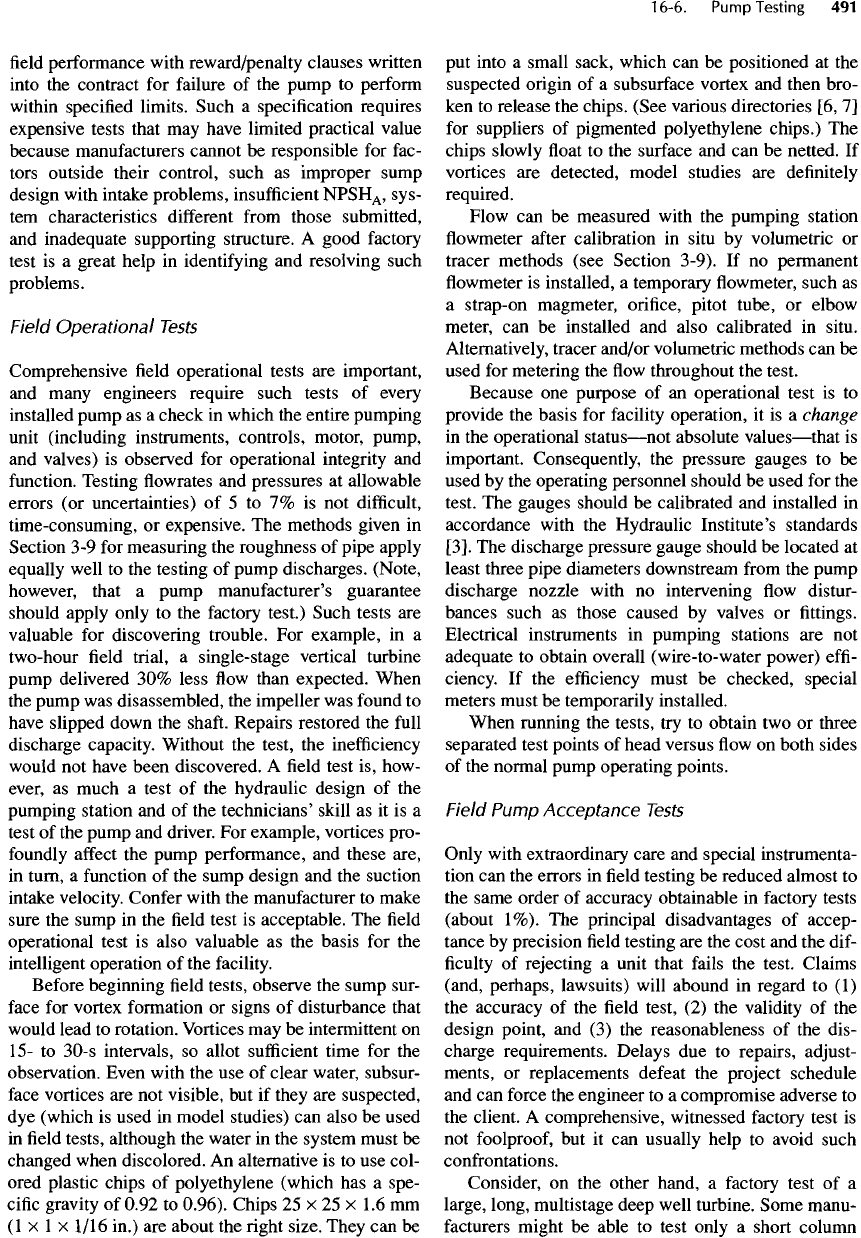
field
performance
with reward/penalty clauses written
into
the
contract
for
failure
of the
pump
to
perform
within
specified limits. Such
a
specification requires
expensive tests that
may
have limited practical value
because manufacturers cannot
be
responsible
for
fac-
tors outside their control, such
as
improper sump
design with intake problems,
insufficient
NPSH
A
,
sys-
tem
characteristics
different
from
those submitted,
and
inadequate supporting structure.
A
good factory
test
is a
great help
in
identifying
and
resolving such
problems.
Field
Operational
Tests
Comprehensive
field
operational tests
are
important,
and
many engineers require such tests
of
every
installed pump
as a
check
in
which
the
entire pumping
unit
(including instruments, controls, motor, pump,
and
valves)
is
observed
for
operational integrity
and
function.
Testing
flowrates and
pressures
at
allowable
errors
(or
uncertainties)
of 5 to 7% is not
difficult,
time-consuming,
or
expensive.
The
methods given
in
Section
3-9 for
measuring
the
roughness
of
pipe apply
equally
well
to the
testing
of
pump discharges. (Note,
however, that
a
pump manufacturer's guarantee
should
apply only
to the
factory test.) Such tests
are
valuable
for
discovering trouble.
