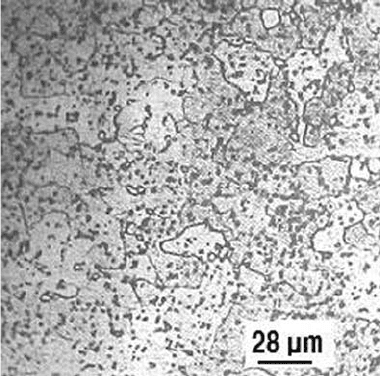
temperatures where silicon diffusion occurs,
thus slowing the process.
Silicon is a substitutional alloy element that
accumulates in the ferrous matrix adjacent to the
Fe
3
C carbide in the growth process. It increases
the carbon activity in this region, decreasing the
carbon flow to the growing particle and conse-
quently reducing its growth velocity (Ref 5, 16,
17). This silicon effect resulted in the develop-
ment of alloy 300M, which substitutes for 4340
steel in those applications where it is necessary
to use tempering temperatures that cause
embrittlement of tempered martensite, which is
soon defined. This reaction begins to occur at
temperatures on the order of 100
C. Cementite
can also be observed during quenching when the
M
s
temperature is elevated, as is the case of steel
with a low carbon content, mainly in the mar-
tensite formed just below the M
s
temperature.
This phenomenon is known as self-tempering
(Ref 5).
Stage 4. In carbon steels, stage 3 marks the
end of the tempering process. Spheroidization of
Fe
3
C occurs as cementite coalesces. This phe-
nomenon is sometimes called stage 4 of tem-
pering (Ref 2). The lath boundary maintains
stability up to approximately 600
C. Intense
rearrangement occurs between the lath and its
low-angle boundaries above 600
C. This
recovery process is replaced by recrystallization
and coarsening (Fig. 12) at temperatures be-
tween 600 and 700
C (Fig. 13).
Effect of Te mperature and Alloying. The
effect of the tempering temperature on steels
with increasing carbon contents can be inferred
from Fig. 13. During tempering, the continuous
decomposition of martensite to ferrite and car-
bides changes the state of stress because of
continuous dimensional changes. At low tem-
peratures (first stage), a volume contraction
takes place as a consequence of e-carbide pre-
cipitation. In the second stage, with the trans-
formation of retained austenite (approximately
300
C), the volume is increased. In stage 3, the
progressive decomposition of martensite leads
to a volume decrease.
It is important to observe that the austeniti-
zation temperature, which determines the
amount of carbon dissolved and the amount of
retained austenite, has a strong influence on the
expected volume changes (Ref 2, 4, 12, 13).
Table 3 shows the changes in length for various
steels as a function of tempering temperature.
Alloyed steels can also have another stage
with the precipitation of alloy carbides, includ-
ing M
2
C (molybdenum), M
7
C
3
,M
6
C, M
23
C
6
(chromium rich), V
4
C
3
, TiC, and so on, where
the “M” refers to a combination of metal atoms.
However, all of these carbides require long-
range diffusion of substitutional atoms. They
can only precipitate when the combination of
time and temperature is sufficient to allow this
diffusion. The alloy carbides grow at the
expense of the less stable cementite. If the con-
centration of strong carbide-forming elements,
such as molybdenum, chromium, titanium,
vanadium, and niobium, is large, then all of the
carbon can be accommodated in the alloy car-
bide, thereby completely eliminating the
cementite.
Figure 14 illustrates the effect of alloying
elements on hardness as a function of tempering
temperature in carbon steels (Ref 5). Increases in
hardness with additions of titanium, vanadium,
molybdenum, and chromium are related to the
alloy carbide precipitation. This phenomenon is
common for tool steels and can affect their
toughness, as illustrated in Fig. 15.
Embrittlement
Hardness decreases with increasing temper-
ing temperature (Fig. 10, 11). Consequently,
yield strength and tensile strength decrease as
well. On the other hand, elongation and ductility
increase. In this general context, a failure related
Fig. 12
Fe-0.17C alloy quenched in water from 900
C and
tempered at 650
C for 5 h. Microstructure shows
ferrite grains and spheroidized Fe
3
C
Steel Failures due to Tempering and Isothermal Heat Treatment / 293
Name ///sr-nova/Dclabs_wip/Failure_Analysis/5113_285-309.pdf/Chap_09/ 18/8/2008 3:34PM Plate # 0 pg 293