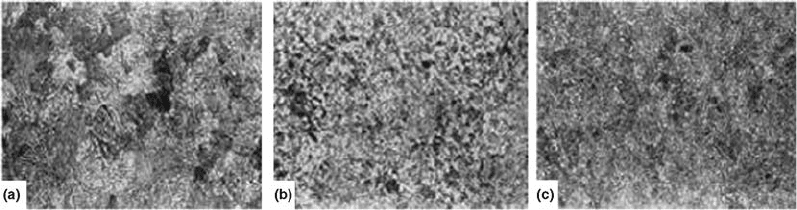
cementite formed in this manner will combine
with the required amount of ferrite to form
pearlite, and any remaining ferrite will be in the
structure as free ferrite (proeutectoid ferrite).
Pearlite will form if the carbon content in the
austenite is 40.83%, and excess carbon will
form cementite. Excess cementite (proeutectoid
cementite) will deposit in the grain boundaries.
Because cementite (Fe
3
C) contains a specific
amount of carbon and iron, pearlite also contains
a specific amount of cementite and ferrite.
As a phase in steel, the chemical composition
of cementite will contain carbides of other car-
bide-forming elements, such as chromium and
manganese Alloying elements of chromium,
manganese, nickel, and other elements are, of
course, commonly used in alloy steels for
property improvement. They also impact the
properties of ferrite and cementite, because they
partition differently in the phases. For example,
chromium and manganese partition in cementite
instead of ferrite. However, nickel and silicon
tend to favor partitioning in ferrite. Chromium,
manganese, molybdenum, and titanium are thus
cementite stabilizers in steels, while nickel and
silicon are ferrite stabilizers. Interestingly, while
chromium, manganese, molybdenum, and van-
adium show no negative effect on cementite
formation, titanium, nickel, and silicon exhibit a
negative effect on cementite formation (Ref
109).
Cementite develops different morphologies
and distributions depending on the process of
cementite formation. Figure 62 illustrates three
microstructural forms of cementite: lamellar,
mixed, and granular (Ref 110). Cementite may
also be classified as reticular, acicular, or gran-
ular (Ref 110). Reticular cementite, also known
as shell-type cementite, possesses a crack-
sensitive network or platelet structure. Acicular
cementite, or needlelike structure, refers to a
lamellar structure of cementite in ferrite, shown
in Fig. 62(b). Finally, cementite exhibits a
granular or grainy appearance, as shown in
Fig. 62(c).
Cementite forms during soldification from a
liquid or during solid-state transformations.
When cementite originates by crystallization
from a liquid melt, it is referred to as pri-
mary cementite (Fe
3
CI). Secondary cementite
(Fe
3
CII) is formed from austenite by hyper-
eutectoid alloys (carbon40.8%). Tertiary cem-
entite (Fe
3
CIII) is formed at temperatures below
723
C by precipitation in the grain boundaries
(which become richer in carbon with the
decreasing carbon content in a-iron).
Globular Carbides. Slowly heating a steel
to the carburizing temperature in the presence of
a carburizing atmosphere through the ferrite-to-
austenite temperature transformation region will
lead to unconnected globular carbide formation
either within the ferrite grains or at the former
ferrite grain boundaries, as shown in Fig. 63.
This process is favored by high carbon potentials
and also by reduction of normal heating rates
typically involved during carburizing, by
excessive furnace loading, or by a furnace mal-
function. Globular carbide formation may also
be enhanced by austenitic nuclei or by localized
concentrations of carbide-forming elements.
The problem of globular carbides may also
coexist with other problems, such as retaining
austenite or quench cracking.
When carburizing steels (0.15 to 0.25% C),
which are commonly ferritic with localized
areas of spheroidal carbides due to prior nor-
malizing and subcritical annealing, are heated
through the Ac
1
temperature, the high-carbon
regions begin to transform to austenite, resulting
in the formation of localized regions of carbon
and carbide-forming elements in addition to
undissolved carbides in the presence of the
Fig. 62 Cementite structures of CT60 steel with (a) lamellar, (b) mixed, and (c) granular cementite. Original magnification: 500·
Sources of Failures in Carburized and Carbonitrided Components / 223
Name ///sr-nova/Dclabs_wip/Failure_Analysis/5113_177-240.pdf/Chap_06/ 18/8/2008 3:21PM Plate # 0 pg 223