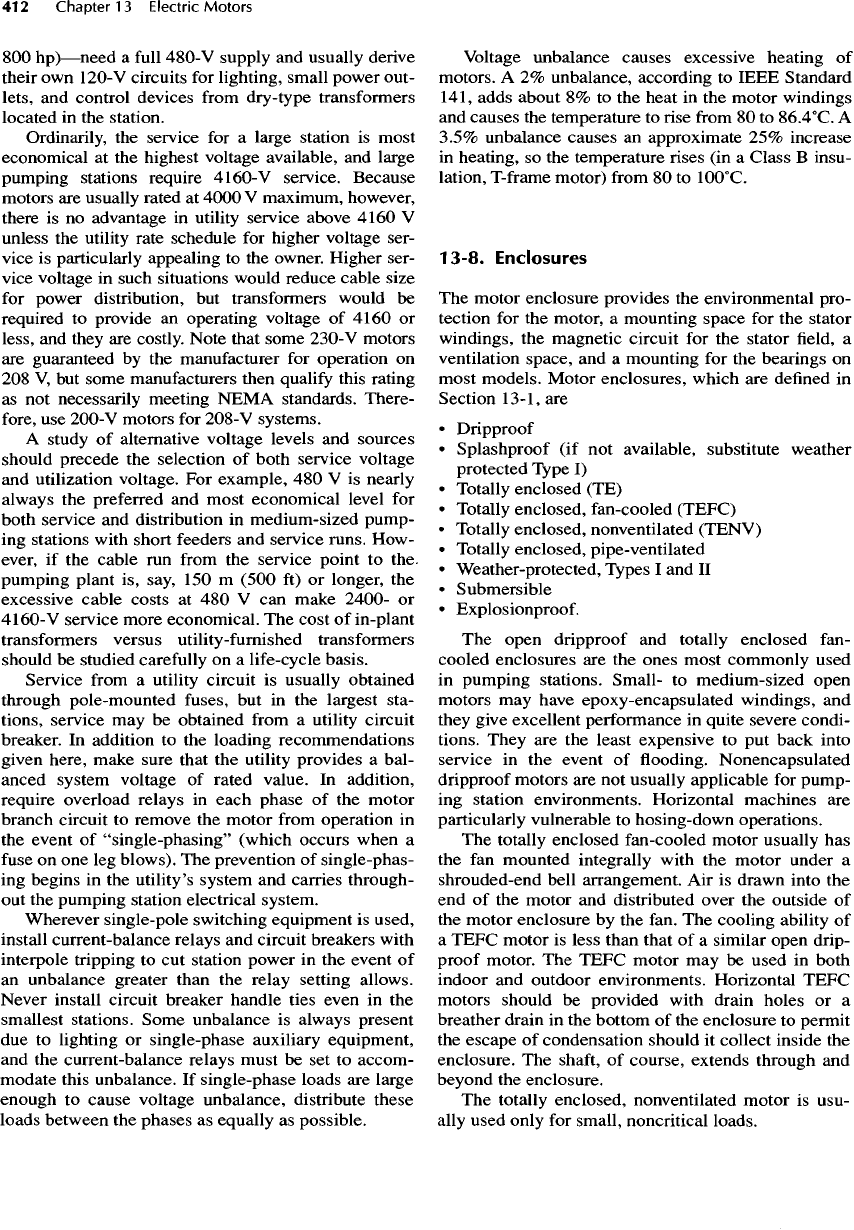
800
hp)
—
need
a
full
480-V supply
and
usually derive
their
own
1
20-
V
circuits
for
lighting, small power out-
lets,
and
control devices
from
dry-type transformers
located
in the
station.
Ordinarily,
the
service
for a
large station
is
most
economical
at the
highest voltage available,
and
large
pumping
stations require
4
160-
V
service. Because
motors
are
usually rated
at
4000
V
maximum, however,
there
is no
advantage
in
utility service above 4160
V
unless
the
utility
rate schedule
for
higher voltage ser-
vice
is
particularly appealing
to the
owner. Higher ser-
vice voltage
in
such situations would reduce cable size
for
power distribution,
but
transformers would
be
required
to
provide
an
operating voltage
of
4160
or
less,
and
they
are
costly. Note that some 230-V motors
are
guaranteed
by the
manufacturer
for
operation
on
208 V, but
some manufacturers then
qualify
this rating
as
not
necessarily meeting NEMA standards.
