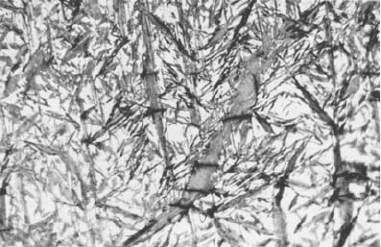
McEvily et al., reported the use of fracto-
graphic analysis to explain cracking of a
carburized AISI 9310 gear at the case-core
transition zone. One of the factors was the dif-
ferential in the Poisson ratio (n) between the case
and the core that develops during a monotonic
bending test when the core deforms plastically
while the case deforms elastically. McEvily
used as an example to illustrate this point a
9 mm diameter round bar with a 1 mm case.
When the bar is first loaded initially and the
deformation is elastic, the Poisson ratio for the
case and the core is equal. Upon further bending,
the core will deform plastically while the case is
deforming elastically. However, because of the
difference in the Poisson ratio between the case
(n = 0.3) and the core (n = 0.5) at this point,
radial tensile stresses will develop. For a tensile
strain of 1%, the radial strain in the case (relative
to the centerline) would be 0.003, and the radial
strain in the core would be 0.005. To remain
compatible, the difference in the strain and
corresponding displacements must be accom-
modated by the formation of a tensile stress.
However, this radial stress will result in a state of
triaxial stress that will promote brittle behavior
by inhibiting plastic deformation. The total
tensile stress may then be developed sufficient
to result in rupture at the case-core interface
(Ref 82).
Grinding Cracks. Grinding may be used for
postprocessing of components to remove growth
and distortion that may have resulted from car-
burizing and carbonitriding. Grinding is also
performed to remove such metallurgical features
as carbide films, internal oxidation, and high-
temperature transformation products that may
impart deleterious performance properties. In
addition, grinding processes are commonly used
to create the desired surface finish to improve
bending and contact fatigue and lubrication
properties.
Surface cracks in the carburized case may
occur during the grinding process, which can be
attributed to microstructural transformations
and thermal stresses producing tensile forces. If
the tensile forces in the case exceed the material
strength, then surface cracks will result. This is
due to the difference in the specific volume of
the transformational phases present in the case
structure, primarily martensite and austenite.
Structural defects, such as those caused by
inclusions, will also influence the susceptibility
of the steel to cracking.
Generally, crack creation during grinding is
influenced by thermoelastic tensile stresses that
are created in the surface cooling zone during
grinding. They are dependent on thermal and
mechanical properties of the material, maximum
contact temperature, grinding feed depth, and
cooling rate.
One study conducted on the generation of
grinding cracks showed that microstructural
heterogeneity, such as the presence of carbide
inclusions (particularly those with a mean dia-
meter of 6 to 10 mm), which were shown to be
associated with large internal residual stresses,
were a predominant cause of grinding cracks
(Ref 83).
Grinding burns arise when excessive heat is
generated during the grinding process, and this is
characterized by surface discoloration. The term
grinding burn refers to localized surface tem-
perature increases at least sufficient to cause
tempering of the martensitic surface, resulting in
localized soft spots. Furthermore, since carbide
precipitation volume contraction accompanies
tempering, the burnt areas are in tension and, if
the resulting tensile stresses are sufficient, sub-
ject to tranverse cracking. However, in other
cases, the increase may be in excess of the Ac
3
temperature, producing an austenitic surface
that, upon rapid cooling, may produce a hard,
light-etching, martensitic thin layer at the sur-
face. This induced defect is known as a rehar-
dening burn, which is characteristically
surrounded by a layer of tempered steel (Fig. 36)
(Ref 84). In this case, the rehardened zone is in
compression due to the martensitic volume
expansion, and the surrounding areas of tem-
pered martensite are in relative tension. Crack-
ing may occur in the area surrounding the
rehardened material or in the interface between
the two (Ref 84).
Fig. 35
Microcracks in the martensitic case of a coarse-
grained SAE 8620 steel
Sources of Failures in Carburized and Carbonitrided Components / 207
Name ///sr-nova/Dclabs_wip/Failure_Analysis/5113_177-240.pdf/Chap_06/ 18/8/2008 3:19PM Plate # 0 pg 207