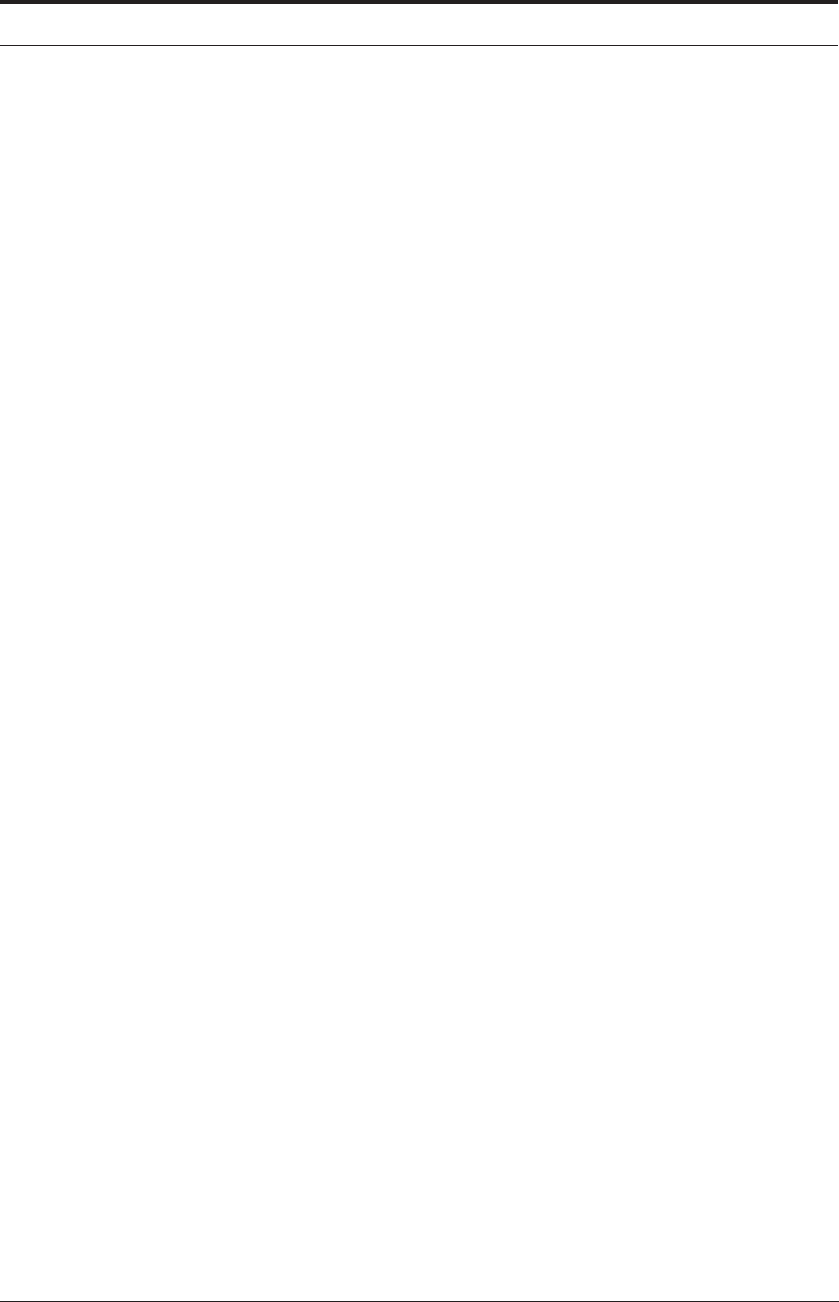
AEROSPACE ALUMINUM AND TITANIUM 361
the equation in chapter 5) and a power series expansion in temperature for thermal softening.
Very importantly, the code also includes a power viscosity law for strain rate sensitivity. Note
that this viscosity term for strain rate has already been introduced in equation 11.1 as a funda-
mental material constant at high strain rates in “Region IV”.
The importance of including the strain rate effects cannot be emphasized enough. For the alu-
minum alloy, Sandstrom and Hodowany did not obtain satisfactory agreement with experiment
when “standard handbook” data were used. Disagreement was observed both in cutting force
trends vs. cutting speed, and in observed chip morphology. However, these issues were resolved
when they employed experimental shock physics techniques to derive material properties at
high strain rates and elevated temperatures.
11.8.2 Chip morphology of 7050-T7451 aluminum and Ti-6A1-4V titanium
11.8.2.1 7050-T7451 aluminum
The computed effective plastic strain field for high-speed machining of the aluminum alloy
is shown in Figure 11.15. It compares well with an image of an actual machining chip obtained
under corresponding conditions. Once Sandstrom and Hodowany used the high strain rate data
for the aluminum alloy, good agreement was observed both in absolute magnitude of cutting
forces, and in cutting force trends vs. cutting speed.
From the primary zone, the average temperature rise in the bulk of the chip was found to be
about 105
o
C. Similar temperature fluctuations have been experimentally measured during Kol-
sky bar tests of similar materials.
30
Individual values between 120 and 190
o
C were isolated in
the shear localized thinner bands between the segments.
By contrast, in the secondary shear zone, the temperature and effective plastic strain rose
dramatically. At the rear of secondary shear, temperatures approached 660
o
C, approximately to
the melting point, and effective plastic strain exceeded 2,000 percent. The gradient of strain
across the chip is greater than that of temperature because there has been time for heat to diffuse
across the chip and into the tool. In contrast, shear is effectively localized in the secondary
shear zone, resulting in a sharp strain profile.
11.8.2.2 Ti-6A1-4V mill-annealed ELI titanium
A similar result for titanium is shown in Figure 11.16. Frame C-1 shows the configuration
before cutting begins. In frame C-2, a shear band is well developed and is being forced up the
tool rake face; the tangential cutting force measured by Sandstrom and Hodowany was on its
way to its peak value. At frame C-3, the material has just begun a new shear instability in the
primary shear zone, relieving stress there; tangential force fell to nearly its minimum value. In
frame C-4 the shear plane of C-3 has become localized and has begun to be forced up along the
rake face; tangential force was again rising.
At frame C-5 shear is arrested but just about to begin again in the primary shear zone. The
system has not yet relieved stresses there - thus tangential force was still at its maximum and
was about to reduce as this shear plane developed. Note that, at an instant after C5, this will be
a “long shear plane of low angle” similar to the Sullivan, Wright and Smith model. Once this
shear band has been initiated, the shear plane gets shorter and the angle is greater. It is as if the
system “prefers” this higher-shear-angle solution but cannot remain there because of the stick-
slip phenomenon.