For
example,
in a
two-hour
field
trial,
a
single-stage vertical turbine
pump
delivered
30%
less
flow
than expected. When
the
pump
was
disassembled,
the
impeller
was
found
to
have
slipped down
the
shaft.
Repairs restored
the
full
discharge capacity. Without
the
test,
the
inefficiency
would
not
have been discovered.
A field
test
is,
how-
ever,
as
much
a
test
of the
hydraulic design
of the
pumping
station
and of the
technicians' skill
as it is a
test
of the
pump
and
driver.
For
example, vortices pro-
foundly
affect
the
pump performance,
and
these
are,
in
turn,
a
function
of the
sump design
and the
suction
intake
velocity. Confer with
the
manufacturer
to
make
sure
the
sump
in the field
test
is
acceptable.
The field
operational test
is
also valuable
as the
basis
for the
intelligent operation
of the
facility.
Before
beginning
field
tests, observe
the
sump sur-
face
for
vortex formation
or
signs
of
disturbance that
would
lead
to
rotation. Vortices
may be
intermittent
on
15-
to
30-s
intervals,
so
allot
sufficient
time
for the
observation. Even with
the use of
clear water, subsur-
face
vortices
are not
visible,
but if
they
are
suspected,
dye
(which
is
used
in
model studies)
can
also
be
used
in
field
tests, although
the
water
in the
system must
be
changed when
discolored.
An
alternative
is to use
col-
ored plastic chips
of
polyethylene (which
has a
spe-
cific
gravity
of
0.92
to
0.96).
Chips
25 x 25 x 1.6 mm
(lxlxl/16
in.)
are
about
the right
size. They
can be
put
into
a
small sack, which
can be
positioned
at the
suspected origin
of a
subsurface vortex
and
then bro-
ken
to
release
the
chips. (See various
directories
[6, 7]
for
suppliers
of
pigmented polyethylene chips.)
The
chips slowly
float to the
surface
and can be
netted.
If
vortices
are
detected, model studies
are
definitely
required.
Flow
can be
measured with
the
pumping station
flowmeter
after
calibration
in
situ
by
volumetric
or
tracer methods (see
Section
3-9).
If no
permanent
flowmeter
is
installed,
a
temporary
flowmeter,
such
as
a
strap-on magmeter, orifice,
pitot
tube,
or
elbow
meter,
can be
installed
and
also calibrated
in
situ.
Alternatively, tracer and/or volumetric methods
can be
used
for
metering
the flow
throughout
the
test.
Because
one
purpose
of an
operational test
is to
provide
the
basis
for
facility operation,
it is a
change
in
the
operational
status
—
not
absolute
values
—
that
is
important. Consequently,
the
pressure gauges
to be
used
by the
operating personnel should
be
used
for the
test.
The
gauges should
be
calibrated
and
installed
in
accordance with
the
Hydraulic Institute's standards
[3].
The
discharge pressure gauge should
be
located
at
least three pipe diameters downstream
from
the
pump
discharge nozzle with
no
intervening
flow
distur-
bances such
as
those caused
by
valves
or fittings.
Electrical instruments
in
pumping stations
are not
adequate
to
obtain overall (wire-to-water power)
effi-
ciency.
If the
efficiency
must
be
checked, special
meters must
be
temporarily installed.
When running
the
tests,
try to
obtain
two or
three
separated test points
of
head versus
flow on
both sides
of
the
normal pump operating
points.
Field
Pump
Acceptance
Tests
Only with extraordinary care
and
special instrumenta-
tion
can the
errors
in field
testing
be
reduced almost
to
the
same order
of
accuracy obtainable
in
factory
tests
(about
1%).
The
principal disadvantages
of
accep-
tance
by
precision
field
testing
are the
cost
and the
dif-
ficulty
of
rejecting
a
unit that
fails
the
test. Claims
(and,
perhaps, lawsuits) will abound
in
regard
to (1)
the
accuracy
of the field
test,
(2) the
validity
of the
design point,
and (3) the
reasonableness
of the
dis-
charge requirements. Delays
due to
repairs,
adjust-
ments,
or
replacements defeat
the
project schedule
and
can
force
the
engineer
to a
compromise adverse
to
the
client.
A
comprehensive, witnessed factory test
is
not
foolproof,
but it can
usually help
to
avoid such
confrontations.
Consider,
on the
other hand,
a
factory test
of a
large, long, multistage deep well turbine. Some manu-
facturers
might
be
able
to
test only
a
short column