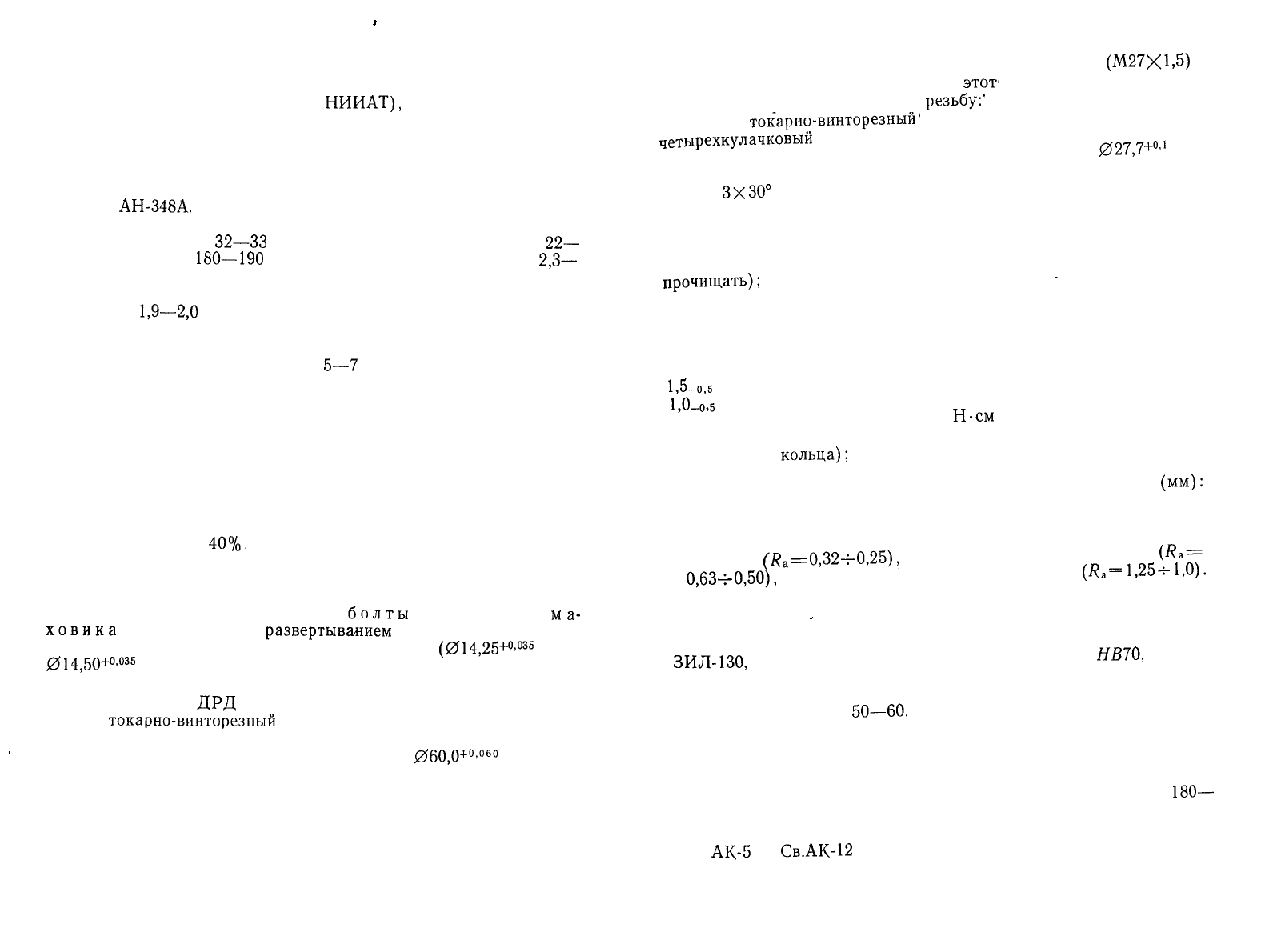
щей нормализацией, проточкой шеек, упрочнением галтелей по-
верхностным пластическим деформированием, закалкой их ТВЧ,
шлифованием и полированием под размер рабочего чертежа.
Применяют также наплавку под слоем легированного флюса
(технология способа предложена
НИИАТ),
после которой шей-
ки коленчатого вала не требуют термической обработки. В этом
случае легированный флюс используется при наплавке цилинд-
рической части шатунных и коренных шеек пружинной проволо-
кой II класса 01,6 мм. Наплавку галтелей шатунных шеек про-
изводят электродной проволокой СВ-08 01,6 мм под обычным
флюсом
АН-348А.
