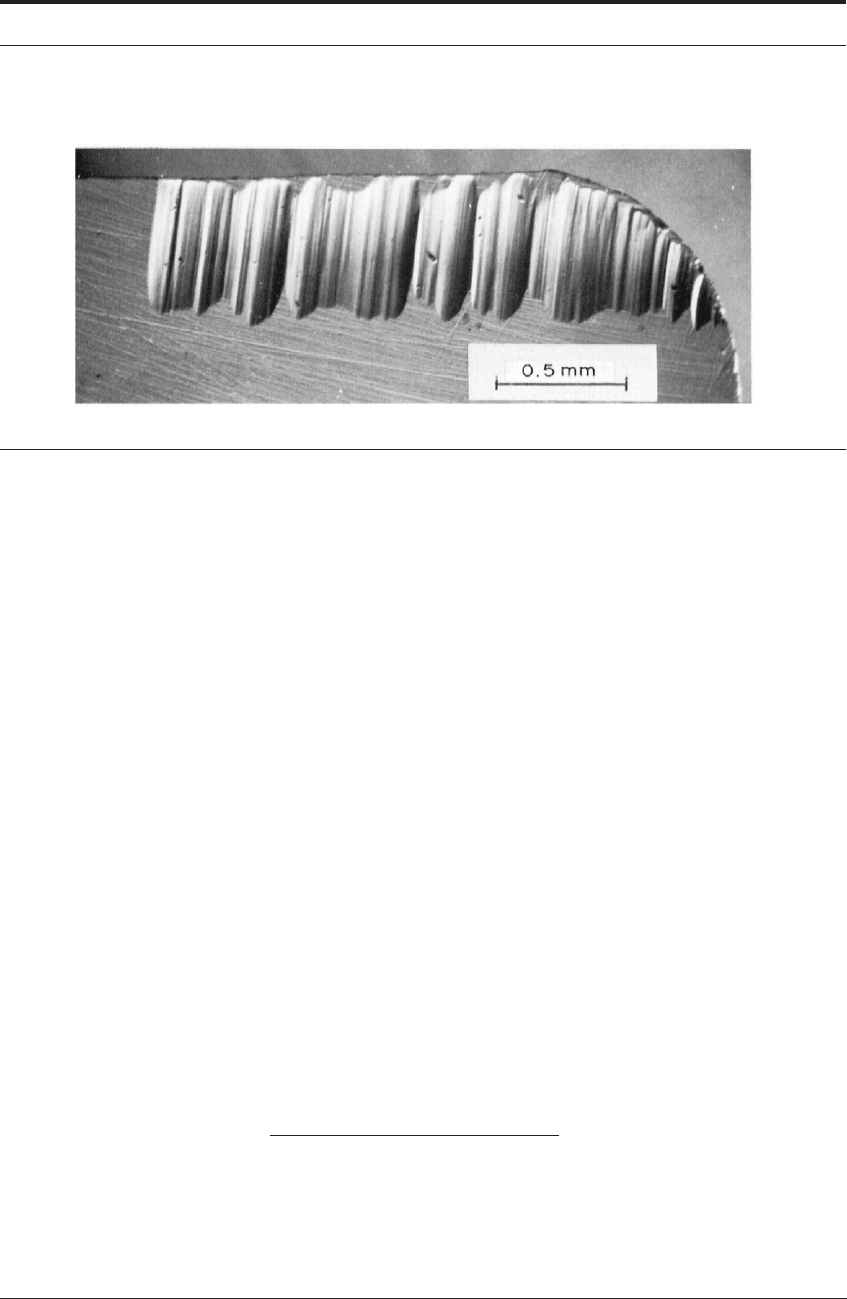
286 MACHINABILITY
FIGURE 9.28 Deep grooves in rake face of WC-Co tool after cutting high-sulfur leaded steel at 46 m min
-1
for 10 min (After Milovic
19
)
At high cutting speed, sections through quick-stops often show a modest secondary shear
zone. Flow is retarded at the under surface of the forming chip, but without a definite flow-zone.
The tool rake face temperatures are often considerably lower than when cutting the correspond-
ing lead-free steels. These observations suggest that, under some cutting conditions, lead at the
interface prevents complete seizure between the steel work-material and the tool. This effect
depends on the tool material.
The reduction of seizure, allowing sliding at the interface, may in fact cause an acceleration of
wear despite the lower interface temperatures. With high speed steel tools, or WC-Co tools, the
rake face of the tool may be rapidly worn when cutting leaded steel. Deep, “horseshoe-shaped”,
localized craters are often observed on high speed steel tools.
24
They start very close to the tool
edge. These may be accompanied by localized flank wear. The horseshoe configuration is not
observed with carbide tools. However, craters starting at or near the edge may develop rapidly in
WC-Co tools (Figure 9.28).
19
This rapid damage to the tool is most common at low or medium
cutting speed. It may disappear if the speed is raised. Some CVD coated tools appear to be very
resistant to this form of wear.
In summary, the particles of lead in steel are plastically deformed during machining. This is
seen clearly where it is associated with MnS inclusions. The action of lead as a free-cutting addi-
tive is very complex.
†
Because it is complex, the value of “free cutting” steels as a solution to
particular production problems must be investigated for each case.
†. Today’s demands of “dry cutting” - see end of Chapter 10 - are connected to the effects described in the last few
pages. The results from the authors’ laboratory experiments show a surprising range of possible “internal lubrication”
effects from the various “free cutting” additions. The variations between the “straight” and “steel-cutting” grades of
carbides are perhaps the most surprising of all, even to many practitioners - here the “machinability” of the “free cut-
ting” steels is totally changed by the bonding effects in the secondary shear zone. Dry cutting will therefore be very
easy with the “steel-cutting” grades and less so with the “straight, WC-Co” grades.