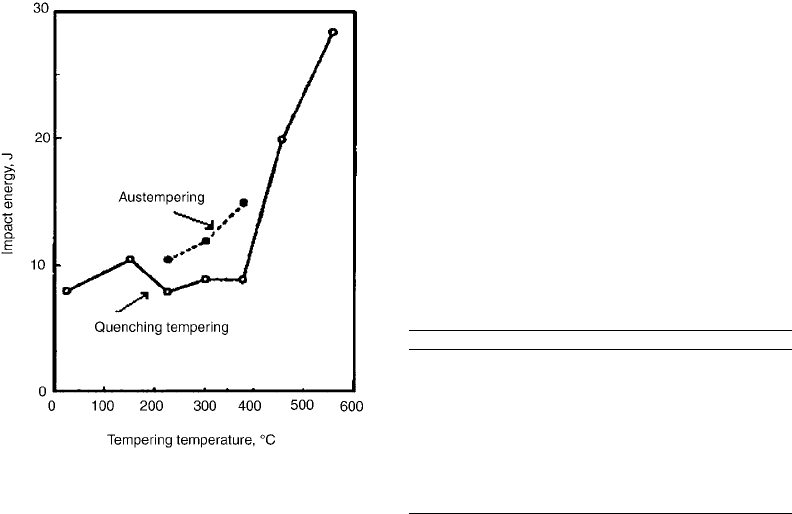
treatments were carried out. Experiment results
indicated that the acceleration of the crack
growth in hydrogen was more pronounced for
quenched and tempered conditions when the
tempered temperature range coincided with the
TME range of the 4140 steel (230 to 370
C).
At higher tempered temperature (approximately
550
C), the influence of hydrogen became
insignificant. Specimens in the austempered
condition have the best performance on the tests,
as seen in Fig. 23 (Ref 42).
The effect of the microstructure on HEM was
investigated for a low-carbon (Mn-Si-Cr) steel.
Microstructure formed by bainite and martensite
has better behavior than tempered martensite in
intermediate-temperature tempering. At the
same strength level, the impact energy of the
mixed microstructure is 17% higher than only
tempered martensite. It is attributed to the fact
that bainite-martensite delays the TME onset
(Ref 43).
Similar work was performed by Lantsman
et al. Experiments with cadmium-plated
65S2VA steel springs were carried out. In this
process, the steel absorbs hydrogen, which leads
to HEM. Results show that the susceptibility of
HEM has a strong dependence on the pre-
liminary heat treatment and structure. With an
identical hydrogen content, the austempered
steel, with lower internal stresses, will fracture
under a higher load than the steel subjected to
standard quenching and tempering (Ref 44).
Interaction of the TE Phenomenon with
Liquid-Metal Embrittlement. The presence of
select metallic specimens on the surface of
various alloys can provide for a very detrimental
reaction under load, known as liquid metal
embrittlement (LME), causing brittle fracture by
intergranular cracking. LME is the reduction in
elongation to failure that can occur when nor-
mally ductile metals are stressed while in contact
with liquid metals. Failure of components rela-
ted to LME is less common than failures caused
by other processes, such as fatigue, HEM and
stress-corrosion cracking, but a significant
number of industrial failures related to LME do
occur (Ref 45–47).
LME should depend on time of contact with
liquid metal while the solid is stressed. When
this occurs, the solid metal fails instantly,
because the flow of liquid metal into the crack tip
during crack growth plays a significant role (Ref
48). The liquid metal affects the fracture beha-
vior at the tip of the crack, reducing the critical
stress intensity for fracture and altering the
micromechanism of fracture at the crack tip
(Ref 49).
Sources of the aggressive elements vary,
including unintentional or accidental exposures,
for example, during fabrication or service when
there is intimate contact between the structural
and embrittling metals and also when there are
tensile stresses above a threshold value. Even-
tually, small amounts (0.1 g) of embrittling
metals can produce extensive cracking by LME
(Ref 45).
Plain carbon and low-alloy steels may be
embrittled by exposure to liquid lead, cadmium,
brass, aluminum bronze, copper, zinc, lead-tin
solders, and lithium (Ref 50, 51). Other metal
alloys also have susceptibility to LME. Table 6
lists embrittling environments for some com-
mon structural materials (Ref 45).
Fig. 23
Impact values of 4140 specimens after various
types of tempering treatments. Source: Adapted from
Ref 42
Table 6 Examples of embrittling metal
environments for some structural materials
Structural materials Embrittling environments
High-strength martensitic steel Hg, In, Sn, Pb, Cd, Zn, Li, Cu
Austenitic stainless steel Zn, Cu, Li
Titanium alloys Hg, Cd, Ag, Au
Aluminum alloys Hg, Ga, In, Sn, Pb, Cd, Zn, Na
Copper alloys Hg, Ga, Bi, Zn, Li, Sn, Pb, In
Zirconium alloys Hg, Cd, Cd-Cs, Zn
Nickel alloys Hg, In, Li, Zn, Ag
Magnesium alloys Na, K, Rb, Cs, Zn
Source: Ref 45
302 / Failure Analysis of Heat Treated Steel Components
Name ///sr-nova/Dclabs_wip/Failure_Analysis/5113_285-309.pdf/Chap_09/ 18/8/2008 3:35PM Plate # 0 pg 302