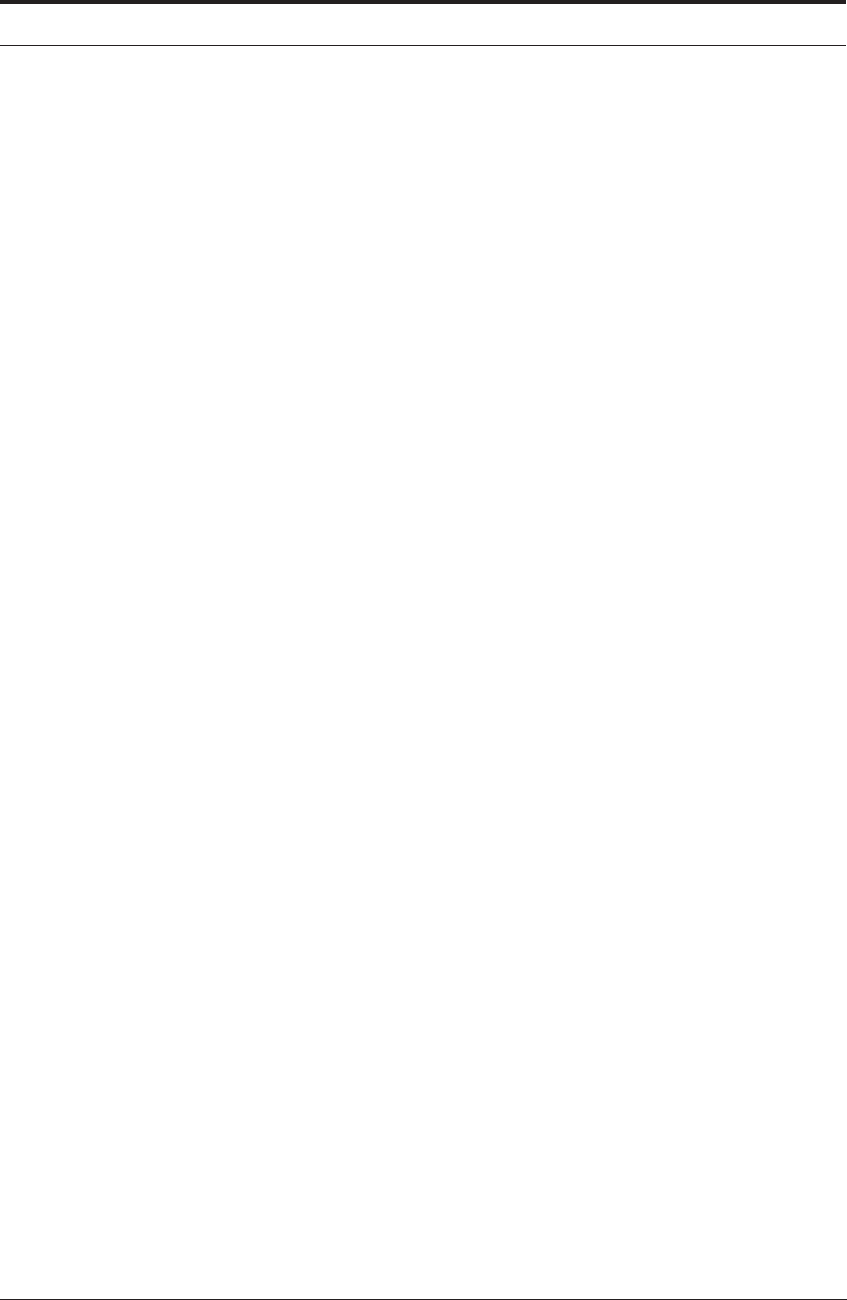
314 COOLANTS AND LUBRICANTS
automatic lathes where several tools are used simultaneously or in quick succession to fabricate
relatively small components.
In Chapter 5 the two main sources of heat in a cutting operation are discussed - i) on the pri-
mary shear plane and ii) at the tool-work interface (especially in the flow-zone on the tool rake
face). The work done in shearing the work material in these two regions is converted into heat,
while the work done by sliding friction makes a minor contribution to the heating under most
cutting conditions.
Coolants cannot prevent the heat being generated, and do not have direct access to the zones
which are the heat sources. Heat generated in the primary shear zone is mostly carried away in
the chip and a minor proportion is conducted into the workpiece. Water-based coolants act effi-
ciently to reduce the temperature both of the work-piece and of the chip after it has left the tool.
The cooling of the chip is of minor importance, but maintaining low temperatures in the work-
piece is essential for dimensional accuracy.
The removal of heat generated in the primary shear zone can have little effect on the life or
performance of the cutting tools. By contrast, as has been demonstrated, the heat generated at
and near the tool/work interface is of much greater significance, particularly under high cutting
speed conditions where the heat source is a thin flow-zone seized to the tool.
The coolant cannot act directly on the thin zone which is the heat source. However, the coolant
can remove heat from those surfaces of the chip, the workpiece, and the tool which are accessi-
ble to the coolant. Removal of heat by conduction through the chip and through the body of the
workpiece is likely to have relatively little effect on the temperature at the tool/work interface.
This is because both chip and workpiece are constantly moving away from the contact area,
allowing very little time for heat to be conducted from the source. For example, when cutting at
30 m min
-1
(100 ft/min) the time required for the chip to pass over the region of contact with the
tool is of the order of 0.005 seconds. The tool is the only stationary part of the system. It is the
tool which is damaged by the high temperatures and, therefore, in most cases, cooling is most
effective through the tool.
10.2.1 Importance of fluid jet and nozzle location
The tool is cooled most efficiently by directing the coolant towards those accessible surfaces of
the tool which are at the highest temperatures. These are surfaces from which heat is most rap-
idly removed, and the parts of the tool most likely to suffer damage. Knowledge of temperature
distribution in the tool can, therefore, be of assistance in a rational approach to coolant applica-
tion. This is illustrated by experimental evidence from the authors’ laboratory cutting tests on
tools used to cut a very low carbon steel and commercially pure nickel.
4,5
With steel, nickel and titanium alloys, the tool life is extended in turning if the coolant jet can
gain good access to the clearance faces of the tool. Also, Chapter 9 showed that when machining
commercially pure nickel the hottest region is very close to the cutting edge.
In most cases it is desirable to direct the jet at the flank face. This can be most easily done in
turning operations. In some of the authors’ experiments, the tool was held upside down in a tool-
post at the back of the lathe. The chip was formed on the rake surface and fell directly down into
the bed. This arrangement allowed the cutting fluid to pour directly down into the flank face
region and provide consistent cooling action to the face and edge.
5
In other experiments, espe-