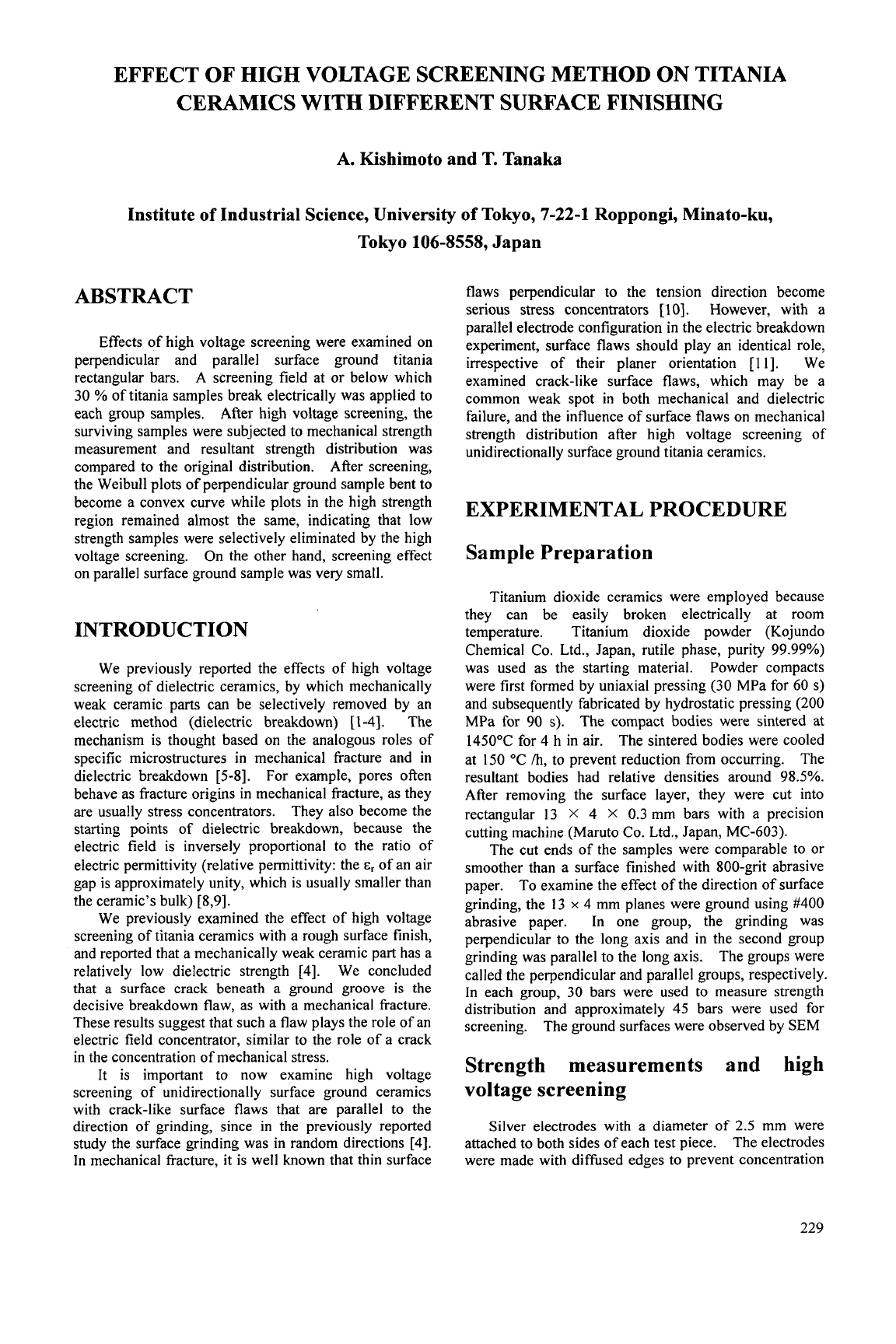
EFFECT OF HIGH VOLTAGE SCREENING METHOD ON TITANIA
CERAMICS
WITH
DIFFERENT SURFACE FINISHING
A. Kishimoto and
T.
