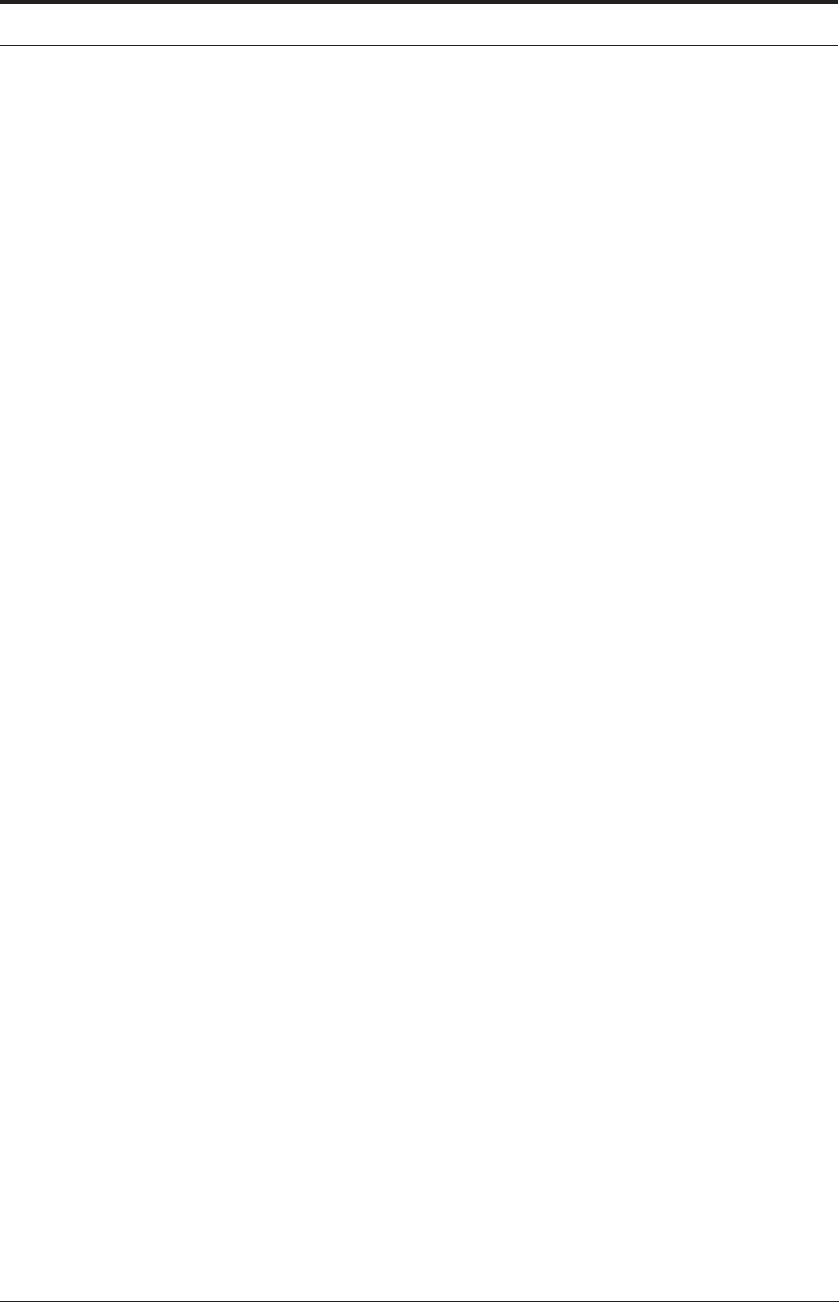
INFLUENCE OF INCREASING SPEED ON CHIP FORMATION 351
Ernst’s
25
three classical descriptions are described first:
• Discontinuous chips form at very low speeds. Low temperatures cause the first material to
strain harden and “stick” on the rake face. The incoming material is impeded by this stuck
material and homogeneous strain occurs in large chunks of material ahead of the tool. There
is often a “bulge” on the free surface. Eventually “something has to give” and a crack is ini-
tialed on a long shear plane. A discontinuous chip segment then pops free and “slips” off the
tool. The “stick-slip” cycle then repeats.
• Built-up-edge effects form at modest speeds up to 30m min
-1
for medium carbon steel. Tem-
peratures are still low and a severely strain hardened “cap” remains at the cutting edge. A
continuous chip flows over this cap (see Figure 3.21).
• Continuous chips form at higher speeds and hence higher temperatures. The temperatures
eliminate the built-up-edge and a flow zone replaces it on the rake face. In the primary zone,
“adiabatic shear lamellae” create a distinct shear zone, and chip flow is very smooth.
• The fourth type of chip may be termed segmented, serrated or shear-localized. The compre-
hensive research of Komanduri and colleagues has established much of the data in the two
paragraphs below, on when particular materials experience this transition.
11-15
There is a transition from a continuous chip to a segmented chip with increase in cutting
speed for most materials. This type of chip persists with further increase in speed. No additional
transitions or reversal to a continuous chip have been observed at least up to 30,488 m min
-1
(or
100,000 ft./min). The deformation of the chip is inhomogeneous on a gross level. In a narrow
band between the segments, deformation is very high. By contrast, inside the segments the
deformation is relatively very low. Recht also observed that exceptionally narrow shear bands
(as low as 0.002 mm) are separated by much larger regions of little strain. Physically, such seg-
mental chips resemble a discontinuous chip.
The transition speed at which the chip form changes from a continuous to a segmented or
shear-localized chip is found to be different for different work materials.
11-15
For example, it is
only a few m min
-1
or less in the case of titanium alloys, about 61 m min
-1
in the case of nickel-
base superalloys, and above 61 m min
-1
and complete at about 244 m min
-1
in the case of AISI
4340 steel (325 BHN). The speed at which catastrophic shear develops and the cutting speed at
which individual segments are completely isolated are found to decrease with increase in the
hardness of an AISI 4340 steel. Similar results are obtained with titanium alloys and nickel-
base superalloys.
Sullivan Wright and Smith
26
showed that the transition speed from continuous to segmented
for austenitic stainless steel is 35 m min
-1
. They observed such chip types up to a high speed of
300 m min
-1
, where tool life with carbide tools became impracticably low. These experiments
are described in detail in the next main section.
As a final note in this overview section, it has been verified in all the research so far, that the
segmented chip formation is not triggered by machine-tool vibration but is related to the inher-
ent metallurgical features of the workmaterial for the machining conditions used. Of course,
once these metallurgical instabilities are triggered, they drive regenerative chatter in the mate-
rial, the toolholder and the machine tool.
Thus, any thing that can be done to reduce the intensity of the segmentation is always benefi-
cial to the overall machining performance. And if such “difficult-to-machine” alloys can be
processed on the stiffest available machine tools in a particular factory, then at least a challeng-
ing situation will be held under the best control.