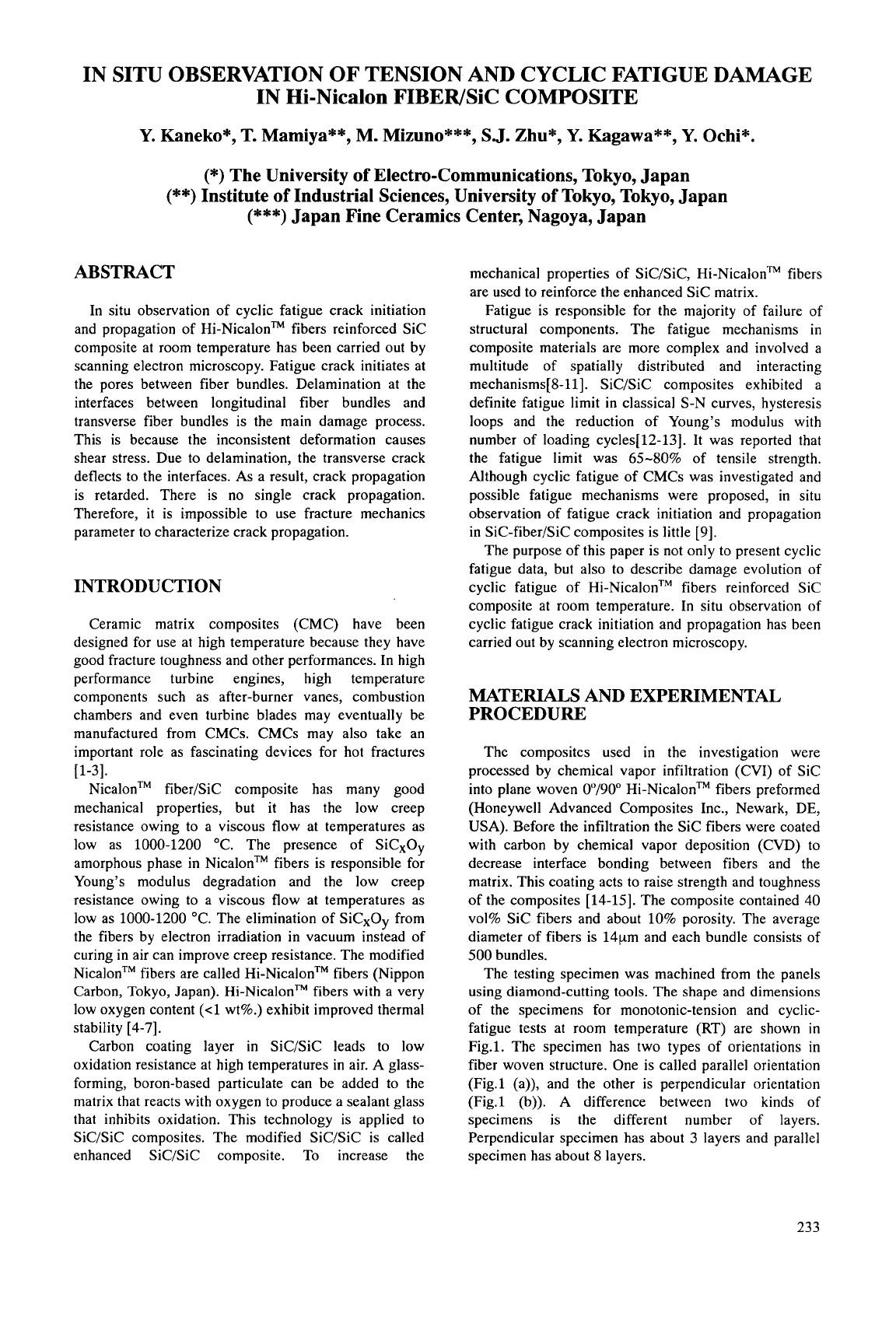
IN SITU OBSERVATION OF TENSION AND CYCLIC FATIGUE DAMAGE
IN Hi-Nicalon FIBEWSiC COMPOSITE
Y.
Kaneko", T. Mamiya**, M. Mizuno***,
SJ.
Zhu*,
Y.
Kagawa**,
Y.
Ochi*.
