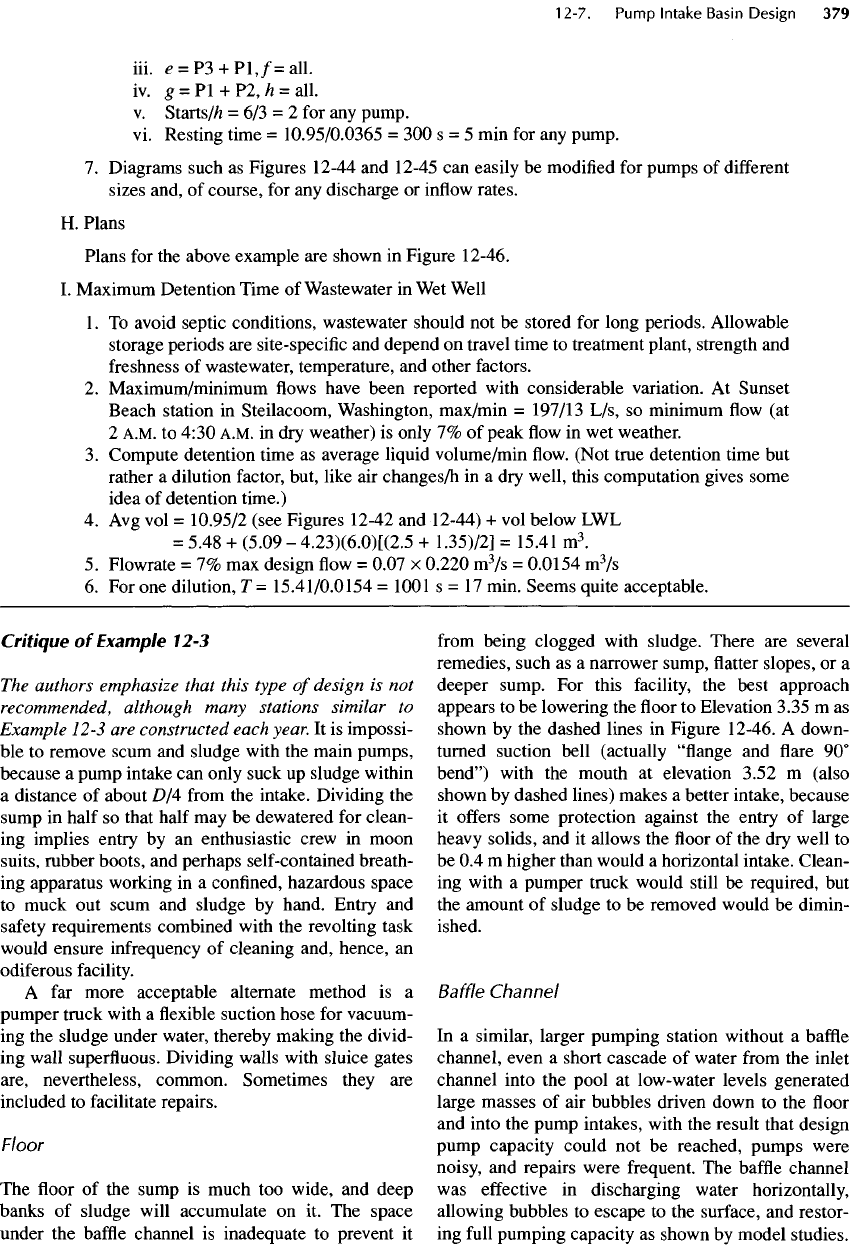
Critique
of
Example
12-3
The
authors emphasize that this
type
of
design
is not
recommended,
although many stations similar
to
Example
12-3
are
constructed each year.
It is
impossi-
ble to
remove scum
and
sludge with
the
main pumps,
because
a
pump intake
can
only suck
up
sludge within
a
distance
of
about
D/4
from
the
intake. Dividing
the
sump
in
half
so
that half
may be
dewatered
for
clean-
ing
implies entry
by an
enthusiastic crew
in
moon
suits,
rubber boots,
and
perhaps self-contained breath-
ing
apparatus working
in a
confined, hazardous space
to
muck
out
scum
and
sludge
by
hand. Entry
and
safety
requirements combined with
the
revolting task
would
ensure
infrequency
of
cleaning and, hence,
an
odiferous
facility.
