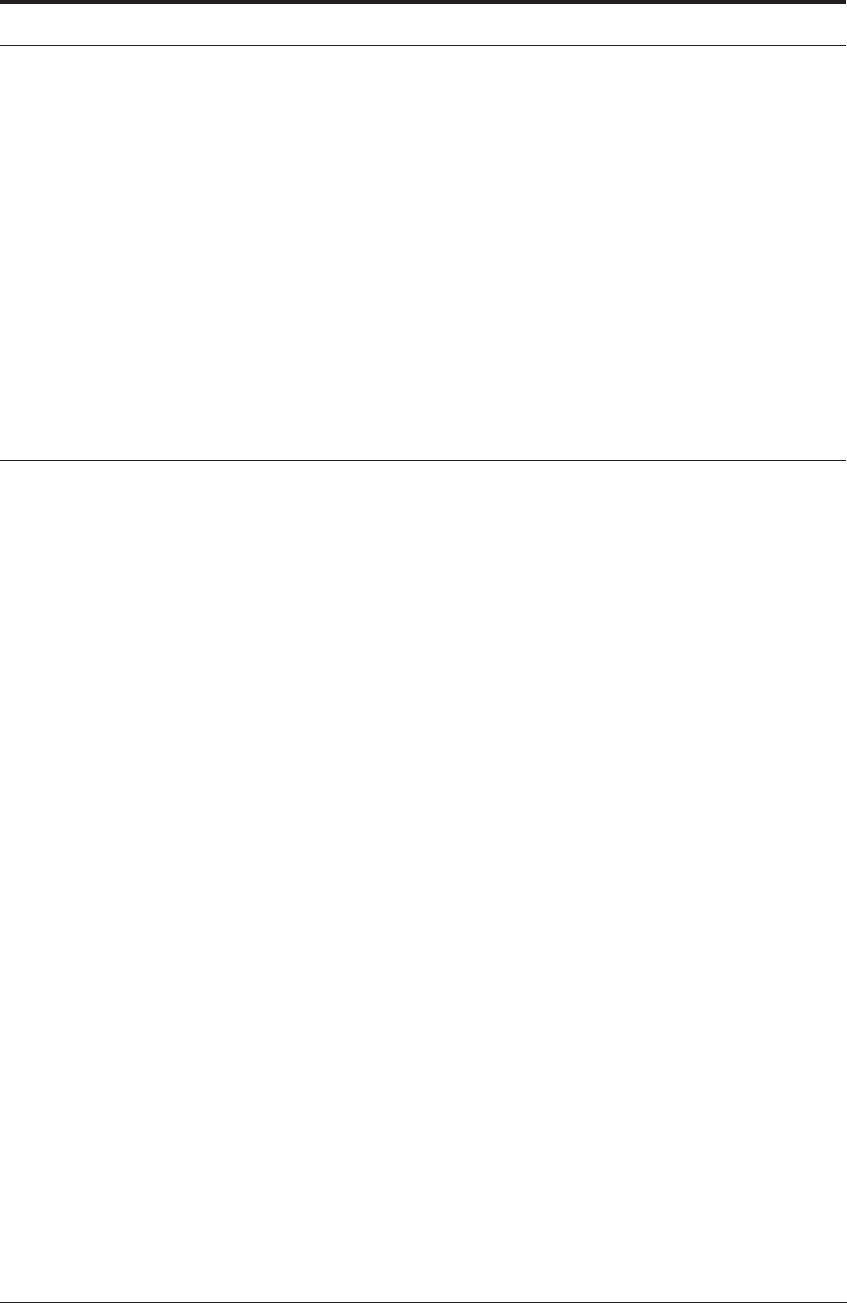
CAST IRON 293
9.8.1 Free cutting stainless steels
Free-cutting austenitic stainless steels increase tool life and metal removal rates. These have
high sulfur contents. As with the free-cutting ferritic steels, their improved machinability is asso-
ciated with the plastic behavior of the sulfides in the flow zone.
The use of free-cutting stainless steels is restricted, because the introduction of large numbers
of sulfide inclusions reduces corrosion resistance under some conditions. An alternative free-
cutting additive is selenium, which forms selenide particles which behave like sulphides during
machining. Selenides are less harmful to corrosion resistance. Improved machinability also
occurs when using calcium deoxidation to produce protective layers at the tool/work interface.
Importantly, these may well improve machinability without loss of corrosion resistance.
32
9.9 CAST IRON
Flake graphite cast irons are considered to have very good machining qualities. In fact, a major
reason for the continued large-scale use of cast iron in engineering is not only the low cost of the
material and the casting process, but also the economics of machining the finished component.
By nearly all criteria cast iron has good machinability: low rates of tool wear, high rates of
metal removal, relatively low tool forces and low power consumption. The surface of the
machined cast iron is rather matt in character, but ideal for many sliding interfaces. The chips are
produced as very small fragments which can readily be cleared from the cutting area even when
machining at very high speeds. It is a somewhat dirty and dusty operation, throwing a fine spray
of graphite into the air, so that protection for factory personnel may be required.
As when cutting other materials, there is a great difference between the behavior of cast iron
when sheared i) on the shear plane and ii) at the tool work interface. The most important charac-
teristic is that fracture on the shear plane occurs at very frequent intervals, initiated by the graph-
ite flakes. The chip is thus composed of very small fragments a few millimeters in length.
Because the chips are not continuous, the length of contact on the rake face is very short. The
chips are thin and the cutting force and power consumption are low. The cutting force is low also
because graphite flakes are very weak. One flake may extend an appreciable way across the
shear plane.
Table 9.3 shows values for the cutting force (F
c
) for a typical pearlitic cast iron in comparison
with steels. This aspect of machinability is influenced by the grade and composition of the cast
iron. Low strength cast irons, the structure of which consists mainly of ferrite and graphite, are
the most machinable, permitting the highest rates of metal removal. Permissible speeds and
feeds are somewhat lower for pearlitic irons, and decrease as the strength and hardness are
raised. As with steel, there are extensive published data for cutting speeds when machining gray
cast iron with high speed steel and cemented carbide (WC- Co) tools.
33,36
Recently, there is
much data for ceramic tools.
37
Table 9.4 shows typical recommendations for turning gray cast
irons. These are classified according to hardness, when using the three classes of tool material.
The use of ceramic (alumina and sialon) tools for machining cast iron has increased greatly in
recent years, mainly in mass production turning, boring and milling operations. Most cast iron
brake drums, clutch faces and flywheels are, today, being machined with ceramic tools. The
excellent surface finish achieved often eliminates the need for a grinding operation. Because the
chips are fragmented, very high cutting speeds can be used without problems of chip control.