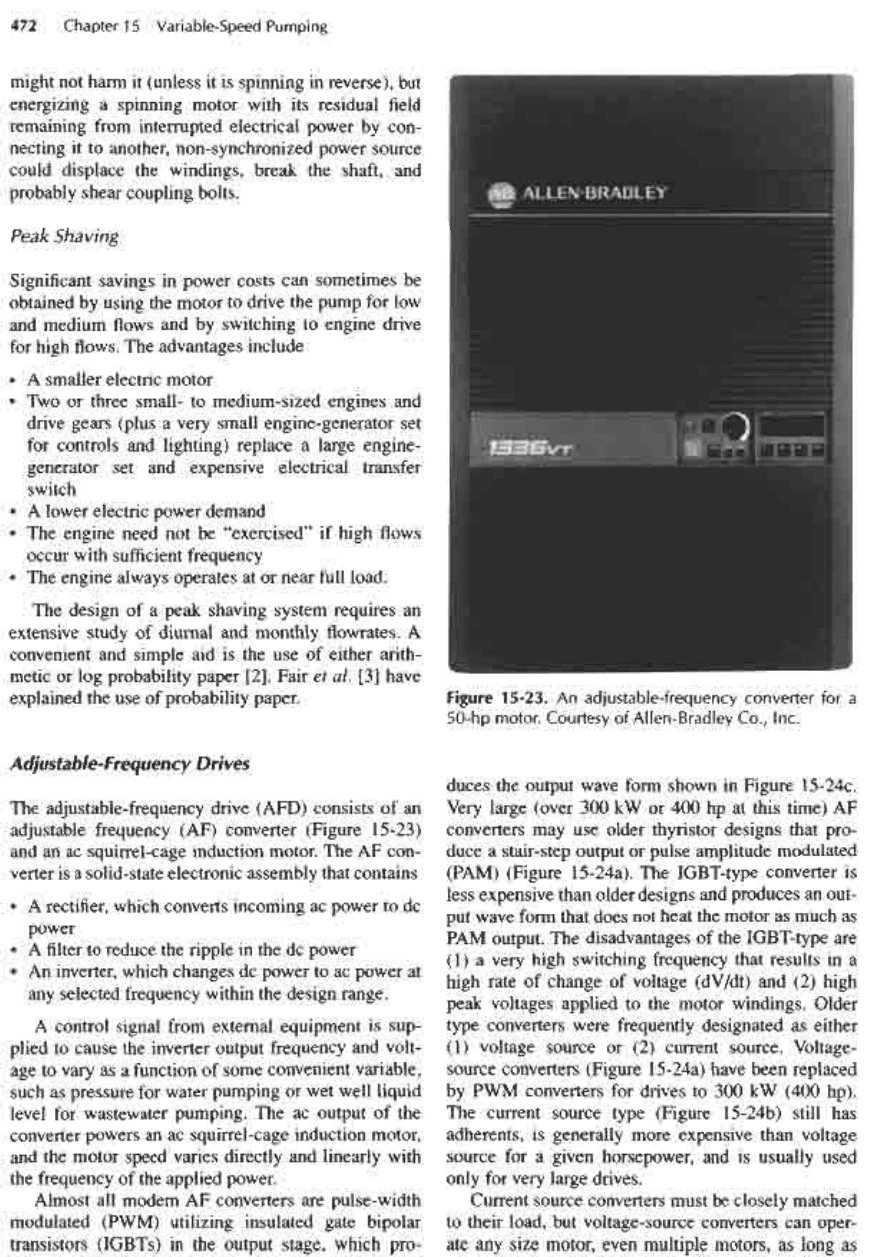
might
not
harm
it
(unless
it is
spinning
in
reverse),
but
energizing
a
spinning motor with
its
residual
field
remaining
from
interrupted
electrical
power
by
con-
necting
it to
another, non-synchronized power source
could
displace
the
windings, break
the
shaft,
and
probably shear coupling bolts.
Peak
Shaving
Significant
savings
in
power costs
can
sometimes
be
obtained
by
using
the
motor
to
drive
the
pump
for low
and
medium
flows and by
switching
to
engine drive
for
high
flows. The
advantages include
• A
smaller electric motor
• Two or
three
small-
to
medium-sized
engines
and
drive
gears (plus
a
very small engine-generator
set
for
controls
and
lighting) replace
a
large engine-
generator
set and
expensive electrical transfer
switch
• A
lower
electric
power demand
• The
engine need
not be
"exercised"
if
high
flows
occur with
sufficient
frequency
• The
engine always operates
at or
near
full
load.
The
design
of a
peak shaving system requires
an
extensive study
of
diurnal
and
monthly
flowrates. A
convenient
and
simple
aid is the use of
either arith-
metic
or log
probability paper
[2].
Fair
et
al
[3]
have
explained
the use of
probability paper.
Adjustable-Frequency
Drives
The
adjustable-frequency drive (AFD) consists
of an
adjustable
frequency
(AF) converter (Figure 15-23)
and
an ac
squirrel-cage
induction motor.
The AF
con-
verter
is a
solid-state electronic assembly that contains
• A
rectifier, which converts incoming
ac
power
to dc
power
• A filter to
reduce
the
ripple
in the dc
power
• An
inverter, which changes
dc
power
to ac
power
at
any
selected
frequency within
the
design range.
A
control signal
from
external equipment
is
sup-
plied
to
cause
the
inverter output
frequency
and
volt-
age to
vary
as a
function
of
some convenient variable,
such
as
pressure
for
water pumping
or wet
well liquid
level
for
waste
water
pumping.
The ac
output
of the
converter powers
an ac
squirrel-cage induction motor,
and
the
motor speed varies directly
and
linearly with
the
frequency
of the
applied power.
Almost
all
modern
AF
converters
are
pulse-width
modulated (PWM) utilizing insulated gate bipolar
transistors (IGBTs)
in the
output stage, which pro-
Figure
15-23.
An
adjustable-frequency
converter
for a
50-hp
motor.
Courtesy
of
Allen-Bradley
Co.,
Inc.
duces
the
output wave
form
shown
in
Figure
15-24c.
Very
large (over
300 kW or 400 hp at
this time)
AF
converters
may use
older thyristor designs that pro-
duce
a
stair-step output
or
pulse amplitude modulated
(PAM)
(Figure 15-24a).
The
IGBT-type
converter
is
less expensive than older designs
and
produces
an
out-
put
wave
form
that does
not
heat
the
motor
as
much
as
PAM
output.
The
disadvantages
of the
IGBT-type
are
(1)
a
very high switching frequency that results
in a
high
rate
of
change
of
voltage (dV/dt)
and (2)
high
peak voltages applied
to the
motor windings. Older
type
converters were
frequently
designated
as
either
(1)
voltage source
or (2)
current source. Voltage-
source converters (Figure
15-24a)
have
been
replaced
by
PWM
converters
for
drives
to 300 kW
(400 hp).
The
current source type (Figure
15-24b)
still
has
adherents,
is
generally more expensive than voltage
source
for a
given horsepower,
and is
usually used
only
for
very large drives.
Current
source
converters must
be
closely
matched
to
their load,
but
voltage-source converters
can
oper-
ate any
size motor, even multiple motors,
as
long
as