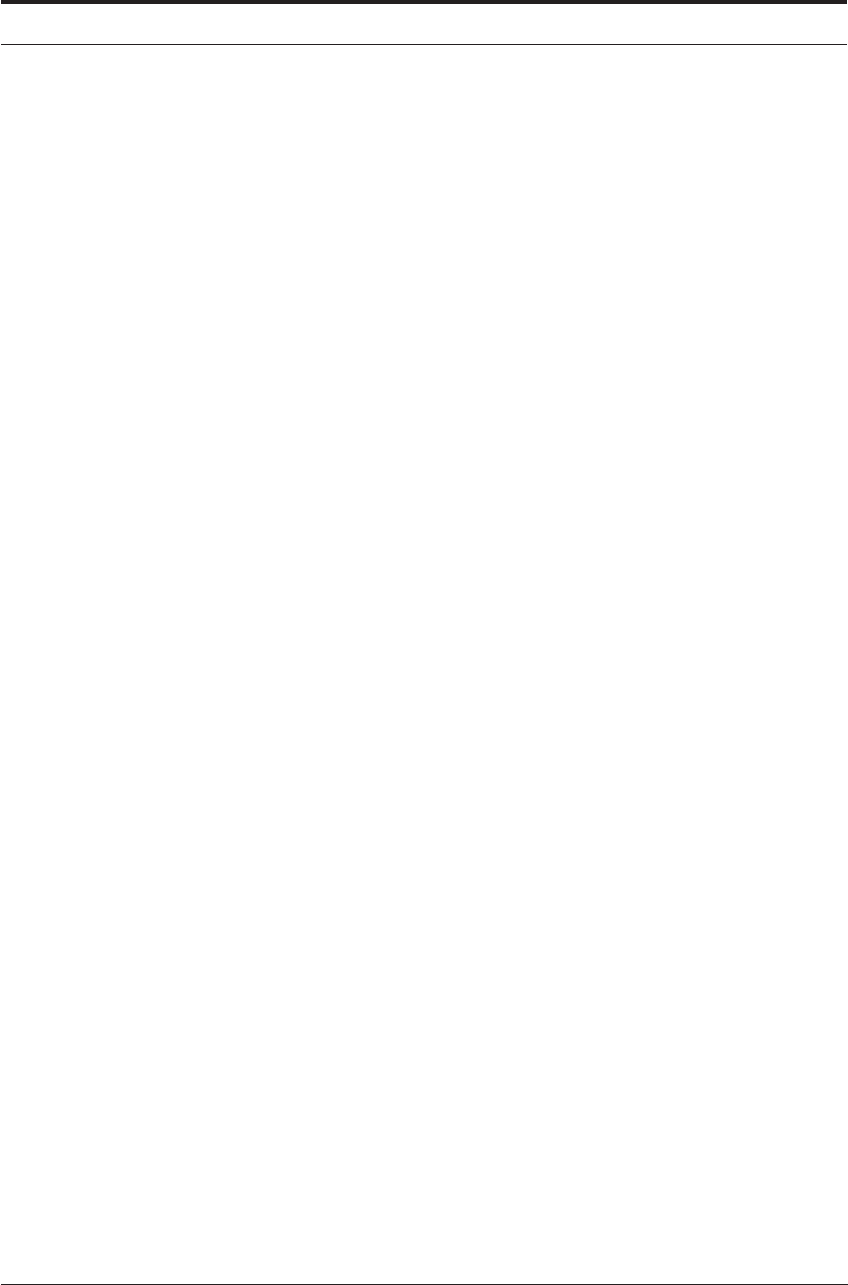
SIALON 235
As with alumina ceramics, sialon tools are normally used with negative rake and often with
similar chamfers at the edge (Figure 8.2). Industrial usage has been largely in machining ferrous
materials. Successful use has been reported on roughing cuts and in operations involving rough
surfaces and interruptions such as holes. Gray cast iron can be machined at 600 m min
-1
(2000
ft/min) with a feed of 0.25 m/rev. Milling cutters tipped with sialon inserts are being used for
cutting cast iron. Steel hardened to 550 HV has been successfully cut at speeds of up to 60 m
min
-1
(200 ft/min) with a feed rate of 0.12 mm/rev.
8.4.1 A special note on machining aerospace nickel alloys with sialon tools
In the machining of aerospace alloys, nickel-based gas turbine discs are being faced using sia-
lon tips at 180 to 300 m min
-1
(600-1000 ft/min) at a feed of 0.2 mm/rev, whereas carbide tools
can be used at only 60 m min
-1
(200 ft/min). Use in this application is significant for the confi-
dence placed in the reliability of the tool, since tool failure could result in scrapping of very
costly components
Both crater and flank wear are observed on sialon tools. In one research program on cutting of
a nickel-based alloy, the limit to rate of metal removal was reached when the tool edge deformed
and fractured. Wear by attrition at low speed, and by diffusion and interaction with the Si
3
N
4
phase at high speed, were observed, and also a type of notch wear, where the outer edge of the
chip crossed the tool edge.
6
(The high resistance to interaction with nickel at high temperatures
is shown by the very low rate of attack when immersed in molten nickel.) The interactions when
machining this alloy, although they were a cause of wear, did not prevent sialon being the best
material for machining nickel alloys on an industrial scale, at speeds three or four times higher
than with carbide tools.
In the case of machining another nickel-based high temperature alloy, industrial experience
demonstrated that, for this alloy, long tool life can be achieved using the A1
2
0
3
/SiC whisker
ceramics.
16
When machining engineering steels, however, sialons are generally not used on a
industrial scale because of rapid wear, attributed to interaction between tool and work materials.
The conditions at the tool edge when cutting different alloys are so complex that more research
will be required to achieve an understanding of the performance of different ceramic tool materi-
als. At this stage optimum ceramic tooling is selected by empirical testing.
8.4.2 Summary of ceramics, alumina-based composites and sialon
The advances in alloying of ceramic tools today, typified by sialons, A1
2
O
3
/ZrO
2
, and A1
2
O
3
/
SiC whiskers, demonstrate that numerous variations in composition, and even heat treatment,
can be introduced to modify structure and properties for specific cutting operations on different
work materials. A universal ceramic tool to meet all requirements is unlikely and in the next
period, various ceramic types will be competing for use in particular niches. Improvements in
rigidity of machine tools and in tool design can be expected to enable ceramic tools to be used in
more operations. It is of interest that, in Japan, the ceramic share of indexable inserts is esti-
mated at 8 to 10%, while in the U.S. the proportion is estimated to be lower at about 3 to 4%.
17