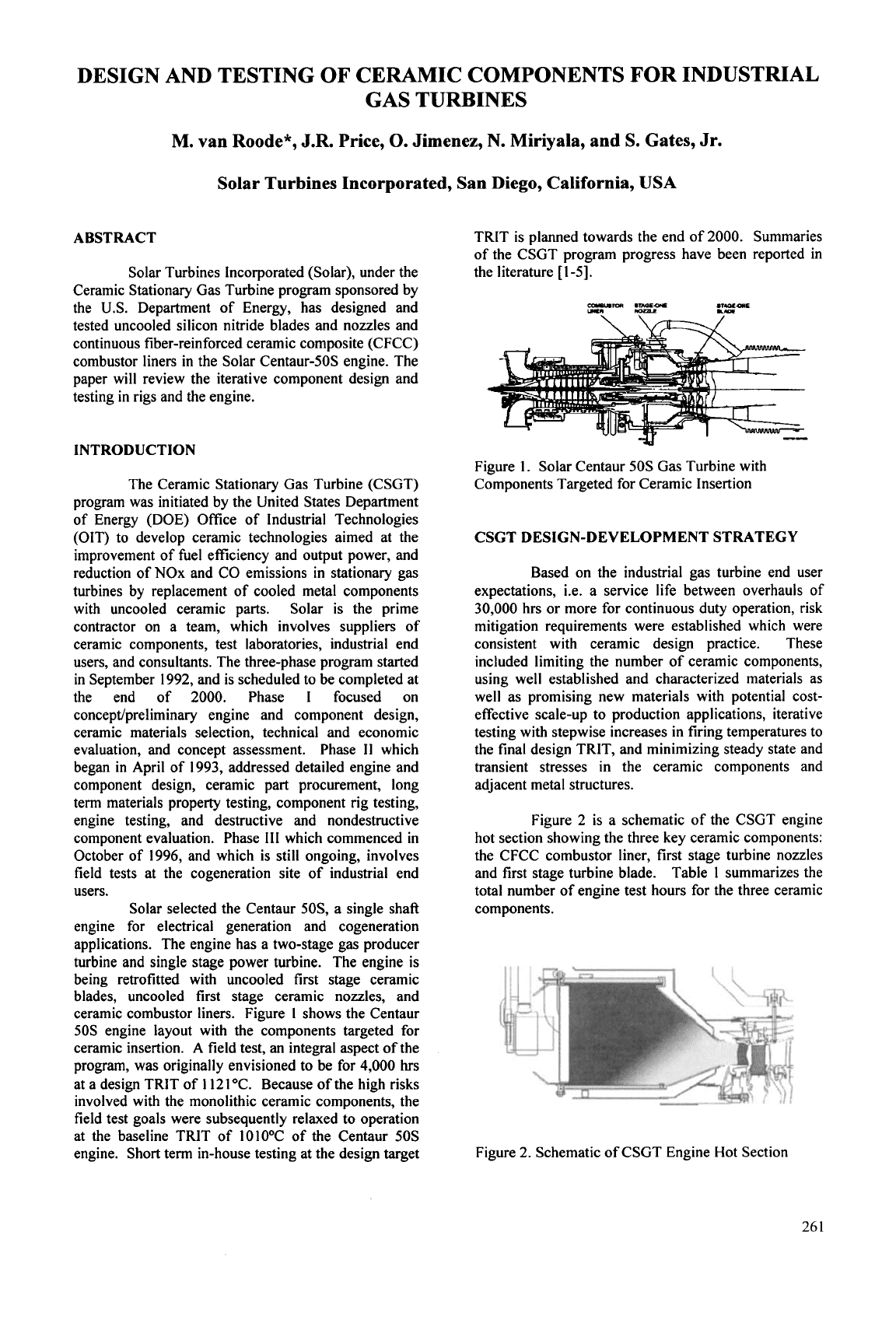
DESIGN AND TESTING
OF
CERAMIC COMPONENTS
FOR
INDUSTRIAL
GAS TURBINES
M. van Roode*, J.R. Price,
0.
Jimenez,
N.
Miriyala, and
S.
Gates,
Jr.
Solar Turbines Incorporated, San
Diego,
California,
USA
ABSTRACT
Solar Turbines Incorporated (Solar), under the
Ceramic Stationary Gas Turbine program sponsored by
the U.S. Department of Energy, has designed and
tested uncooled silicon nitride blades and nozzles and
continuous fiber-reinforced ceramic composite (CFCC)
combustor liners in the Solar Centaur-50s engine. The
paper will review the iterative component design and
testing
in
rigs and the engine.
INTRODUCTION
The Ceramic Stationary Gas Turbine (CSGT)
program was initiated by the United States Department
of Energy (DOE) Office of Industrial Technologies
(OIT) to develop ceramic technologies aimed at the
improvement of fuel efficiency and output power, and
reduction of
NOx
and CO emissions in stationary gas
turbines by replacement of cooled metal components
with uncooled ceramic parts. Solar is the prime
contractor on a team, which involves suppliers of
ceramic components, test laboratories, industrial end
users, and consultants. The three-phase program started
in
September 1992, and is scheduled to be completed at
the end of
2000.
Phase
I
focused on
concept/preliminary engine and component design,
ceramic materials selection, technical and economic
evaluation, and concept assessment. Phase
I1
which
began
in
April of 1993, addressed detailed engine and
component design, ceramic part procurement, long
term materials property testing, component rig testing,
engine testing, and destructive and nondestructive
component evaluation. Phase
Ill
which commenced
in
October of 1996, and which is still ongoing, involves
field tests at the cogeneration site of industrial end
users.
Solar selected the Centaur
50S,
a single shaft
engine for electrical generation and cogeneration
applications. The engine has a two-stage gas producer
turbine and single stage power turbine. The engine is
being retrofitted with uncooled first stage ceramic
blades, uncooled first stage ceramic nozzles, and
ceramic combustor liners. Figure
I
shows the Centaur
50s
engine layout with the components targeted for
ceramic insertion.
A
field test, an integral aspect of the
program, was originally envisioned to be for
4,000
hrs
at a design TRIT of
1
121OC. Because of the high risks
involved with the monolithic ceramic components, the
field test goals were subsequently relaxed to operation
at the baseline TRIT of 10IO°C of the Centaur 50s
engine. Short term in-house testing at the design target
TRIT is planned towards the end of
2000.
Summaries
of the CSGT program progress have been reported in
the literature [l-51.
Figure
I.
Solar Centaur
50s
Gas
Turbine with
Components Targeted for Ceramic Insertion
CSGT DESIGN-DEVELOPMENT STRATEGY
Based on the industrial gas turbine end user
expectations, i.e. a service life between overhauls of
30,000
hrs or more for continuous duty operation, risk
mitigation requirements were established which were
consistent with ceramic design practice. These
included limiting the number of ceramic components,
using well established and characterized materials as
well as promising new materials with potential cost-
effective scale-up to production applications, iterative
testing with stepwise increases in firing temperatures to
the final design TRIT, and minimizing steady state and
transient stresses in the ceramic components and
adjacent metal structures.
Figure
2
is a schematic of the CSGT engine
hot section showing the three key ceramic components:
the CFCC combustor liner, first stage turbine nozzles
and first stage turbine blade. Table
1
summarizes the
total number of engine test hours for the three ceramic
components.
Figure
2.
Schematic of CSGT Engine Hot Section
26
1