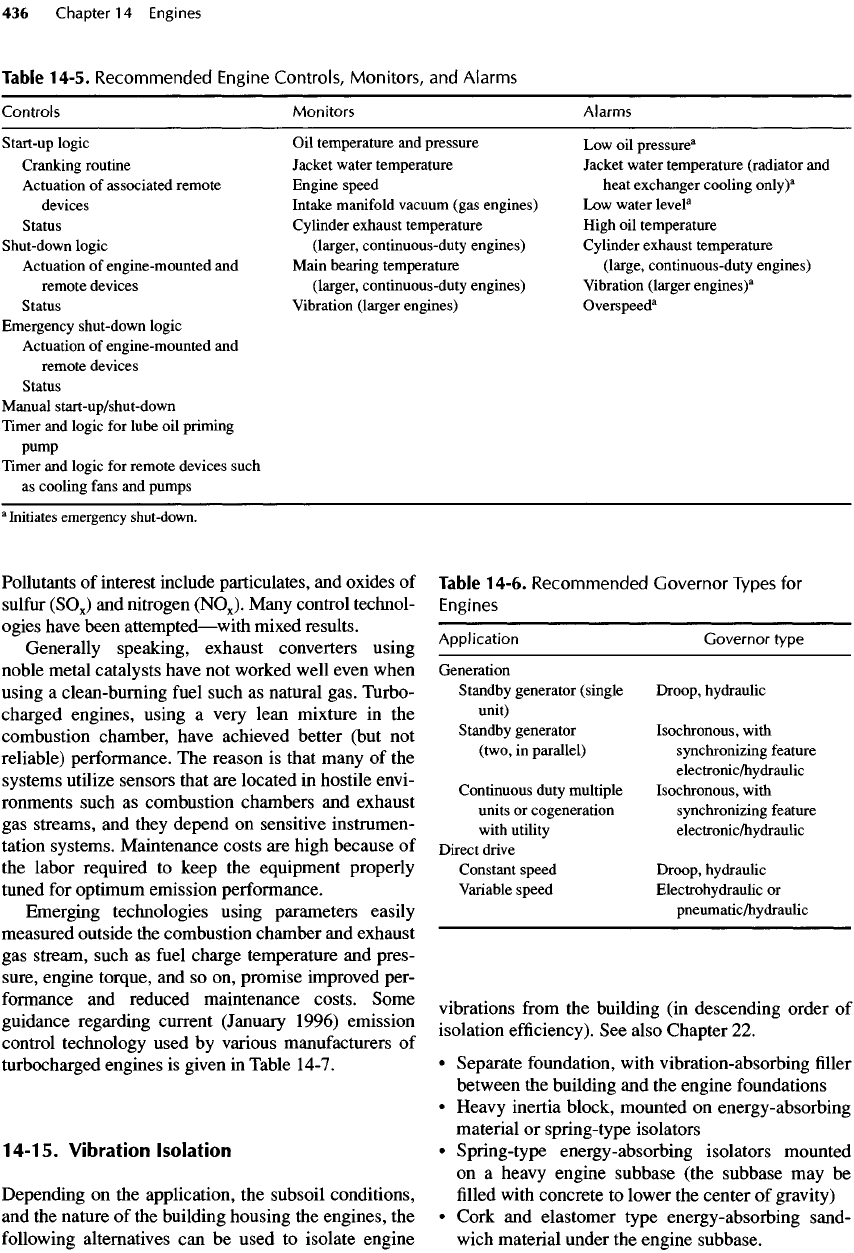
Pollutants
of
interest include
particulates,
and
oxides
of
sulfur
(SO
x
)
and
nitrogen
(NO
x
).
Many control technol-
ogies have
been
attempted
—
with
mixed
results.
Generally speaking, exhaust converters using
noble metal catalysts have
not
worked well even when
using
a
clean-burning
fuel
such
as
natural gas. Turbo-
charged engines, using
a
very lean mixture
in the
combustion chamber, have achieved better (but
not
reliable) performance.
The
reason
is
that many
of the
systems utilize sensors that
are
located
in
hostile envi-
ronments such
as
combustion chambers
and
exhaust
gas
streams,
and
they depend
on
sensitive instrumen-
tation
systems. Maintenance costs
are
high because
of
the
labor required
to
keep
the
equipment properly
tuned
for
optimum emission performance.
Emerging technologies using parameters easily
measured outside
the
combustion chamber
and
exhaust
gas
stream, such
as
fuel
charge temperature
and
pres-
sure, engine torque,
and so on,
promise improved per-
formance
and
reduced maintenance costs. Some
guidance regarding current (January 1996) emission
control technology used
by
various manufacturers
of
turbocharged
engines
is
given
in
Table
14-7.
14-15.
Vibration
Isolation
Depending
on the
application,
the
subsoil conditions,
and
the
nature
of the
building housing
the
engines,
the
following
alternatives
can be
used
to
isolate engine
Table
14-6.
Recommended
Governor
Types
for
Engines
Application
Governor type
Generation
Standby
generator (single Droop, hydraulic
unit)
Standby
generator Isochronous, with
(two,
in
parallel) synchronizing
feature
electronic/hydraulic
Continuous
duty
multiple Isochronous, with
units
or
cogeneration synchronizing
feature
with
utility
electronic/hydraulic
Direct drive
Constant
speed Droop, hydraulic
Variable
speed Electrohydraulic
or
pneumatic/hydraulic
vibrations
from
the
building
(in
descending
order
of
isolation
efficiency).
See
also Chapter
22.
•
Separate foundation, with vibration-absorbing
filler
between
the
building
and the
engine foundations
•
Heavy
inertia
block,
mounted
on
energy-absorbing
material
or
spring-type
isolators
•
Spring-type energy-absorbing isolators mounted
on
a
heavy engine subbase (the subbase
may be
filled
with
concrete
to
lower
the
center
of
gravity)
•
Cork
and
elastomer type energy-absorbing sand-
wich
material under
the
engine subbase.
Controls
Start-up
logic
Cranking
routine
Actuation
of
associated remote
devices
Status
Shut-down
logic
Actuation
of
engine-mounted
and
remote
devices
Status
Emergency
shut-down logic
Actuation
of
engine-mounted
and
remote devices
Status
Manual
start-up/shut-down
Timer
and
logic
for
lube
oil
priming
pump
Timer
and
logic
for
remote devices
such
as
cooling
fans
and
pumps
a
Initiates
emergency
shut-down.
Monitors
Oil
temperature
and
pressure
Jacket
water temperature
Engine speed
Intake
manifold
vacuum
(gas engines)
Cylinder
exhaust temperature
(larger,
continuous-duty engines)
Main
bearing temperature
(larger, continuous-duty engines)
Vibration
(larger engines)
Alarms
Low
oil
pressure
3
Jacket
water temperature (radiator
and
heat
exchanger cooling
only)
a
Low
water
level
8
High
oil
temperature
Cylinder exhaust temperature
(large,
continuous-duty engines)
Vibration
(larger
engines)
a
Overspeed
a
Table 14-5.
Recommended
Engine
Controls,
Monitors,
and
Alarms