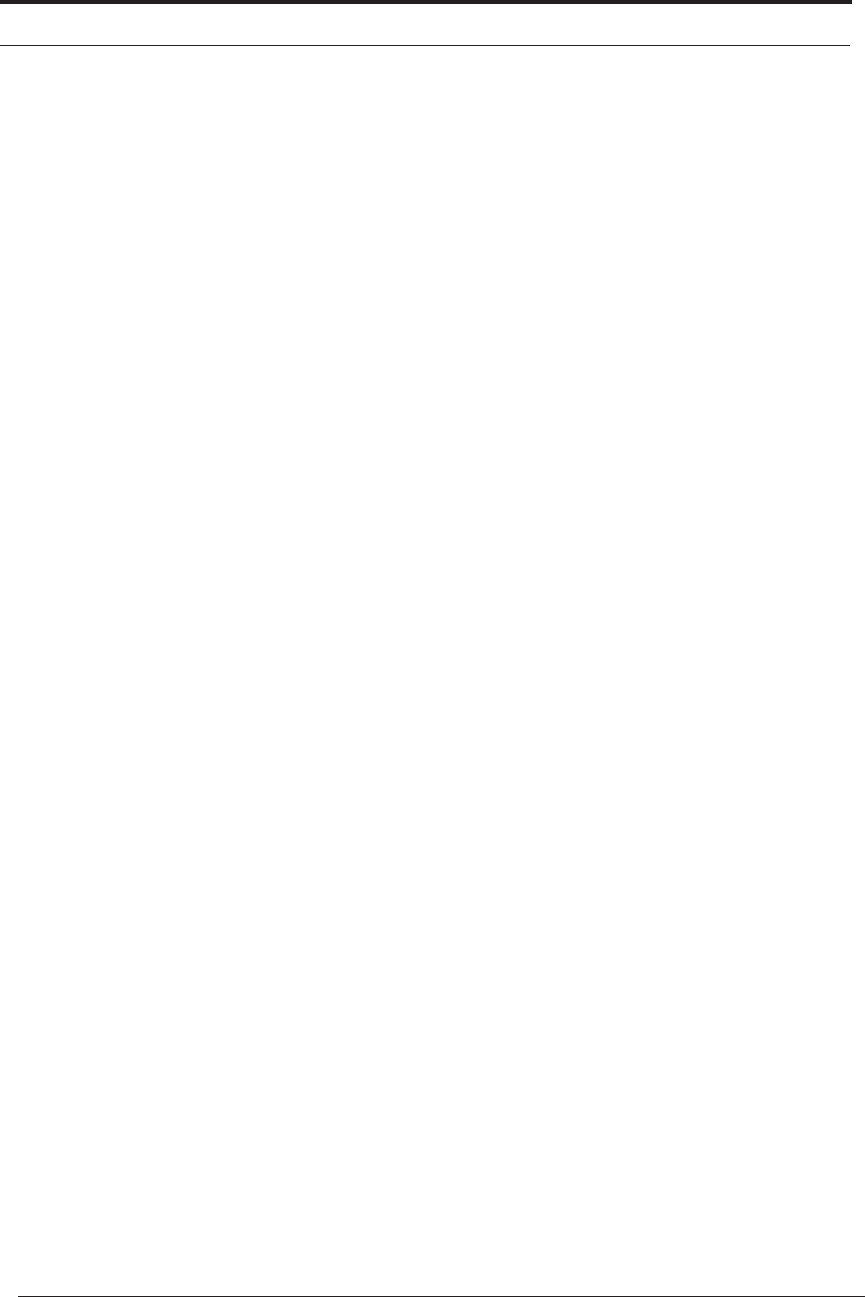
x FOREWORD
microscope during cutting, taking high-speed motion pictures of such, and making photomicro-
graphs of sections through chips still attached to workpieces. As a result of such studies, he
arrived at the concept of the “shear plane” in chip formation, i.e. the very narrow shear zone
between the body of the workpiece and the body of the chip that is being removed by the cutting
tool, which could be geometrically approximated as a plane. From such studies as those by
Ernst, Trent and others, an understanding emerged of the geometrical nature of such shear zones,
and of the role played by them in the plastic flows involved in the chip formation process in
metal cutting. That understanding laid the groundwork for the development, from the mid-1950s
on, of analytical, physics-based models of the chip formation process by researchers such as
Merchant, Shaw and others.
These fundamental studies of chip formation and tool wear, and the metal cutting technology
resulting from it, are still the base of our understanding of the metal cutting process today. As the
manufacturing industry builds on the astounding potential of digital computer technology, born
in the 1950s, and expands to Internet based collaboration, the resulting global enterprises still
depend on the “local” detailed fundamental metal cutting technology if they are to obtain
increasingly precise products at a high quality level and with rapid throughput. However, one of
the most important strengths that the computer technology has brought to bear on this situation is
the fact that it provides powerful capability to integrate the machining performance with the per-
formance of all of the other components of the overall system of manufacturing. Accomplish-
ment of such integration in industry has enabled the process of performing machining operations
to have full online access to all of the total database of each enterprise’s full system of manufac-
turing. Such capability greatly enhances both the accuracy and the speed of computer-based
engineering of machining operations. Furthermore, it enables each element of that system (prod-
uct design, process and operations planning, production planning and control, etc.), anywhere in
the global enterprise to interact fully with the process of performing machining and with its tech-
nology base. These are enablements that endow machining technology with capability not only
to play a major role in the functioning and productivity of an enterprise but also to enable the
enterprise as a whole to utilize it fully as the powerful tool that it is.
M. Eugene Merchant and Paul K. Wright, June 1999