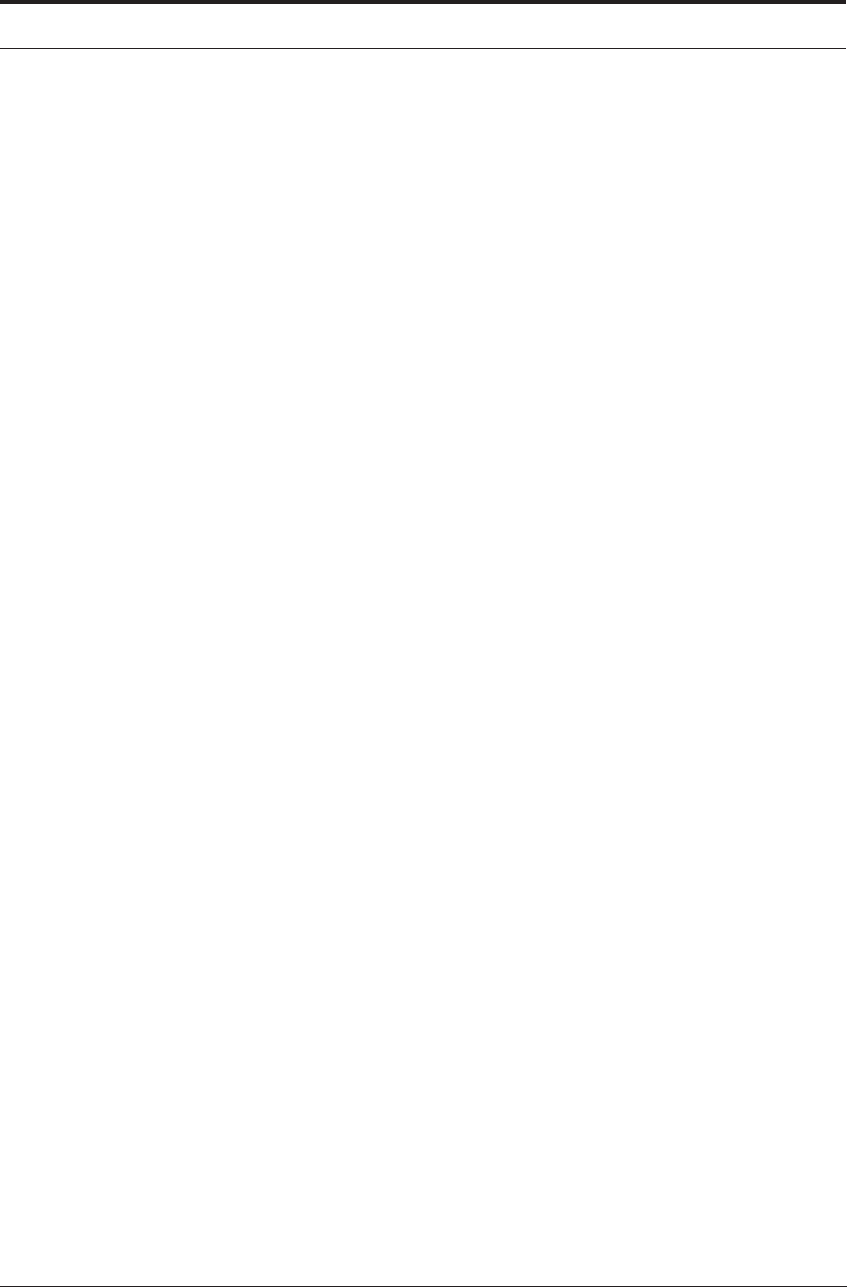
194 CUTTING TOOL MATERIALS II: CEMENTED CARBIDES
on the order of 1 ms, at temperatures of ∼800°C. Rates of diffusion and solution must increase
greatly in such structures, as Loladze
20
has pointed out, but no experimental data exist for these
conditions. There is also evidence of a much higher concentration of dislocations in carbide
grains at the interface than in the body of the tool.
19
These could accelerate the loss of metal and
carbon atoms from surfaces subjected to high shear stress. Mechanical removal of discrete parti-
cles of tool material, too small to be observed by electron microscopy with sizes less than about
5 nanometers - may also occur in the complex wear process which is called here ‘diffusion
wear’.
There must be some solubility for diffusion to take place at all. It has been shown that 7% of
WC can be dissolved in iron at 1250°C. The rate of diffusion wear depends on what is some-
times called the “compatibility” of the materials; large differences in diffusion wear rate occur
with different tool and work materials. The rate of wear is more dependent on the chemical prop-
erties than on the mechanical strength or hardness of the tool, provided the tool is strong enough
to withstand the imposed stresses. It is for this reason that the higher hardness of cemented car-
bides with fine grain size is not reflected in improved resistance to diffusion wear. In fact coarse-
grained alloys are rather more resistant than fine-grained ones of the same composition, but the
difference is small.
The rate of diffusion wear depends on the rate at which atoms from the tool dissolve and dif-
fuse into the work material and consideration is now given to the question - “Which atoms from
the tool material are most impregnating”? Recall that in the case of high speed steels, the iron
atoms from the matrix diffused into the work until the isolated alloy carbide particles, which
remain practically intact, were undermined and carried away bodily (Figures 6.17, 6.18 and
6.19). With cemented carbide tools also, the most rapid diffusion is by the cobalt atoms of the
tool, and the iron atoms of the work material. The carbide grains, however, are not undermined
and carried away for two reasons. First, because the carbide particles are not isolated, but consti-
tute most of the volume of the cemented carbide, supporting each other in a rigid framework.
Second, when cobalt atoms diffuse out of the tool, iron atoms diffuse in, and iron is almost as
efficient in “cementing” the carbide as is cobalt. Carbon atoms are small and diffuse rapidly
through iron, but those in the tool are strongly bonded to the tungsten and are not free to move
away by themselves.
TEM observations (Figure 3.12) show no structural changes in carbide grains within dis-
tances of 0.01μm of the interface. Changes would be observed if carbon atoms were lost from
the carbide without loss of tungsten atoms. It is the rate of diffusion of tungsten and carbon
atoms together into the work material which controls the rate of diffusion wear. This depends not
only on the temperature, but also on the rate at which they are swept away - i.e. on the rate of
flow of the work material very close to the tool surface - at distances of 0.001-1 μm. Just as the
rate of evaporation of water is very slow in stagnant air, so the rate of diffusion wear from the
tool is low where the work material is stationary at, and close to, the tool surface. At the flank of
the tool, the rate of flow of the work material close to the tool surface is very high (Figure 5.2a),
and diffusion may be responsible for a high rate of flank wear even when the nearby rake face
surface is practically unworn. In Figure 3.7 the carbide grains on the flank can be seen to be
smoothly worn through. Under conditions of seizure, the smooth wearing through of carbide
grains can be regarded as a good indication that a diffusion wear process is involved.