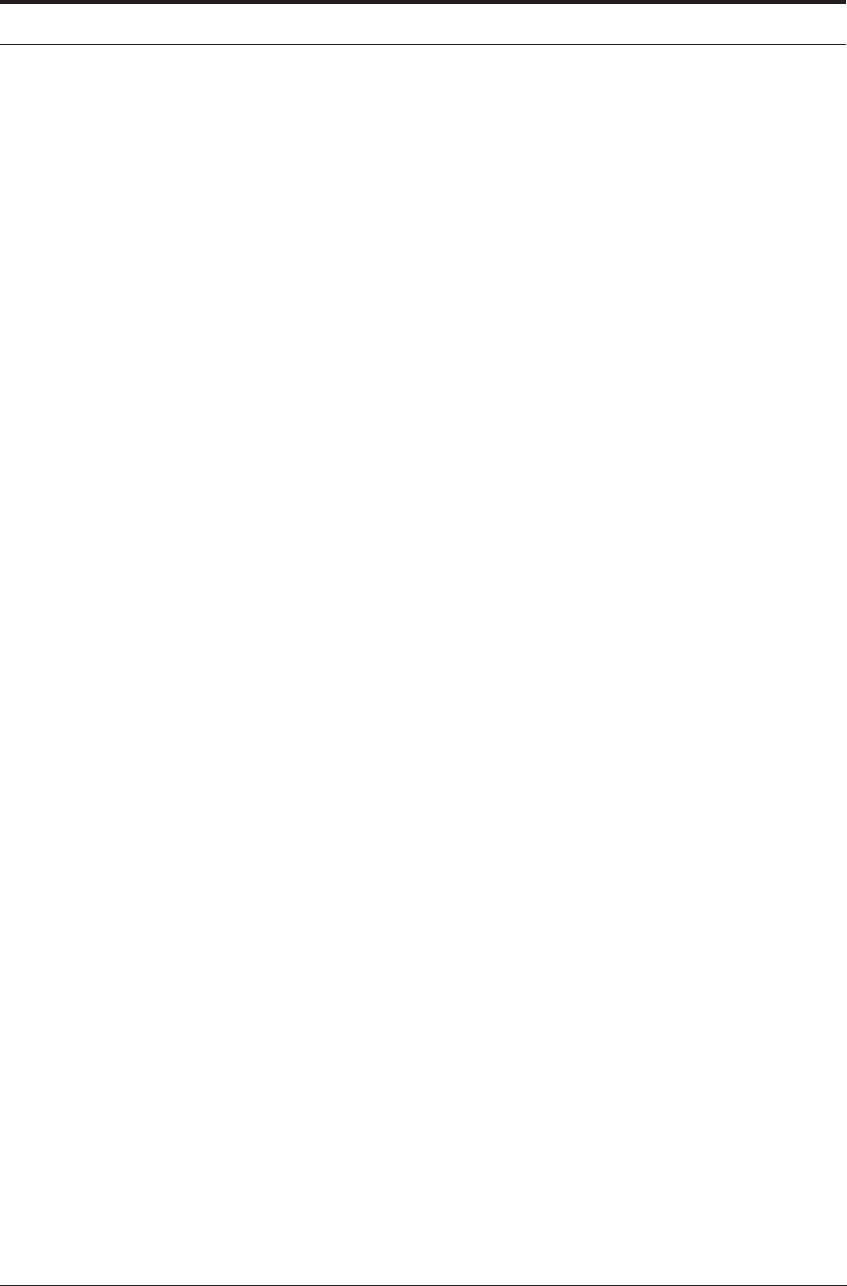
386 MODELING OF METAL CUTTING
12.5.4.1 Lagrangian formulation
In a Lagrangian formulation, the mesh is “attached to the workpiece”. In a virtual sense it
resembles the experiments in which researchers etch a photogrid onto the workpiece and then
study its deformation during cutting. The tool or workpiece is advanced through predefined dis-
placement increments, and the finite element solution is obtained. The displacement increment is
a function of the time step in explicit solution methods.
32,33
This can be related to the material
removal rate during cutting. By contrast, in an implicit solution,
34-37
the time step has no physi-
cal significance. In the various papers in the literature, different material models are used: they
include i) elastic-plastic, ii) only plastic, iii) viscoplastic, and iv) additive
33
as well as
multiplicative
32
decomposition of elastic and plastic strains.
From a civil engineering (structural) viewpoint, the application of finite element analysis for
stress analysis leads to a system equation for the nodal displacement vector
{u} of the system as
follows:
(12. 20)
where
[K] = the global stiffness matrix and
{R} = the load vector which include all its applied loads.
The solution of the system of the equation yields the nodal displacement vector {u} from
which the element strains and hence stresses can be calculated.
By contrast from a metal cutting viewpoint, the assumptions used in the above equation 12.20,
namely small displacement linear analysis and constant material properties, are no longer valid.
In the updated Lagrangian formulation, because the elements move with the workpiece, they
experience both large plastic deformation and rigid body motion. Under such circumstances, the
larger deformations, and the changing material properties due to stress and strain in the material,
need to be considered. The global stiffness matrix [K] is no longer constant. The stiffness matrix
is dependent on the current geometry and the stress history imposed by the loading sequence.
Since the governing equations are now nonlinear, the system must be solved iteratively on the
computer.
The advantage of the updated Lagrangian formulation is that the tool can be simulated from
the start of cutting to a steady-state. One of the disadvantages, however, is that the model
requires large computational times to reach steady-state conditions. In addition, a material fail-
ure and “parting-line or separation” mechanism has to be provided to allow the chip to sepa-
rate from the workpiece.
In the Lagrangian formulation, this “parting-line” or “separation” mechanism of the chip from
the parent workpiece material ahead of the tool tip remains a significant and controversial issue
for researchers. Nodes on this line are separated, and the line “unzipped”, when the tool tip is
sufficiently close, or when a certain level of plastic strain is attained. Various schemes have been
employed as criteria to part the chip: they include effective strain,
34
geometric distortion,
38
and
crack generation and propagation.
39
To implement the chip parting line, several algorithms have
been used: the slide-line,
34
node/element birth and death,
40
and remeshing.
32
K[]u{} R{}=