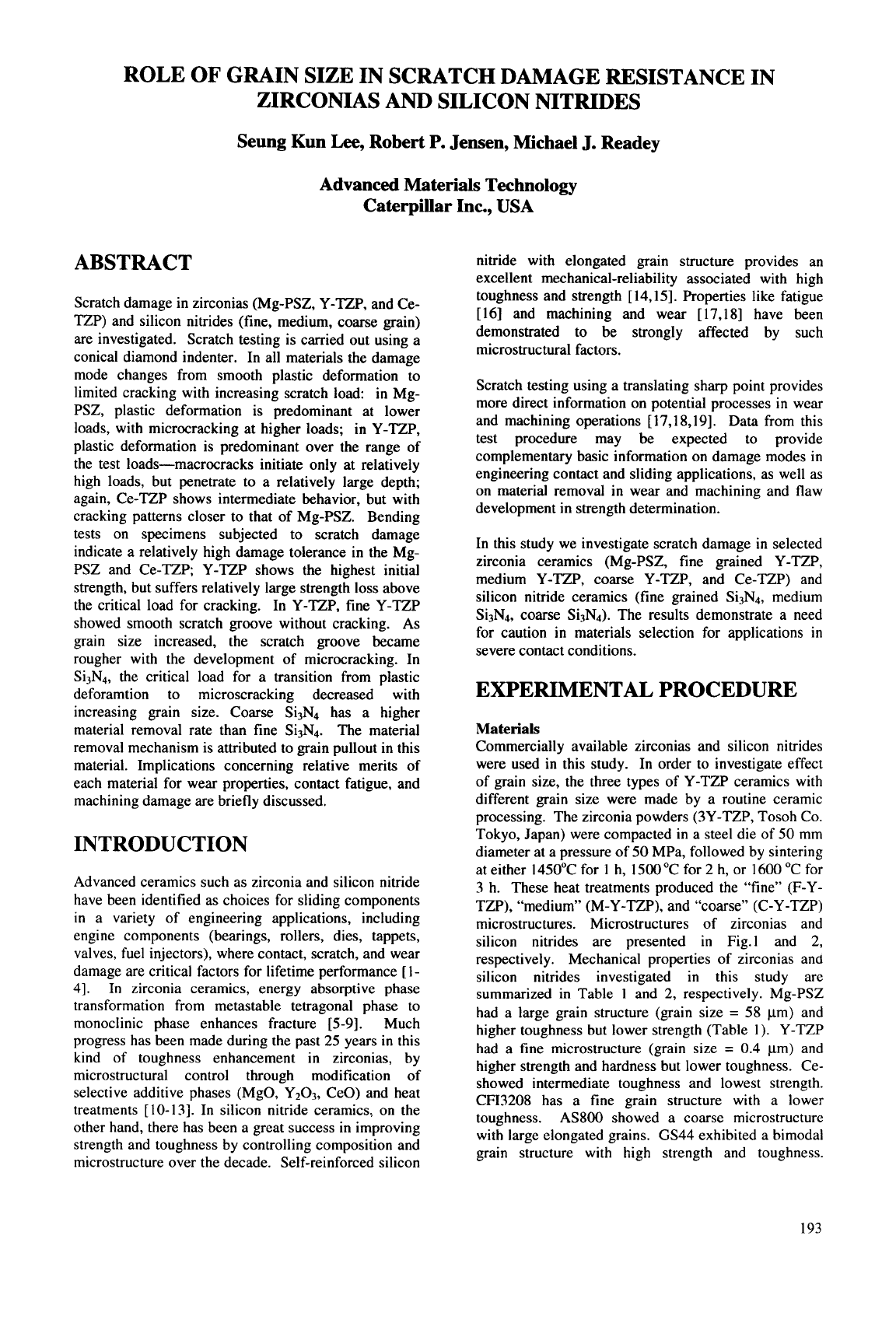
ROLE
OF
GRAIN SIZE IN SCRATCH DAMAGE RESISTANCE IN
ZIRCONIAS AND SILICON NITRIDES
Seung Kun
Lee,
Robert
P.
Jensen, Michael
J.
