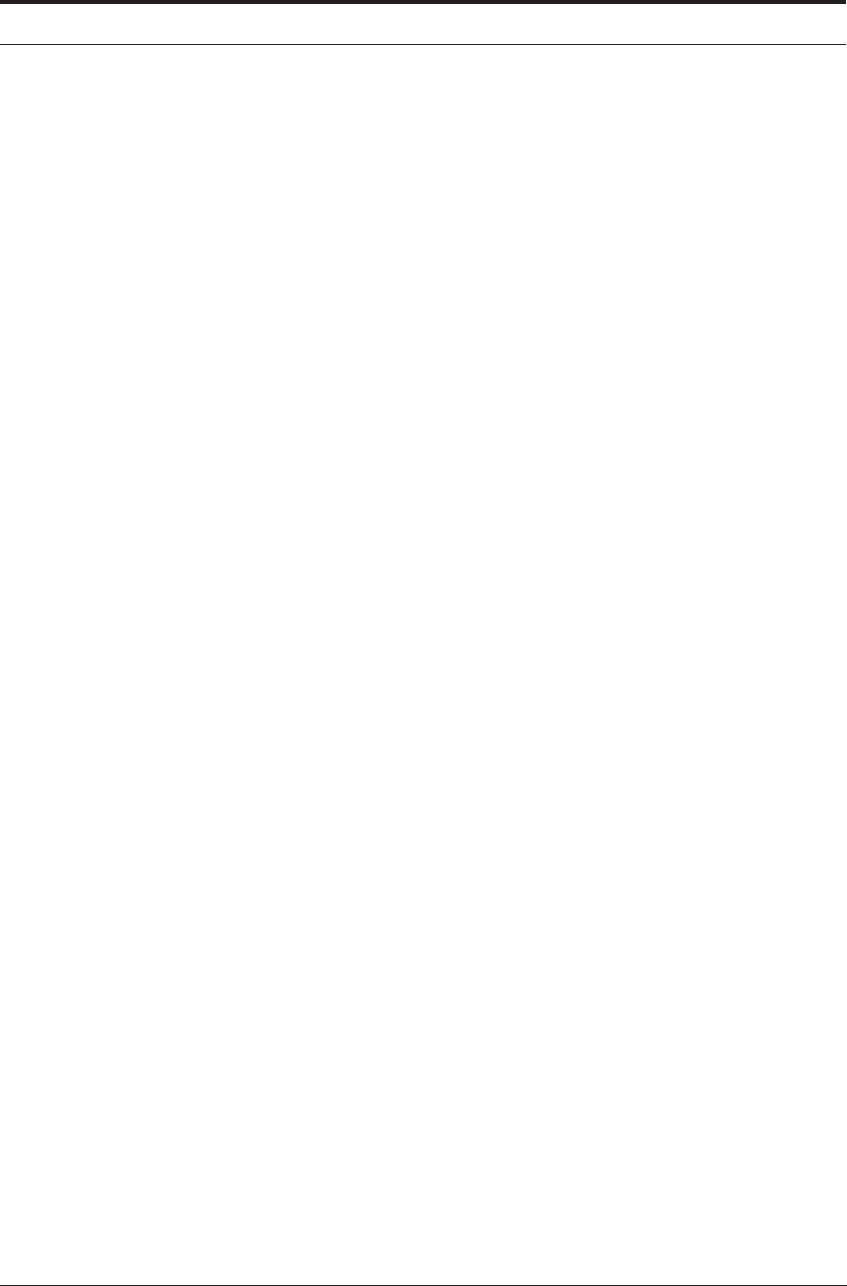
376 MODELING OF METAL CUTTING
12.4.2 Component accuracy - EMSIM
The “end-milling simulation” - EMSIM - uses a mechanistic model of the end-milling process
for the prediction of cutting forces and tool deflections. This “indented-ski-slope” deflection is
schematically shown in Figure 2.6. For the analysis, the flutes of the end-mill are decomposed
into thin axial slices (in a class situation it is useful to pile-up a column of pennies, or coins, rep-
resenting the sliced up end-mill). Force elements for each slice are then summed to predict the
instantaneous cutting force. This mechanistic force model was developed by Kline, DeVor et
al.
17-21
The elemental force components in the tangential and radial directions are shown in Fig-
ure 12.3, and can be expressed as:
(12. 5)
(12. 6)
K
t
´ and K
R
are empirical coefficients for the work material and tool material. D
z
is the thick-
ness of the axial disk. Also, t
c
is the instantaneous chip thickness going around the arc-shaped
slice. Examination of Figure 12.3 shows that as the tool edge first “bites into” the surface labeled
“B”, the instantaneous value of t
c
will be the same as the feed rate (f). But as the tool cuts around
the arc to “A”, it encounters a thinner and thinner instantaneous value of t
c
.
In the ideal case, the instantaneous value of chip thickness t
c
is approximated
15
by (t
c
=fsin α),
where f is the feed per tooth, and α is the angular position of the tooth in the cut, shown in Figure
12.3. However, the presence of runout greatly complicates the estimation of the instantaneous
chip thickness. Runout occurs if the cutting tool axis is not perfectly aligned with the tool-holder
and machine tool spindle. When the combined system spins around, the very tip of the tool
might thus create two errors. It might vibrate back-and-forth {the case of parallel axis offset
runout (PAOR)}, or it could scribe out a cutting circle on an axis that tilts relative to the tool’s
axis {the case of axis tilt runout (ATR)}.
For the basic case without runout, the angular position, α, of a tooth in the cut can be computed
for each axial disk element, i, and flute, k. The i value will be an integer value depending on the
number of axial slices used in the EMSIM run. A typical end-mill will have two or four flutes,
thus k will be 1, 2, 3, or 4. In the equation below, the j value can be regarded as an integer value
that “counts around” the arc during the computer simulation. So, for the simple case of the first
slice and first flute, i = 1, and k = 1. Then, the first term on the right side of the equation below is
one where θ(j) “counts around” the arc in Figure 12.3 by (say) 100 integer steps. The second
term in the {braces} on the right side of the equation is the vertical height of the engagement
point above the bottom of the disc being analyzed. Again, to show a simple case, the first disc is
i = 1 so the term in the square [brackets] becomes (D
z
/2) which is just the mid-point of that first
disc. This is multiplied by (tan(
λ)/R) to account for the helical twist. (Note, out of interest, if
there were no twist, the mill would be a reamer with straight edges - and α would just track
around in the same position as θ.
(12. 7)
F
t
i()δ K′
t
D
z
t
c
=
F
R
i()δ K
R
δF
t
=
α ijk,,()θj() γk 1–()+[]i 1–()D
z
D
z
2⁄+[]λ()tan R⁄{}+=