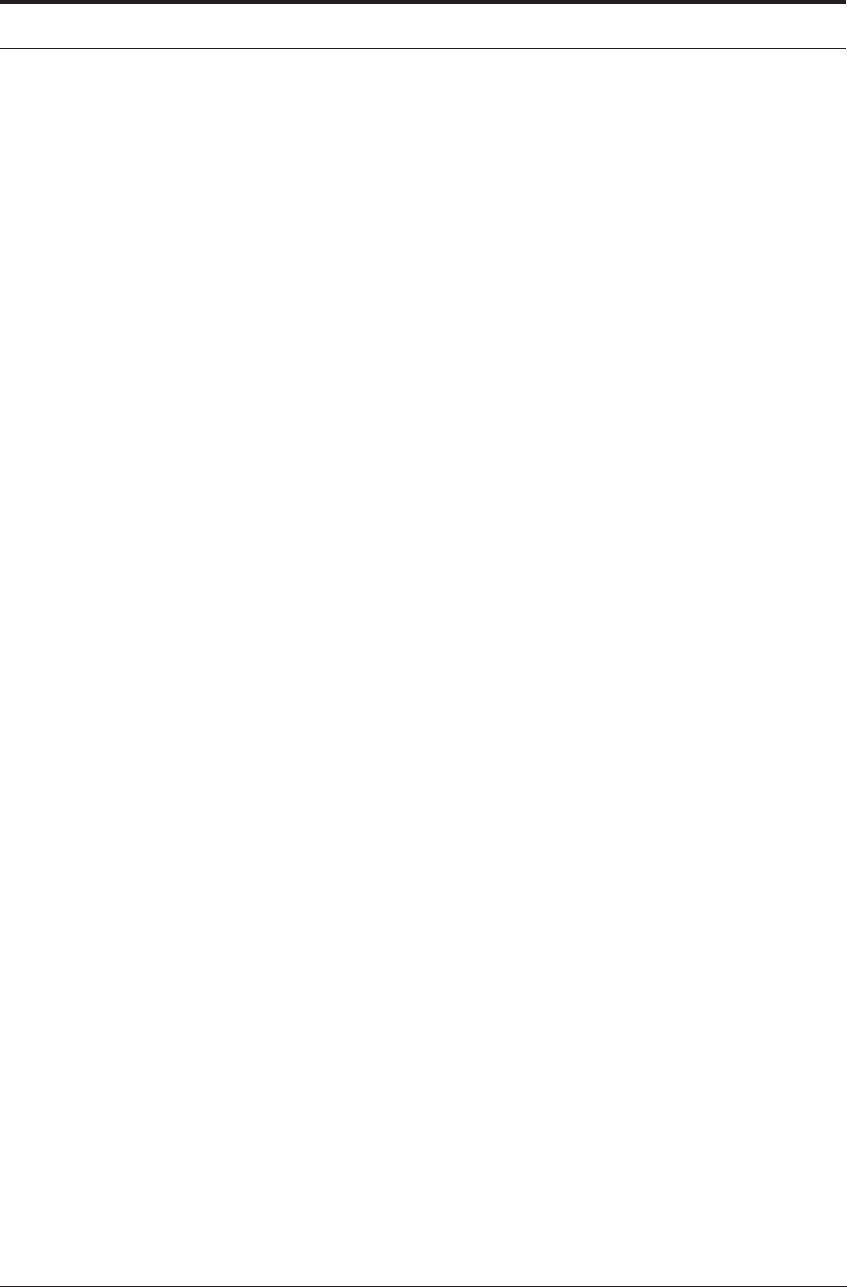
214 CUTTING TOOL MATERIALS II: CEMENTED CARBIDES
7.9.4 Comparisons between different types of coating
There are differences between the different coatings in respect of their resistance to flank and
crater wear. Most reported results on steel cutting suggest that TiN is more resistant than TiC to
crater wear and that TiC is more resistant to flank wear. The crater and flank wear rates of alu-
mina-coated tools appear to be not greatly different from those of carbide and nitride coated
tools. There is evidence that the crater wear of alumina coatings is caused by superficial plastic
deformation, rather than by a diffusion mechanism.
15
The greatest difference in wear rate is
reported to be that in the notch at the outer edge of the chip (Figures 6.23 and 6.24) where slid-
ing rather than seizure occurs. Wear at this position was minimal with alumina coatings. TiN
coatings were nearly as good as alumina, but notch wear on TiC coatings was very much greater
and not greatly different from that on uncoated tools.
7.9.5 Multiple layer and nanolayer coatings: a design goal
It is clear that there is a place for more than one type of coating, and therefore multi-layer
coatings may provide a type of tool which will cope well with a variety of operations. Colloqui-
ally speaking, could research work discover a tooling combination that would “give the best of
all worlds”? It might consist of a tough carbide core - probably one of the WC-Co, “K-grades” -
coated with several layers: one that would bond reliably to the core; another that would buffer
thermal-expansion discrepancies; another that would provide insulation; another that would
buffer diffusion wear; another on the very outside that would have ultra-low friction characteris-
tics.
Will such an “all-purpose”, multi-layer “sandwich” eventually be discovered over the next
few years? This is the new challenge to cutting tool developers. Some progress is reviewed in
the next two sections.
7.9.6 Multiple layer coatings
For such multiple-layer “sandwiches” the first layer is usually TiN or TiCN created by the
PVD process. These can be created on straight WC-Co substrates, or on mixed carbide sub-
strates of varying cobalt content. TiN or TiCN minimize or eliminate the formation of -phase
(Co
x
W
y
C
z
) at the interface with the substrate. It is also common to create the last, or outer, layer
of the “sandwich” with TiN using PVD. This induces beneficial residual compressive stresses on
the complete structure.
In today’s industrial inserts of this type, multiple layers of only TiN may in fact be successful.
Multiple layering allows the final thickness of the “sandwich” to be as much as 10-15 m. This
is greater than can be achieved by trying to create the whole layer in one operation. When used
in turning and milling operations, the successive layers of very thin coats, rather than one heavy
coat, give a more stable structure. In other, triple-layer “sandwiches” the middle layer is often
TiCN as shown earlier in Figure 7.33.
Beyond this, Komanduri
32
reports that many “sandwich” combinations are being investigated
today including the following: {TiN-Al
2
0
3
-TiC-TiCN}, or {TiN-TiCN-TiC}, or {TiN-A1
2
0
3
-
TiCN}, or {A1
2
0
3
-TiC}, or {A1
2
0
3
-TiC-TiCN}, or {TiN-A1
2
0
3
-TiC}, or {TiN-A1
2
0
3
-TiN-
A1
2
0
3
-TiN-A1
2
0
3
-TiCN}. In addition, Komanduri reports that one grade of TiN-A1
2
0
3
on a
η
μ