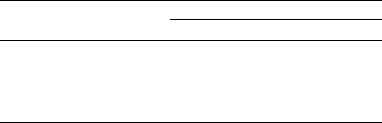
decarburized side will be softer than the side
that did not undergo decarburizing, which is
harder. The greater amount of martensite
leads to distortion.The solution to this pro-
blem is to restore carbon into the furnace
atmosphere or machine off the decarburized
layer.
The third surface-related condition that may
lead to cracking or material weakening is the
formation of surface seams or nonmetallic
inclusions, which may occur in hot rolled or cold
finished material. The presence of these defects
prevent the hot steel from welding to itself dur-
ing the forging process, for example, creating a
stress raiser. To prevent this problem with hot
rolled bars, stock should be removed before heat
treatment. Recommendations made earlier by
Kern are provided in Table 7 (Ref 22).
Although not a published standard, Kern has
reported that a seam or nonmetallic depth of
0.025 mm/3.3 mm (0.001 in./0.13 in.) diameter
maximum is usually acceptable for cold finished
bars (Ref 22). If the seam depth is excessive, it is
recommended that the bars be magniflux in-
spected prior to heat treatment.
Heating and Atmosphere Control. An
important source of steel distortion and cracking
is nonuniform heating and not using the appro-
priate protective atmosphere. For example, if
steel is heated in a direct-gas-fired furnace with
high moisture content, the load being heated
may adsorb hydrogen, leading to hydrogen
embrittlement and subsequent cracking that
would not normally occur with a dry atmosphere
(Ref 19, 26).
One source of distortion is when a part is in
contact with the furnace hearth during heating,
which may produce sufficient nonuniform tem-
perature distribution within the part. This will
occur because the portion of the part in contact
with the furnace hearth will be heated con-
ductively much faster than the remainder of the
part surface, which is heated primarily by
radiation. Thus, as the hotter surface tries to ex-
pand, it will be restrained by the cooler steel,
leading to a hot upsetting condition and possibly
significant distortion even if quenched uni-
formly (Ref 21). A similar condition exists if the
tray of gears is placed near radiant tube heaters
or electric heating elements in the furnace wall
and the remainder of the gear surface is heated
by radiation from the roof of the furnace.
Localized overheating is particularly a
potential problem for inductively heated parts
(Ref 4, 26). Subsequent quenching of the part
leads to quench cracks at sharp corners and areas
with sudden changes in cross-sectional area
(stress raisers). Cracking is due to increases of
residual stresses at the stress raisers during the
quenching process. The solution to the problem
is to increase the heating speed by increasing the
power density of the inductor. The temperature
difference across the heated zone is decreased by
continuous heating or scanning of several pis-
tons together on a single bar (Ref 26).
For heat treating problems related to furnace
design and operation, it is usually suggested that
(Ref 19):
The vestibules of atmosphere-hardening
furnaces should be loaded and unloaded with
purging. Load transfer for belt and shaker
hearth furnaces should only occur with
thorough purging to minimize atmosphere
contamination.
If the load being heated in the furnace is
excessively large, either nonuniform heating
over the specified heating cycle or nonuni-
form cooling when quenched will result. In
such cases, either the production rate can be
increased or smaller loads should be pro-
cessed.
Retained Austenite. Dimensional changes
may occur slowly or quickly and are due to the
volume composition of the transformation pro-
ducts formed upon quenching. One of the most
important, with respect to residual-stress varia-
tion, distortion, and cracking, is the formation
and transformation of retained austenite. For
example, the data in Table 8 illustrate the slow
conversion of retained austenite to martensite,
which was still occurring days after the original
quenching process for the two steels shown (Ref
15, 16). This is particularly a problem when
dimensional control and stability is one of the
primary goals of heat treatment. Therefore,
Table 7 Minimum recommended material
removal from hot rolled steel products to prevent
surface seam and nonmetallic stringer problems
during heat treatment
Minimum material removal per side(a)
Condition Nonresulfurized Resulfurized
Turned on centers 3% of diameter 3.8% of diameter
Centerless turned or ground 2.6% 3.4%
(a) Based on bars purchased to special straightness, i.e., 3.3 mm in 0.04 m
(0.13 in. in 5 ft) maximum. Source: Ref 22
Steel Heat Treatment Failures due to Quenching / 269
Name ///sr-nova/Dclabs_wip/Failure_Analysis/5113_255-284.pdf/Chap_08/ 18/8/2008 3:30PM Plate # 0 pg 269