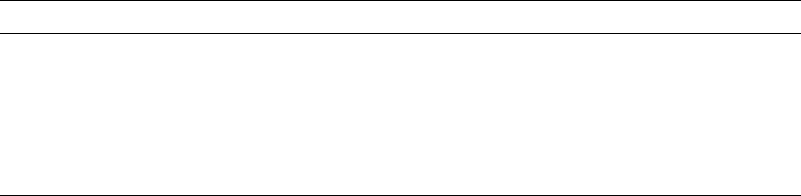
gas-carburized steel (Ref 10). Structural surface
anomalies act as preferential zones for fatigue
crack initiation under low stress amplitudes.
Shear-type crack growth can occur in ductile
retained austenite in the near-surface region of
the case for gas-carburized steels. Kikuchi et al.
have shown that shot peening is very effective in
improving the fatigue properties of carburized
steels with these surface structure anomalies
(Ref 59, 65). In fact, in their study, the fatigue
properties were essentially comparable for a
20 mm diameter chromium-molybdenum steel
(0.16% C, 0.26% Si, 0.74% Mn, 0.012% P,
0.013% S, 1.01% Cr, 0.18% Mo) bar that was
carburized at 950
C for 1 h with and without
surface structure anomalies (to a depth of ap-
proximately 30 mm) after shot peening. As a
result of this work, it was concluded that since
internal oxides near the surface can also act as
preferential crack initiator sites, it is desirable to
avoid the presence of such defects during gas
carburizing (Ref 65).
Although components such as gears are car-
burized and shot peened to introduce the desired
level of surface compressive stresses, there are
other processes that can be used to introduce
compressive stresses. One such process is pre-
setting. Presetting involves the introduction of
an overload that causes yielding in the area of
maximum stress concentration, such as in the
root area of a gear tooth. When the load is
released, a residual stress is introduced in that
area. The induced stress is compressive on the
side being loaded and tensile on the other side
(Ref 66). Woods et al. evaluated presetting to
improve the bending fatigue of carburized AISI
4120 steel spur gear teeth and found that pre-
setting introduces compressive stresses in
the area of a gear tooth where fatigue cracks
originate. The results of this work showed
that presetting provided substantially longer
fatigue life.
Dimensional Stability
Dimensional stability has two components:
size (distortion) and shape (warpage). Distortion
is defined as “an irreversible change in the
component during heat treatment” (Ref 67).
While changes in shape such as straightness
(warpage) can be corrected by application of
stress or by tempering in the elastic range
(reversible), size changes are irreversible and
cannot be changed in this way. Metallurgically,
distortion may be thermally or transformation-
ally derived. Size distortion typically refers to
dimensional variation due to growth or shrink-
age that is due to volumetric changes attributable
to microstructural phase transformations (Ref
19, 68). Figure 28 shows the effect of the tem-
perature dependence of the specific phase
volume of different steel transformation phases
(Ref 69).
Variables that affect distortion include (Ref
19, 68, 70):
Chemical composition and hardenability—
chemical and phase composition as well as
hardenability (distortion increases as hard-
enability increases), as shown in Fig. 29
(Ref 67, 71, 72)
Steelmaking—grain size and hardenability
Hot working—hot reduction, length and
direction of fiber
Prior heat treatment—residual stresses,
grain size and uniformity of microstructure
Geometry—cheese blanks, shafts, rims
Heat treatment aspects—heat rate, cooling
rate (quench severity), quenching tempera-
ture, jigs and fixtures, plug quenching. Plug
quenching is used to minimize dimensional
change of inside diameters such as round-
ness and taper distortion of ring-shaped
components (Ref 67, 68) (generally, salt
bath quenching yields minimum distortion
Table 10 Effect of shot peening on retained austenite transformation and residual stress of
gas-carburized 18NCD6 steel
Shot peening(a)
Heat
treatment(b)
Depth modified by
shot peening treatment, mm
Retained austenite
on surface, %
Retained austenite
converted to martensite, % s
max
, MPa
None T1 ... 24.7 ... 300
T2 ... 36.8 ... 300
G1 T1 100 5.7 19.0 1450
T2 100 14.9 21.9 1350
G2 T1 200 12.1 12.6 980
T2 200 22.1 14.6 930
(a) G1, steel shot, BA 300, F 25–30A, overlap rate 150%; G2, steel shot, BA 800, F 55–80A, overlap rate 150%. (b) T1, carburize for 3 h. at 920
C, plateau at 850
C,
oil quenching at 60
C, tempering for 2 h. at 150
C; T2, carburize for 3 h at 960
C, oil quenching at 60
C, tempering for 2 h at 150
C
200 / Failure Analysis of Heat Treated Steel Components
Name ///sr-nova/Dclabs_wip/Failure_Analysis/5113_177-240.pdf/Chap_06/ 18/8/2008 3:19PM Plate # 0 pg 200