There-
fore,
use
200-V motors
for
208-V systems.
A
study
of
alternative voltage levels
and
sources
should precede
the
selection
of
both service voltage
and
utilization voltage.
For
example,
480 V is
nearly
always
the
preferred
and
most economical level
for
both service
and
distribution
in
medium-sized pump-
ing
stations
with
short feeders
and
service runs. How-
ever,
if the
cable
run
from
the
service point
to
the-
pumping
plant
is,
say,
15Om
(500
ft) or
longer,
the
excessive cable costs
at 480 V can
make
2400-
or
4
160-
V
service more economical.
The
cost
of
in-plant
transformers
versus utility-furnished transformers
should
be
studied
carefully
on a
life-cycle basis.
Service
from
a
utility circuit
is
usually obtained
through pole-mounted
fuses,
but in the
largest sta-
tions, service
may be
obtained
from
a
utility circuit
breaker.
In
addition
to the
loading recommendations
given
here, make sure that
the
utility provides
a
bal-
anced system voltage
of
rated value.
In
addition,
require overload relays
in
each phase
of the
motor
branch circuit
to
remove
the
motor
from
operation
in
the
event
of
"single-phasing" (which occurs when
a
fuse
on one leg
blows).
The
prevention
of
single
-phas-
ing
begins
in the
utility's system
and
carries
through-
out
the
pumping station electrical system.
Wherever single-pole switching equipment
is
used,
install current-balance relays
and
circuit breakers with
interpole
tripping
to cut
station power
in the
event
of
an
unbalance greater than
the
relay setting allows.
Never
install circuit breaker handle ties even
in the
smallest stations. Some unbalance
is
always present
due
to
lighting
or
single-phase auxiliary equipment,
and
the
current-balance relays must
be set to
accom-
modate this unbalance.
If
single-phase loads
are
large
enough
to
cause voltage unbalance, distribute these
loads between
the
phases
as
equally
as
possible.
Voltage
unbalance causes excessive heating
of
motors.
A 2%
unbalance, according
to
IEEE
Standard
141,
adds about
8% to the
heat
in the
motor windings
and
causes
the
temperature
to rise
from
80 to
86.4
0
C.
A
3.5% unbalance causes
an
approximate
25%
increase
in
heating,
so the
temperature
rises (in a
Class
B
insu-
lation,
T-frame
motor)
from
80 to
10O
0
C.
13-8.
Enclosures
The
motor enclosure provides
the
environmental pro-
tection
for the
motor,
a
mounting space
for the
stator
windings,
the
magnetic circuit
for the
stator
field, a
ventilation space,
and a
mounting
for the
bearings
on
most models. Motor enclosures, which
are
defined
in
Section
13-1,
are
•
Dripproof
•
Splashproof
(if not
available, substitute weather
protected
Type
I)
•
Totally enclosed (TE)
•
Totally enclosed, fan-cooled (TEFC)
•
Totally enclosed, nonventilated (TENV)
•
Totally enclosed, pipe-ventilated
•
Weather-protected, Types
I and II
•
Submersible
•
Explosionproof.
The
open dripproof
and
totally
enclosed
fan-
cooled
enclosures
are the
ones most commonly used
in
pumping stations. Small-
to
medium-sized open
motors
may
have
epoxy-encapsulated
windings,
and
they
give excellent performance
in
quite severe condi-
tions. They
are the
least expensive
to put
back into
service
in the
event
of flooding.
Nonencapsulated
dripproof motors
are not
usually applicable
for
pump-
ing
station environments. Horizontal machines
are
particularly vulnerable
to
hosing-down operations.
The
totally
enclosed
fan-cooled motor usually
has
the fan
mounted integrally with
the
motor under
a
shrouded-end
bell
arrangement.
Air is
drawn into
the
end of the
motor
and
distributed over
the
outside
of
the
motor enclosure
by the
fan.
The
cooling ability
of
a
TEFC
motor
is
less than that
of a
similar open drip-
proof motor.
The
TEFC
motor
may be
used
in
both
indoor
and
outdoor environments. Horizontal
TEFC
motors should
be
provided with drain holes
or a
breather drain
in the
bottom
of the
enclosure
to
permit
the
escape
of
condensation should
it
collect inside
the
enclosure.
The
shaft,
of
course, extends through
and
beyond
the
enclosure.
The
totally enclosed, nonventilated motor
is
usu-
ally
used only
for
small, noncritical loads.