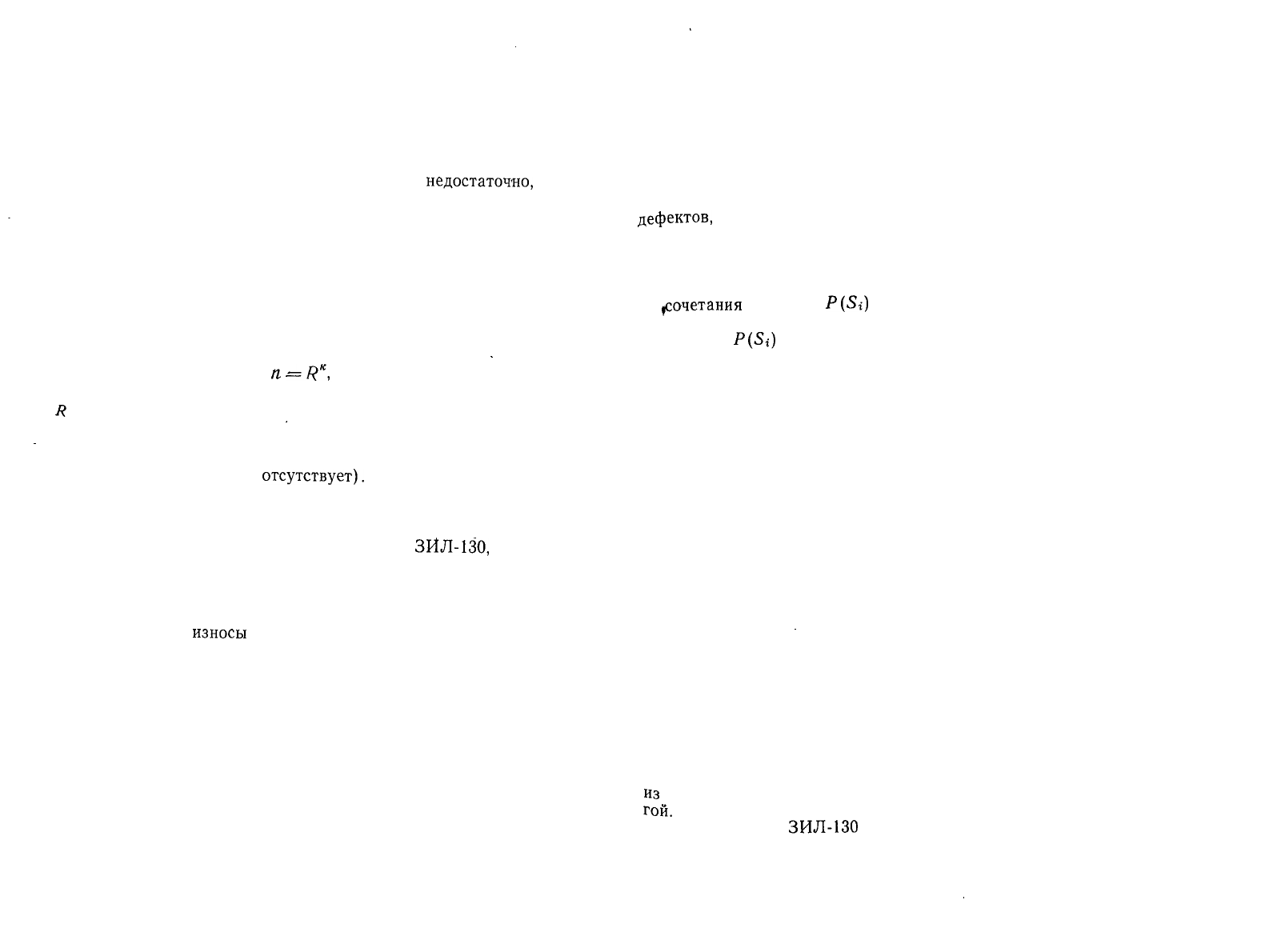
4. Закономерности поступления на восстановление деталей
с различным техническим состоянием
При подефектной технологии восстановления деталей решение
вопроса о возможности их повторного использования и выборе
рациональных способов устранения дефектов может приниматься
на основе данных о характере и величине износа. В случае про-
мышленного восстановления деталей по маршрутной технологии
наличие только этой информации совершенно
недостаточно,
так
как большое влияние при этом на выбор способов, а также после-
довательность операций восстановления оказывает совокупность
дефектов, составляющих тот или иной маршрут. Поэтому необхо-
димо исследовать не только распределение размеров поверхностей
изношенных деталей, но и выявить статистические закономерности
в образовании действительных сочетаний дефектов, оценить ве-
роятности поступления деталей по ним.