A
far
more acceptable alternate method
is a
pumper truck with
a flexible
suction hose
for
vacuum-
ing
the
sludge under water, thereby making
the
divid-
ing
wall
superfluous.
Dividing walls with sluice gates
are, nevertheless, common. Sometimes they
are
included
to
facilitate repairs.
Floor
The floor of the
sump
is
much
too
wide,
and
deep
banks
of
sludge will accumulate
on it. The
space
under
the
baffle
channel
is
inadequate
to
prevent
it
from
being clogged with sludge. There
are
several
remedies, such
as a
narrower sump,
flatter
slopes,
or a
deeper sump.
For
this facility,
the
best approach
appears
to be
lowering
the floor to
Elevation 3.35
m as
shown
by the
dashed
lines
in
Figure
12-46.
A
down-
turned
suction bell (actually "flange
and flare 90°
bend")
with
the
mouth
at
elevation 3.52
m
(also
shown
by
dashed lines) makes
a
better intake, because
it
offers
some protection against
the
entry
of
large
heavy
solids,
and it
allows
the floor of the dry
well
to
be 0.4 m
higher than would
a
horizontal intake. Clean-
ing
with
a
pumper truck would still
be
required,
but
the
amount
of
sludge
to be
removed would
be
dimin-
ished.
Baffle
Channel
In a
similar, larger pumping station without
a
baffle
channel, even
a
short cascade
of
water
from
the
inlet
channel into
the
pool
at
low-water levels generated
large masses
of air
bubbles driven down
to the floor
and
into
the
pump intakes, with
the
result that design
pump capacity could
not be
reached, pumps were
noisy,
and
repairs were frequent.
The
baffle
channel
was
effective
in
discharging water horizontally,
allowing bubbles
to
escape
to the
surface,
and
restor-
ing
full
pumping capacity
as
shown
by
model studies.
iii.
e
= P3 +
Pl,/=all.
iv.
£
= Pl +
P2,/i
=
all.
v.
Starts//*
= 6/3 = 2 for any
pump.
vi.
Resting time
=
10.95/0.0365
= 300 s = 5
min
for any
pump.
7.
Diagrams such
as
Figures
12-44
and
12-45
can
easily
be
modified
for
pumps
of
different
sizes and,
of
course,
for any
discharge
or
inflow
rates.
H.
Plans
Plans
for the
above example
are
shown
in
Figure 12-46.
I.
Maximum Detention Time
of
Wastewater
in Wet
Well
1.
To
avoid septic conditions, wastewater should
not be
stored
for
long periods. Allowable
storage
periods
are
site-specific
and
depend
on
travel time
to
treatment plant, strength
and
freshness
of
wastewater, temperature,
and
other factors.
2.
Maximum/minimum
flows
have been reported with considerable variation.
At
Sunset
Beach station
in
Steilacoom, Washington, max/min
=
197/13
L/s,
so
minimum
flow (at
2
A.M.
to
4:30
A.M.
in dry
weather)
is
only
7% of
peak
flow in wet
weather.
3.
Compute detention time
as
average liquid
volume/min
flow.
(Not true detention time
but
rather
a
dilution
factor,
but, like
air
changes/h
in a dry
well, this computation gives some
idea
of
detention time.)
4. Avg
vol
=
10.95/2
(see Figures 12-42
and
12-44)
+
vol
below
LWL
=
5.48
+
(5.09
-
4.23)(6.0)[(2.5
+
1.35)/2]
=
15.41
m
3
.
5.
Flowrate
= 7% max
design
flow =
0.07
x
0.220
m
3
/s
=
0.0154
m
3
/s
6.
For one
dilution,
T=
15.41/0.0154
=
1001
s = 17
min. Seems quite acceptable.