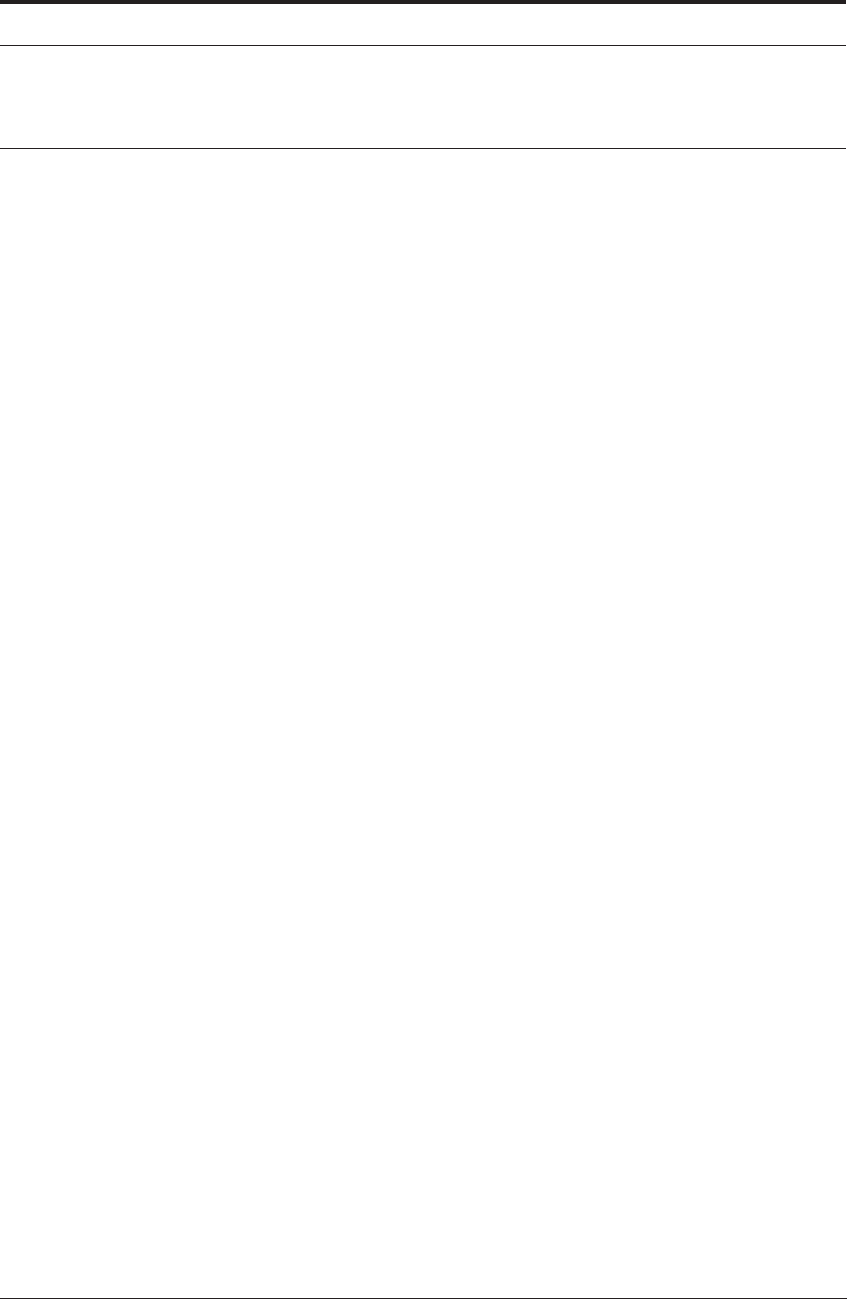
254 MACHINABILITY
9.3 ALUMINUM AND ALUMINUM ALLOYS
9.3.1 Introduction
Alloys of aluminum in general also rate highly in the machinability table by most of the crite-
ria. As with magnesium, the melting points of aluminum (659°C) and its alloys are low. Conse-
quently, the temperatures generated during cutting are never high enough to be damaging to the
heat-treated structures of high speed steel tools. Good tool life can be attained up to speeds of
600 m min
-1
(2,000 ft/min) when using carbide tools, and 300 m min
-1
(1,000 ft/min) with tools
of high speed steel. Speeds as high as 4,500 m min
-1
(15,000 ft/min) have been used for special
purposes. (Further discussion of high speed, and very high speed machining of aluminum alloys
appears in Chapter 11.) Wear on the tool takes the form of flank wear, but no detailed study of
the wear mechanism has been reported.
9.3.2 Machinability of aluminum-silicon alloys
High tool wear rates become a serious problem with only a few aluminum alloys. In alumi-
num-silicon castings containing 17-23% Si, the silicon content is above the eutectic composi-
tion. The structures thus contain large grains of silicon, up to 70 μm across. In addition, they
contain a finely dispersed silicon of the eutectic structure. The large silicon crystals greatly
increase the wear rate, even when using carbide tools.
2
The eutectic alloys, containing 11-14%
Si can be machined at 300-450 m min
-1
(1,000-1,500 ft/min) with good carbide tool life, but the
presence of large silicon grains may reduce the permissible speed to only 100 m min
-1
(300 ft/
min). The drastic effect of large silicon particles is the result of the high stress and temperature
which these impose on the cutting edge. Silicon particles have a high melting point (1,420°C)
and high hardness (> 400 HV). Figure 9.2 shows a section through the worn cutting edge of a
carbide tool after cutting a 19% Si alloy.
3
The layer of silicon (dark gray) attached to the worn
surface demonstrates the action of the large silicon crystals which cause an attrition type of wear.
The photomicrographs demonstrate that the wear of tools depends not only on the phases
present in the work material, but also on their size and distribution. Small silicon particles in the
eutectic bypass the cutting edge. Either they do not make contact with the tool at all, or they
make only rubbing contact with one of the flat surfaces. However, the large primary silicon
grains cannot pass by the cutting edge but are divided when they make contact with it. Part of the
silicon passes away with the chip and part continues on the new machined surface. At the same
time, a layer of sheared silicon is strongly bonded to the tool surface, causing rapid attrition
wear. The machining of hypereutectic Al-Si alloys is one of the most important applications for
polycrystalline diamond tools. Most engine manufacturers now use these tools for machining
pistons and other components, cast from high silicon alloys. Turning, boring and milling opera-
tions are carried out at much higher speed with longer tool life and improved surface finish. Pis-
tons have been turned at speeds from 300 to 1,000 m min
-1
(1,000 to 3,000 ft/min), and at a feed
of 0.125 mm/rev (0.005 in/rev) with tool edge life of the order of 100,000 components. The dia-
mond tools have proved so advantageous for cutting the hypereutectic alloys that they are used
for turning and milling other aluminum alloys even where carbide tools give reasonable tool life.
Polycrystalline diamond tools can be kept in use for months. This gives economies in spite of the
higher tool cost.