(*)
The University
of
Electro-Communications, Tokyo, Japan
(**)
Institute
of
Industrial Sciences, University
of
Tokyo, Tokyo, Japan
(***)
Japan Fine Ceramics Center, Nagoya, Japan
ABSTRACT
In
situ observation of cyclic fatigue crack initiation
and propagation of Hi-NicalonTM fibers reinforced Sic
composite at room temperature has been carried out by
scanning electron microscopy. Fatigue crack initiates at
the pores between fiber bundles. Delamination at the
interfaces between longitudinal fiber bundles and
transverse fiber bundles is the main damage process.
This is because the inconsistent deformation causes
shear stress. Due
to
delamination, the transverse crack
deflects to the interfaces. As a result, crack propagation
is retarded. There
is
no
single crack propagation.
Therefore,
it
is impossible
to
use fracture mechanics
parameter to characterize crack propagation.
INTRODUCTION
Ceramic matrix composites (CMC) have been
designed for use at high temperature because they have
good fracture toughness and other performances.
In
high
performance turbine engines, high temperature
components such as after-burner vanes, combustion
chambers and even turbine blades may eventually be
manufactured from CMCs. CMCs may also take an
important role as fascinating devices for hot fractures
NicalonTM fiber/SiC composite has many good
mechanical properties, but it has the low creep
resistance owing to a viscous flow at temperatures as
low as 1000-1200 "C. The presence of SiCxOy
amorphous phase in NicalonTM fibers
is
responsible for
Young's modulus degradation and the low creep
resistance owing to a viscous flow at temperatures as
low as 1000-1200 "C. The elimination of SiCxOy from
the fibers by electron irradiation in vacuum instead of
curing in air can improve creep resistance. The modified
NicalonTM fibers are called Hi-NicalonTM fibers (Nippon
Carbon, Tokyo, Japan). Hi-NicalonTM fibers with a very
low oxygen content (c1 wt%.) exhibit improved thermal
stability [4-71.
Carbon coating layer in SiC/SiC leads to low
oxidation resistance at high temperatures in air. A glass-
forming, boron-based particulate can be added
to
the
matrix that reacts with oxygen
to
produce a sealant glass
that inhibits oxidation. This technology
is
applied
to
SiC/SiC composites. The modified SiC/SiC is called
enhanced SiC/SiC composite.
To
increase the
[l-31.
mechanical properties of SiC/SiC, Hi-NicalonTM fibers
are used
to
reinforce the enhanced
Sic
matrix.
Fatigue
is
responsible for the majority of failure
of
structural components. The fatigue mechanisms
in
composite materials are more complex and involved a
multitude of spatially distributed and interacting
mechanisms[8-11]. SiC/SiC composites exhibited a
definite fatigue limit in classical S-N curves, hysteresis
loops and the reduction of Young's modulus with
number of loading cycles[12-131. It was reported that
the fatigue limit was
65-80%
of tensile strength.
Although
cyclic
fatigue of CMCs was investigated and
possible fatigue mechanisms were proposed, in situ
observation of fatigue crack initiation and propagation
in Sic-fiber/SiC composites
is
little [9].
The purpose of this paper is not only to present cyclic
fatigue data, but also to describe damage evolution of
cyclic fatigue of Hi-NicalonTM fibers reinforced Sic
composite at room temperature.
In
situ observation of
cyclic
fatigue crack initiation and propagation has been
carried out by scanning electron microscopy.
MATERIALS AND EXPERIMENTAL
PROCEDURE
The composites used in the investigation were
processed by chemical vapor infiltration (CVI) of Sic
into plane woven 0"/90" Hi-NicalonTM fibers preformed
(Honeywell Advanced Composites Inc., Newark,
DE,
USA). Before the infiltration the Sic fibers were coated
with carbon by chemical vapor deposition (CVD) to
decrease interface bonding between fibers and the
matrix. This coating acts to raise strength and toughness
of the composites [14-151. The composite contained 40
vol% Sic fibers and about 10% porosity. The average
diameter of fibers is 14pm and each bundle consists of
500
bundles.
The testing specimen was machined from the panels
using diamond-cutting tools. The shape and dimensions
of the specimens for monotonic-tension and cyclic-
fatigue tests at room temperature (RT) are shown in
Fig.1. The specimen has two types of orientations in
fiber woven structure. One
is
called parallel orientation
(Fig.1 (a)), and the other is perpendicular orientation
(Fig.1 (b)).
A
difference between two kinds of
specimens
is
the different number of layers.
Perpendicular specimen has about
3
layers and parallel
specimen has about
8
layers.
233