Общее число возможных состояний изношенной детали может
быть определено по формуле
я
*=/?*,
(IV.2.1)
где к — число возможных дефектов на детали;
R
— число уровней контролируемых параметров.
При контроле деталей по альтернативному признаку число
уровней контролируемого параметра равно двум (имеется дефект
на рабочей поверхности или
отсутствует).
Для сложных деталей, имеющих большое количество изна-
шивающихся поверхностей, число возможных состояний (сочета-
ний дефектов) достигает значительных величин. Например, про-
межуточный вал коробки передач автомобиля
ЗИЛ-130,
проверя-
емый согласно техническим условиям на контроль-сортировку по
десяти параметрам, может иметь 1024 возможных сочетаний де-
фектов, ведущий вал — 2048, фланец ведомого вала — 256. В
действительности детали имеют гораздо меньшее число сочетаний
дефектов, так как
износы
поверхностей у большинства деталей
взаимосвязаны. Это в значительной степени и обусловливает ус-
тойчивость естественных сочетаний дефектов.
Практика показывает, что, несмотря на случайный характер
образования тех или иных сочетаний дефектов, поступление
деталей на восстановление имеет вполне определенные законо-
мерности. Например, с увеличением объема выборки обследова-
ния частота поступления деталей с тем или иным состоянием
постепенно стабилизируется, приближаясь к какому-то постоян-
ному значению. При этом выявляются так называемые статисти-
ческие закономерности или устойчивость поступления деталей,
когда невозможно заранее предсказать, с каким именно сочетани-
ем дефектов поступает на контроль-сортировку та или иная де-
таль, но можно предсказать вероятность этого события по ре-
зультатам обследования большого количества таких деталей.
238
Исследование состояния значительной номенклатуры деталей,
анализ производственных условий их восстановления, а также на-
учно-исследовательских работ в области маршрутной технологии
позволили установить в качестве основных следующие признаки,
использование которых дает возможность объединить изношен-
ные детали с большим количеством возможных состояний в груп-
пу технологических маршрутов восстановления деталей.
Частота появления детали с определенным сочетанием дефек-
тов. Из всех возможных состояний детали необходимо прежде
всего выявить с заданной достоверностью устойчивые сочетания
дефектов,
наиболее вероятные из которых и являются базой при
формировании технологических маршрутов восстановления. Де-
фекты, составляющие такие сочетания, являются наиболее близ-
кими, так как их устранение производится по единому технологи-
ческому процессу. Следовательно, частота появления того или ино-
го
сочетания
дефектов
P(Si)
является основным признаком груп-
пирования различных дефектов в маршруты восстановления.
Частота
P(Si)
относится к типу классификационных призна-
ков с числом градаций, равным количеству выявленных сочета-
ний дефектов.
Функциональная связь поверхностей детали. Признак функци-
ональной связи поверхностей детали предполагает необходимость
включения в одни и те же маршруты, во-первых, дефектов, уст-
ранение которых по отдельности не обеспечивает необходимой
точности восстановления, и, во-вторых, дефектов, устранение од-
ного из которых автоматически ведет к устранению другого.
Первый случай предполагает тщательное изучение техничес-
ких условий рабочего чертежа детали, которые задают определен-
ную взаимосвязь между различными ее поверхностями в виде до-
пустимых отклонений в их взаимном расположении. Из-за пов-
реждений установочных баз в условиях ремонтного производства
зачастую трудно уложиться в пределы допуска во взаимном по-
ложении восстанавливаемых поверхностей относительно невосста-
навливаемых. Это приводит к нарушению работы сопряжений и,
в конечном счете, к снижению ресурса отремонтированных авто-
мобилей. В связи с этим необходимо более строго, чем в процессе
изготовления деталей, подходить к выбору установочных баз при
их восстановлении. Если все-таки отклонения во взаимном рас-
• положении превышают допустимые, необходимо включать в мар-
шрут восстановления соответствующие поверхности данной де-
тали.
Во втором случае поверхности детали конструктивно связаны
между собой таким образом, что устранение дефекта на одной
из
них приводит к одновременному устранению дефекта на дру-
гой.
Так, например, при устранении износа шлицев ведущего вала
коробки передач
ЗИЛ-130
(деталь 130-1701030) одновременно
Устраняется и износ шейки под передний шариковый подшипник,
так как технологический процесс в этом случае предусматривает
отрезание изношенного и напрессовку с последующей приваркой
239