular
propagation. By raising the chemical potential
of
the
alumina grains it can also potentially enhance the
underlying rate
of
tribochemical wear.
CONCLUSIONS
The mass loss caused by the wear of
polycrystalline alumina with the mean grain size larger
than approximately 1 pm occurs primarily by
microcrack initiation and propagation, and crack
interlinking followed by grain pull out. The magnesium
silicate intergranular phase influences the wear rate by
a mechanism involving the thermal expansion
mismatch stresses. By applying hoop compressive
stresses to the boundaries, and tensile stresses to the
alumina grains, it alters the fracture mode from
intergranular to transgranular, thus increasing the strain
energy required for the crack propagation. Increasing
magnesium silicate content improves the wear
resistance via the increased average hoop compressive
stressed that strengthen the grain boundaries. Despite
the fact that the microcracks propagate primarily
transgranularly, the grain size dependence of wear is
retained. As a result, the magnesium silicate sintered
alumina with the wear resistance two to three times
higher than that of the pure alumina with a comparable
mean grain size has been prepared.
The work provides certain implications for design
of wear resistant ceramics. Together with fine grain
size, the secondary phases with suitable thermal
expansion that results in formation
of
compressive
hoop stresses across the two grain boundaries in the
course of cooling from the processing temperature
appear to improve largely the wear resistance. Increase
of tribochemical component of wear on expense of
microcracking is beneficial. The Group I1 element
silicate grain boundary phases, continuously
distributing at all two-grain boundaries and forming
triple pockets with low-thermal expansion glass appear
to meet the above requirements.
ACKNOWLEDGEMENT
The work was supported by the NATORoyal Society
Fellowship scheme, by EPSRC Grant GWJ86513, by
the Slovak National Grant Agency under the grant
NOVEGA
2/7055/20 and by the NATO Science for
Peace Programme under the contract No
SfP
974122.
Alcoa International Ltd. donated the alumina powders.
REFERENCES
'R. Morrell, Handbook of Properties of Technical
&
Engineering Ceramics: Part 2 Data Reviews. Section
I: High-alumina Ceramics, R.Morrel1,
HMSO
(London 1987).
*R. W. Rice, B.
K.
Speronello, Effect of microstructure
on rate of machining of ceramics,
J.Am.Ceram.Soc.,
59,330-333 (1976).
3S.
M. Wiederhorn, B.
J.
Hockey, Effect of material
parameters on the erosion resistance
of
brittle
materials,
J.Muter.Sci.,
18, 766-780 (1983).
4
D. B. Marshall,
B.
R. Lawn, R. F. Cook,
Microstructural effects on grinding of alumina and
glass-ceramics,
J.Am. Ceram.Soc.,
70, C139-C140
(1987).
5M. G. Gee,
E.
A. Almond, Effect of surface finish on
the sliding wear of alumina,
J.Mater.Sci.,
25, 296-
310 (1990).
%.
Miranda-Martinez,
R.
W. Davidge, F. L. Riley,
Grain size effects on the wet erosive wear
of
high-
pwity polycrystalline alumina,
Wear,
172, 41-48
(1994).
7
P.
C. Twigg, R. W. Davidge,
S.
G. Roberts, F.
L.
Riley, Factors affecting the wet erosive wear of liquid
phase sintered aluminas, in
Euro ceramics
V, Eds.
J.
Baxter et. al.,
Key
Engineering Materials
Volumes
132-136 Part 3, 1524-1527, Trans Tech Publications
Ltd., Switzerland (1997).
D. Galusek, P.C. Twigg, F.L. Riley, Wet erosion of
liquid phase sintered alumina,
Wear,
233-235,
D. Galusek, R. Brydson, P.C. Twigg, F.L. Riley, A.
Atkinson, Y.-H. Zhang, Wet erosive wear of alumina
densified with magnesium silicate additions,
J.Am. Ceram.Soc..
submitted for Dublication
588-95 (1999)
lo
R. Brydson, P. C: Twigg,
S.
C. khen, F. L. Riley,
X.
Pan, M. Riihle, Microstructure and chemistry of
intergranular glassy films in liquid phase sintered
alumina,
J.Am. Ceram.Soc.,
81,369-379 (1998).
C.A. Powell-Dogan, A.H. Heuer, Microstructure of a
96
%
alumina ceramic: 11, crystallization of high-
magnesia boundary
glasses,
J.Am. Ceram. Soc.,
73,
C.A. Powell-Dogan, A.H. Heuer, M.J. Ready,
K.
Merriam Residual stress-induced-grain pullout in
a 96
%
alumina ceramic,
J.Am.Ceram.Soc.,
74, 646-
49 (1991).
D.R. Clarke, On the equilibrium thickness of
intergranular glass phases in ceramic materials,
J.Am.Ceram.Soc.,
70, 15-22 (1987).
I4S.
Blonski,
S.H.
Garofalini, Atomistic structure of
calcium silicate intergranular films in alumina studied
by molecular dynamics simulation,
J.Am. Cerum.Soc.,
"S. English, W.E.S. Turner, Relationship between
chemical composition and thermal expansion of
glasses,
J.Am.Cerum.Soc.,
10,551-570 (1929).
6p.C.
Twigg,
A.
Castro, R.W. Davidge, F.L. Riley,
S.G. Roberts, Indentation induced crack interaction in
alumina ceramics,
Phil.
Mag.
A,
74, 1245-1252
(1996).
"R.W. Davidge, F.L. Riley, The grain size dependence
of the wear of alumina,
Wear,
186-187,45-49 (1995).
"R.W. Davidge,
T.J.
Green, The strength of two-phase
ceramic materials,
J.Mater.Sci.,
3, 629-634 (1968).
'%.
C. Twigg, R. W. Davidge and F. L. Riley, "The
effects of silicon carbide nano-phase on the
wet
erosive wear of polycrystalline alumina",
J.Eur.Ceram.Soc.,
16,799-802 (1996).
11
3677-83 (1990).
12
13
80,
1997-2004 (1997).
1
167