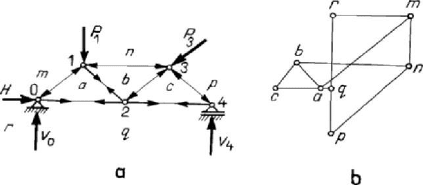
Statics
269
of node 2 (Fig.4.42,b) a.s.o. Sometimes, it is useful to combine the method of isolation
of nodes with the method of sections, as in the case of
K lattice trusses (Fig.4.38,d).
Figure 4.43. A triangular truss (a) and the corresponding Maxwell-Cremona draught (b).
The method of isolation of nodes is graphically concretized in the Maxwell-Cremona
draught. Let be the truss 0-1-2-3-4, acted upon by the forces
1
P and
3
P (Fig.4.43,a).
We use Bow’s notation, denoting by m, n, p, q, r the zones in which is divided the
exterior of the framework by the given and constraint forces which act upon it; as well,
we denote by a, b, c the zones in the interior of the truss, separated by bars or by the
corresponding efforts. Each given and external force and each effort will be expressed
in the form
N
αβ
, where the indices ,αβ correspond to the zones m, n, p, q, r, a, b, c
on one and the other part of the respective force. First of all, the polygon of given and
constraint forces, which is a closed one, is drawn. Then, one constructs the polygon of
forces for the equilibrium of each node, taking the forces clockwise around the node, in
the order in which they are met. We notice that to each node of the truss (Fig.4.43,a)
there corresponds a closed polygon in the Maxwell-Cremona draught (Fig.4.43,b),
while to each closed polygon of the truss (the polygons at the exterior of the truss are
closed at infinity) there corresponds a point of intersection of the respective sides on the
draught. Such figures are called reciprocal, while the method is called the method of
reciprocal polygons too. Denoting the intervals on the framework, the signs of the
efforts are determined on the figure, taking into account the direction along a polygon
according the clockwise direction around the corresponding node on the framework; if
the force stretches the node, then the effort is of tension (as in Fig.4.41), otherwise, it is
of compression.
The compound structures may be studied analogously, by the methods indicated
above. In the case of complex structures in which there is not one node with only two
unknowns and not one section cutting only three non-concurrent members or for which
one cannot make a decomposition in simple structures to which the application of these
methods be possible, one must make – in general – a study of the whole framework;
such a study involves the solution of a system of
2n linear algebraic equations for the
n nodes of the truss. But, from case to case, one can apply the method of bars
replacing of Henneberg or the two sections method of S.A. Tsaplin.
The spatial articulated systems are also systems of bars linked by hinges so as to
form a non-deformable structure from a geometric point of view, and where the loads
are applied at the nodes; but the members of the truss are no more coplanar.
The simple articulated systems are those obtained by joining tetrahedra formed by
bars; such a tetrahedron has six bars, corresponding to its sides. By complete induction,
one can show that