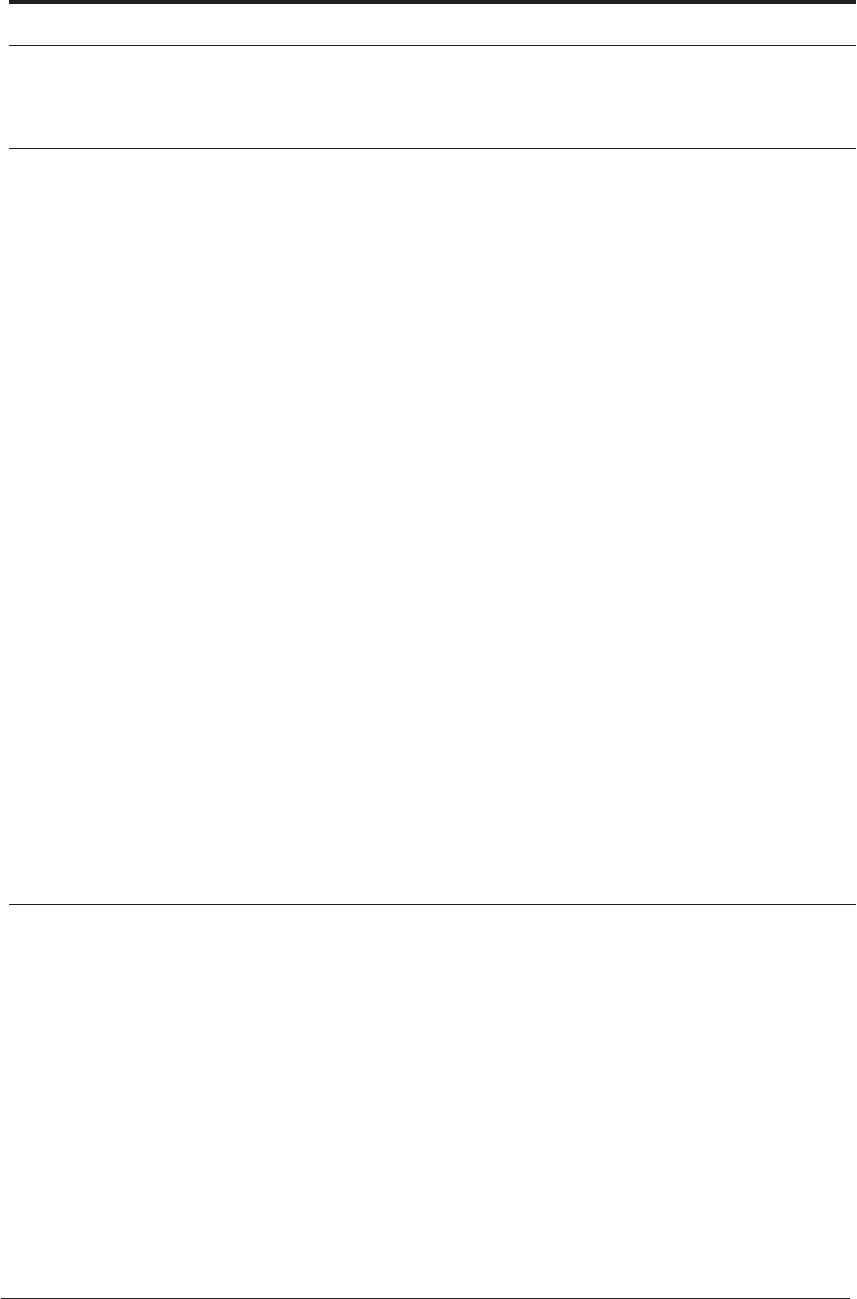
CONCLUSION 173
6.10 CONCLUSION
High speed steel tools, first demonstrated in 1900, were the product of an intense technological
research program to determine the most efficient tool steel composition and heat treatment for
the rough machining of steel. They made possible the cutting of steel at about four times the rate
of metal removal achieved with carbon steel tools. This advance was made possible by retention
of compressive strength of the order of 1500 MPa to temperatures in the range 550-650° C.
These properties are the result of precipitation hardening within the martensitic structure of the
chromium, tungsten, molybdenum, and vanadium tool steels after a very high temperature heat
treatment. The critical strength is retained at the same temperatures generated at the cutting edge
of tools when used to cut a wide range of engineering steels over a range of cutting speeds and
feeds useful in industrial machining.
The most important development has been the coating of tools with thin layers (
∼ 10 μm) of
TiN by a PVD process. Such coatings prolong tool life in most situations and in others give a
smoother surface finish on the machined part. Figures 3.25 to 3.30 are worth revisiting at this
point. The evidence indicates that the TiN coatings have several beneficial effects. They keep the
all-important cutting edge smooth and blemish free; they reduce friction on the rake face and
allow a smoother chip flow process - consequently both forces and temperatures are lower; they
reduce any heat due to rubbing on the clearance face. All these effects reduce the amount of sub-
surface strain going into the machined surface.
Correctly heat-treated high speed steel has adequate toughness to resist fracture in machine
shop conditions, and it is the combination of high-temperature strength and toughness that has
made this class of tool material a successful survivor for 100 years in the evolution of cutting
tool materials. It is significant that in those 100 years no new class of tool steel has superseded it.
The loss of strength and permanent changes in the structure of high speed steel when heated
above about 650° C limit the rate of metal removal when cutting high melting-point metals and
alloys.
6.11 REFERENCES
1. ‘Tool Steels’, Iron & Steel, Special Issue, (1968)
2. Brookes, K.J.A., World Directory and Handbook of Hard Metals, Engineers Digest (1987)
3. Osborn, F.M., The Story of the Mushets, Nelson (1952)
4. Taylor, F. W., Trans. A.S. M. E.,
28, 31 (1907)
5.American National Standards Institute B212.4-86, B212.12-91
6. Mukherjee, T., I.S.I. Publication,
126, 80 (1970)
7.Kirk, F.A., Child, H.C., Lowe, E.M. and Williams, T.J., I.S.I. Publication,
126, 67(1970)
8. Weaver, C., Unpublished work
9.Trent, E.M., Proc. Int. Conf M.T.D.R., Manchester, 1967, 629 (1968)
10. Hellman, P. and Wisell, H., Bulletin du Cercle d’Etudes des Metaux, p. 483 (Nov. 1975)
11. Ekelund, S., Fagersta High Speed Steel Symposium, p. 3 (1981)
12. Wright, P.K. and Trent, E.M., Metals Technology,
1, 13 (1974)