Рекомендуют следующие режимы наплавки
цилиндрической части коренных и шатунных шеек: напряжение
при холостом ходе
32—33
В, напряжение при наплавке
22—
24 В, сила тока
180—190
А, частота вращения вала
2,3—
2,4 об/мин при наплавке коренных шеек и 2,7 об/мин при на-
плавке шатунных шеек, шаг наплавки 4 мм/об, скорость подачи
проволоки
1,9—2,0
м/мин, индуктивность — все витки дросселя
РСТЭ-34. Галтели шатунных шеек наплавляют при следующем
режиме: напряжение в режиме холостого хода и при наплавке и
сила тока те же, индуктивность
5—7
витков дросселя РСТЭ-34,
частота вращения вала 1,5 об/мин, скорость подачи проволоки
2,0 м/мин.
При этом способе план операций по восстановлению шеек ко-
ленчатого вала может быть следующим: наплавка коренных и
шатунных шеек, черновое шлифование коренных и шатунных
шеек, правка вала, чистовое шлифование шеек и их полирование
под размер рабочего чертежа.
Упрочнение наклепом галтелей шатунных шеек, восстанов-
ленных по указанной технологии, позволяет повысить их устало-
стную прочность до
40%.
После восстановления коленчатые валы обмывают снаружи
и промывают их масляные каналы в специальной ванне моющей
жидкостью под давлением 0,5 МПа в течение 20 мин.
Изношенные отверстия под
болты
крепления
ма-
ховика
восстанавливают
развертыва-нием
их в сборе с махови-
ком под один из двух ремонтных размеров
(014,25+°'
035
или
014,50+°'
035
мм), одинаковых
для
всех
отверстий.
Изношенное отверстие под подшипник восстанавли-
вают постановкой
ДРД
При этом коленчатый вал устанавлива-
ют на
токарно-винторезный
станок, используя в качестве базо-
вых поверхностей шейки под распределительную шестерню и
пятую коренную, растачивают отверстие до
060.0-
1
-
0
'
060
мм, за-
прессовывают ремонтную втулку до упора и растачивают ее до
размера по рабочему чертежу.
Биение торцовой поверхности фланца устраняют протачива-
нием ее «как чисто», выдерживая толщину фланца не менее
11,0
мм.
Износ наружной поверхности фланца устраня-
ют накаткой (шаг сетчатой накатки 1,2мм), хромированием или
260
наплавкой с последующей обработкой до размера рабочего чер-
тежа.
При повреждении резьбы под храповик
(М27Х1.5)
менее двух ниток ее прогоняют под
этот'
же размер. При срыве
двух ниток нарезают ремонтную
резьбу:
4
коленчатый вал устанав-
ливают на
токарно-винторезный'
станок (фланец закрепляют в
четырехкулачковый
патрон, первую коренную шейку — в лю-
нет), растачивают отверстие с сорванной резьбой до
027,7+°''
мм
на длине 45 мм и до 031 мм на длине 6 мм, исправляют резцом
фаску
3X30°
и нарезают резьбу МЗОХ 1,5 кл. 2.
После восстановления коленчатые валы должны отвечать
следующим техническим требованиям:
полости масляных каналов шатунных шеек должны быть аб-
солютно чистыми (пробки необходимо выкручивать и полость
прочищать);
нецилиндричность поверхностей А и Д (см. рис. IV.4.4) дол-
жна быть не более 0,005 мм;
непараллельность осей шатунных и коренных шеек на длине
каждой шатунной шейки должна быть не более 0,020 мм;
радиусы галтелей шатунных шеек должны быть в пределах
1,5-о,s
мм, передней коренной 1,5±0,5 мм, остальных коренных
1,0-0,5
мм;
допустимый дисбаланс вала 0,3
Н-см
на каждом конце (при
балансировке на каждую шатунную шейку должны быть наде-
ты разрезные
кольца);
при установке вала на первую и пятую коренные шейки ра-
диальное биение поверхностей должно быть не более
(мм):
Г — 0,05, В — 0,04, Ж — 0,05; торцовое биение поверхностей
должно быть не более: В — 0,07, И — 0,06, К — 0,06;
шероховатость поверхности А должна соответствовать
9а классу
(R
a
=0,324-0,25),
поверхности К — 8а классу
(R
&
==
=
0,63-4-0,50),
поверхностей Е, Ж, Б — 7а классу
(Я
а
=
1,25-И,0).
5. Головки цилиндров
Головки цилиндров (рис. IV 4.5) изготавливают у двигателей
ЗИЛ-130,
ЗМЗ-53 из алюминиевого сплава АЛ4,
ЯВ70,
у ЯМЗ
из легированного чугуна. Вставные седла клапанов изготавли-
вают у двигателей ЗИЛ, ЗМЗ, и выпускные у ЯМЗ из легиро-
ванного чугуна, HRC
50—60.
Основные дефекты головок цилиндров приведены в табл.
IV.4.5.
Трещины в головках цилиндров из алюминиевого
сплава устраняют путем заварки. Сначала подготавливают тре-
щины к заварке, затем головку нагревают до температуры
180—
200°С и заваривают трещины. Наибольшее применение нашла
газовая сварка с использованием присадочной проволоки марок
Св.
АК.-5
и
Св.АК-12
и специального флюса для сварки алюми-
ниевого сплава. После заварки металлической щеткой удаляют
261