Tanaka
Institute
of
Industrial Science, University
of
Tokyo,
7-22-1 Roppongi, Minato-ku,
Tokyo 106-8558, Japan
ABSTRACT
Effects of high voltage screening were examined on
perpendicular and parallel surface ground titania
rectangular bars.
A
screening field at or below which
30
%
of titania samples break electrically was applied to
each group samples. After high voltage screening, the
surviving samples were subjected to mechanical strength
measurement and resultant strength distribution was
compared to the original distribution. After screening,
the Weibull plots
of
perpendicular ground sample bent to
become a convex curve while plots in the high strength
region remained almost the same, indicating that low
strength samples were selectively eliminated by the high
voltage screening. On the other hand, screening effect
on parallel surface ground sample was very small.
INTRODUCTION
We previously reported the effects of high voltage
screening of dielectric ceramics, by which mechanically
weak ceramic parts can be selectively removed by an
electric method (dielectric breakdown)
[
1-41. The
mechanism is thought based on the analogous roles of
specific microstructures in mechanical fracture and in
dielectric breakdown [5-81. For example, pores often
behave as fracture origins in mechanical fracture, as they
are usually stress concentrators. They also become the
starting points of dielectric breakdown, because the
electric field is inversely proportional to the ratio of
electric permittivity (relative permittivity: the
E,
of an air
gap is approximately unity, which is usually smaller than
the ceramic's bulk) [8,9].
We previously examined the effect of high voltage
screening of titania ceramics with a rough surface finish,
and reported that a mechanically weak ceramic part has a
relatively low dielectric strength [4]. We concluded
that a surface crack beneath a ground groove
is
the
decisive breakdown flaw, as with a mechanical fracture.
These results suggest that such a flaw plays the role of an
electric field concentrator, similar to the role of a crack
in the concentration of mechanical stress.
It is important to now examine high voltage
screening of unidirectionally surface ground ceramics
with crack-like surface flaws that are parallel to the
direction of grinding, since in the previously reported
study the surface grinding was in random directions [4].
In mechanical fracture, it is well known that thin surface
flaws perpendicular to the tension direction become
serious
stress
concentrators [lo]. However, with a
parallel electrode configuration in the electric breakdown
experiment, surface flaws should play an identical role,
irrespective of their planer orientation
[
1
11.
We
examined crack-like surface flaws, which may be a
common weak spot in both mechanical and dielectric
failure, and the influence
of
surface flaws on mechanical
strength distribution after high voltage screening
of
unidirectionally surface ground titania ceramics.
EXPERIMENTAL PROCEDURE
Sample Preparation
Titanium dioxide ceramics were employed because
they can be easily broken electrically at room
temperature. Titanium dioxide powder (Kojundo
Chemical Co. Ltd., Japan, rutile phase, purity 99.99%)
was used as the starting material. Powder compacts
were first formed by uniaxial pressing
(30
MPa for 60
s)
and subsequently fabricated by hydrostatic pressing
(200
MPa for 90
s).
The compact bodies were sintered at
1450°C for 4 h in air. The sintered bodies were cooled
at
150
"C
/h,
to prevent reduction from occurring. The
resultant bodies had relative densities around 98.5%.
After removing the surface layer, they were cut into
rectangular 13
X
4
X
0.3 mm bars with a precision
cutting machine (Maruto Co. Ltd., Japan, MC-603).
The cut ends of the samples were comparable to or
smoother than a surface finished with 800-grit abrasive
paper. To examine the effect
of
the direction of surface
grinding, the
13
x
4
mm planes were ground using #400
abrasive paper. In one group, the grinding was
perpendicular to the long axis and in the second group
grinding was parallel to the long axis. The groups were
called the perpendicular and parallel groups, respectively.
In each group,
30
bars were used
to
measure strength
distribution and approximately 45 bars were used for
screening. The ground surfaces were observed by SEM
Strength measurements and high
voltage screening
Silver electrodes with a diameter of
2.5
mm were
attached to both sides of each test piece. The electrodes
were made with diffused edges to prevent concentration
229