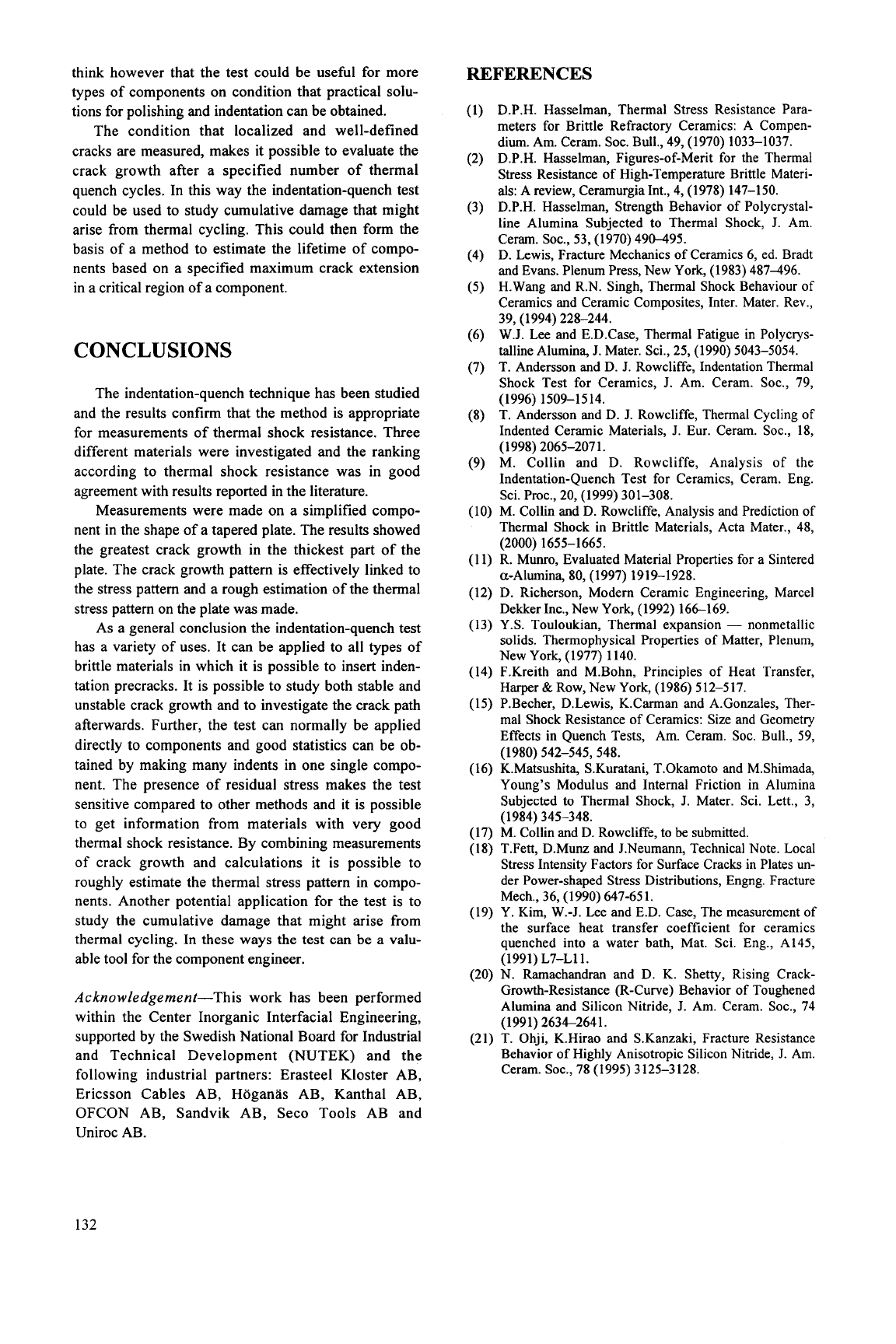
think however that the test could be useful for more
types of components on condition that practical
solu-
tions for polishing and indentation can be obtained.
The condition that localized and well-defined
cracks are measured, makes it possible
to
evaluate the
crack growth after a specified number
of
thermal
quench cycles. In this way the indentation-quench test
could be used
to
study cumulative damage that might
arise from thermal cycling. This could then form the
basis of a method
to
estimate the lifetime of compo-
nents based on a specified maximum crack extension
in a critical region
of
a
component.
CONCLUSIONS
The indentation-quench technique has been studied
and the results confirm that the method is appropriate
for measurements of thermal shock resistance. Three
different materials were investigated and the ranking
according to thermal shock resistance was in good
agreement with results reported in the literature.
Measurements were made on
a
simplified compo-
nent in the shape of
a
tapered plate. The results showed
the greatest crack growth in the thickest part
of
the
plate. The crack growth pattern is effectively linked to
the stress pattern and a rough estimation of the thermal
stress pattern on the plate was made.