Readey
Advanced Materials Technology
Caterpillar Inc.,
USA
ABSTRACT
Scratch damage
in
zirconias (Mg-PSZ, Y-TZP, and Ce-
TZP) and silicon nitrides (fine, medium, coarse grain)
are investigated. Scratch testing is carried out using a
conical diamond indenter. In all materials the damage
mode changes from smooth plastic deformation to
limited cracking with increasing scratch load: in Mg-
PSZ, plastic deformation is predominant at lower
loads, with microcracking at higher loads; in Y-TZP,
plastic deformation is predominant over the range of
the test loads-macrocracks initiate only at relatively
high loads, but penetrate to a relatively large depth;
again, Ce-TZP shows intermediate behavior, but with
cracking patterns closer to that of Mg-PSZ. Bending
tests on specimens subjected to scratch damage
indicate a relatively high damage tolerance in the Mg-
PSZ and Ce-TZP; Y-TZP shows the highest initial
strength, but suffers relatively large strength loss above
the critical load for cracking. In Y-TZP,
fine
Y-TZP
showed smooth scratch groove without cracking.
As
grain size increased, the scratch groove became
rougher with the development of microcracking. In
Si3N4, the critical load for a transition from plastic
deforamtion to microscracking decreased with
increasing grain size. Coarse Si3N4 has a higher
material removal rate than fine Si3N4. The material
removal mechanism is attributed
to
grain pullout in this
material. Implications concerning relative merits of
each material for wear properties, contact fatigue, and
machining damage are briefly discussed.
INTRODUCTION
Advanced ceramics such as zirconia and silicon nitride
have been identified as choices for sliding components
in
a variety of engineering applications, including
engine components (bearings, rollers, dies, tappets,
valves, fuel injectors), where contact, scratch, and wear
damage are critical factors for lifetime performance
[
1
-
41.
In zirconia ceramics, energy absorptive phase
transformation from metastable tetragonal phase to
monoclinic phase enhances fracture [5-91. Much
progress has been made during the past 25 years
in
this
kind of toughness enhancement
in
zirconias, by
microstructural control through modification of
selective additive phases (MgO, Y203, CeO) and heat
treatments
[
10-
131. In silicon nitride ceramics, on the
other hand, there has been a great success
in
improving
strength and toughness by controlling composition and
microstructure over the decade. Self-reinforced silicon
nitride with elongated grain structure provides an
excellent mechanical-reliability associated with high
toughness and strength
[
14,151. Properties like fatigue
[16] and machining and wear [17,18] have been
demonstrated to be strongly affected by such
microstructural factors.
Scratch testing using a translating sharp point provides
more direct information on potential processes
in
wear
and machining operations [17,18,19]. Data from this
test procedure may be expected to provide
complementary basic information on damage modes
in
engineering contact and sliding applications, as well as
on material removal
in
wear and machining and flaw
development in strength determination.
In this study we investigate scratch damage
in
selected
zirconia ceramics (Mg-PSZ, fine grained Y-TZP,
medium Y-TZP, coarse Y-TZP, and Ce-TZP) and
silicon nitride ceramics (fine grained Si3N4, medium
Si3N4, coarse Si3N4). The results demonstrate a need
for caution
in
materials selection for applications
in
severe contact conditions.
EXPERIMENTAL PROCEDURE
Materials
Commercially available zirconias and silicon nitrides
were used
in
this study.
In order to investigate effect
of grain size, the three types of Y-TZP ceramics with
different grain size were made by a routine ceramic
processing. The zirconia powders (3Y-TZP, Tosoh Co.
Tokyo, Japan) were compacted
in
a steel die of 50
mm
diameter at a pressure of 50 MPa, followed by sintering
at either 1450°C for
1
h, 150O0C for 2 h,
or
1600 OC for
3
h.
These heat treatments produced the “fine” (F-Y-
TZP), “medium” (M-Y-TZP), and “coarse” (C-Y-TZP)
microstructures. Microstructures of zirconias and
silicon nitrides are presented
in
Fig.1 and 2,
respectively.
Mechanical properties of zirconias and
silicon nitrides investigated
in
this study are
summarized
in
Table
1
and
2,
respectively. Mg-PSZ
had a large grain structure (grain size
=
58
pm)
and
higher toughness but lower strength (Table 1). Y-TZP
had a fine microstructure (grain size
=
0.4
pm)
and
higher strength and hardness but lower toughness. Ce-
showed intermediate toughness and lowest strength.
CFI3208 has a fine grain structure with
a
lower
toughness.
AS800 showed a coarse microstructure
with large elongated grains.
GS44
exhibited a bimodal
grain structure with high strength and toughness.
193