As a general conclusion the indentation-quench
test
has a variety of uses. It can be applied
to all
types
of
brittle materials in which it is possible to insert inden-
tation precracks. It is possible to study both stable and
unstable crack growth and
to
investigate the crack path
afterwards. Further, the test can normally be applied
directly to components and good statistics can be ob-
tained by making many indents in one single compo-
nent. The presence of residual stress makes the
test
sensitive compared
to
other methods and it is possible
to get information from materials with very good
thermal shock resistance. By combining measurements
of crack growth and calculations it is possible to
roughly estimate the thermal stress pattern in compo-
nents. Another potential application for the test is to
study the cumulative damage that might arise from
thermal cycling. In these ways the
test
can be
a
valu-
able tool for the component engineer.
Acknowledgement-This work has been performed
within the Center Inorganic Interfacial Engineering,
supported by the Swedish National Board for Industrial
and Technical Development (NUTEK) and the
following industrial partners: Erasteel Kloster AB,
Ericsson Cables AB, Hoganas AB, Kanthal AB,
OFCON
AB, Sandvik AB, Seco Tools AB and
Uniroc AB.
D.P.H. Hasselman, Thermal Stress Resistance Para-
meters for Brittle Refractory Ceramics: A Compen-
dium. Am. Ceram. SOC. Bull.,
49, (1970) 1033-1037.
D.P.H. Hasselman, Figures-of-Merit for the Thermal
Stress Resistance of High-Temperature Brittle Materi-
als:
A review, Ceramurgia Int.,
4, (1978) 147-150.
D.P.H. Hasselman, Strength Behavior of Polycrystal-
line Alumina Subjected to Thermal Shock,
J.
Am.
Ceram. SOC.,
53,
(1970) 490-495.
D.
Lewis, Fracture Mechanics of Ceramics
6,
ed. Bradt
and Evans. Plenum Press, New York,
(1983) 487-496.
H.Wang and R.N. Singh, Thermal Shock Behaviour
of
Ceramics and Ceramic Composites, Inter. Mater. Rev.,
W.J. Lee and E.D.Case, Thermal Fatigue
in
Polycrys-
talline Alumina,
J.
Mater. Sci.,
25, (1990) 5043-5054.
T. Anderson and D. J. Rowcliffe, Indentation Thermal
Shock Test for Ceramics, J. Am. Ceram. SOC.,
79,
(1996) 150S15 14.
T. Anderson and D. J. Rowcliffe, Thermal Cycling of
Indented Ceramic Materials, J. Eur. Ceram. SOC., 18,
M. Collin and D. Rowcliffe, Analysis
of
the
Indentation-Quench Test for Ceramics, Ceram. Eng.
Sci. Proc.,
20, (1999) 301-308.
M. Collin and D. Rowcliffe, Analysis and Prediction of
Thermal Shock in Brittle Materials, Acta Mater.,
48,
R. Munro, Evaluated Material Properties for a Sintered
a-Alumina,
80,
(1997) 1919-1928.
D. Richerson, Modern Ceramic Engineering, Marcel
Dekker Inc., New York,
(1992) 166-169.
Y.S. Touloukian, Thermal expansion
-
nonmetallic
solids. Thermophysical Properties of Matter, Plenum,
New York,
(1977) 1140.
F.Kreith and M.Bohn, Principles of Heat Transfer,
Harper
&
Row, New York,
(1986) 512-517.
P.Becher, D.Lewis, K.Carman and A.Gonzales, Ther-
mal Shock Resistance of Ceramics: Size and Geometry
Effects in Quench Tests, Am. Ceram. SOC. Bull.,
59,
K.Matsushita, S.Kuratani, T.Okamoto and M.Shimada,
Young’s Modulus and Internal Friction in Alumina
Subjected to Thermal Shock,
J.
Mater. Sci. Lett.,
3,
M. Collin and D. Rowcliffe, to
be
submitted.
T.Fett, D.Munz and J.Neumann, Technical Note. Local
Stress Intensity Factors for Surface Cracks
in
Plates un-
der Power-shaped Stress Distributions, Engng. Fracture
Mech.,
36, (1990) 647-65
1.
Y. Kim, W.-J. Lee and E.D. Case, The measurement
of
the surface heat transfer coefficient for ceramics
quenched into a water bath, Mat. Sci. Eng., A145,
N. Ramachandran and D. K. Shetty, Rising Crack-
Growth-Resistance (R-Curve) Behavior of Toughened
Alumina and Silicon Nitride, J. Am. Ceram. SOC.,
74
(1991) 26362641.
T. Ohji, K.Hirao and S.Kanzaki, Fracture Resistance
Behavior
of
Highly Anisotropic Silicon Nitride,
J.
Am.
Ceram. SOC.,
78 (1995) 3125-3128.
39, (1994) 228-244.
(1998) 2065-207 1.
(2000) 1655-1 665.
(1980) 542-545,548.
(1984) 345-348.
(1991) L7-Lll.
132