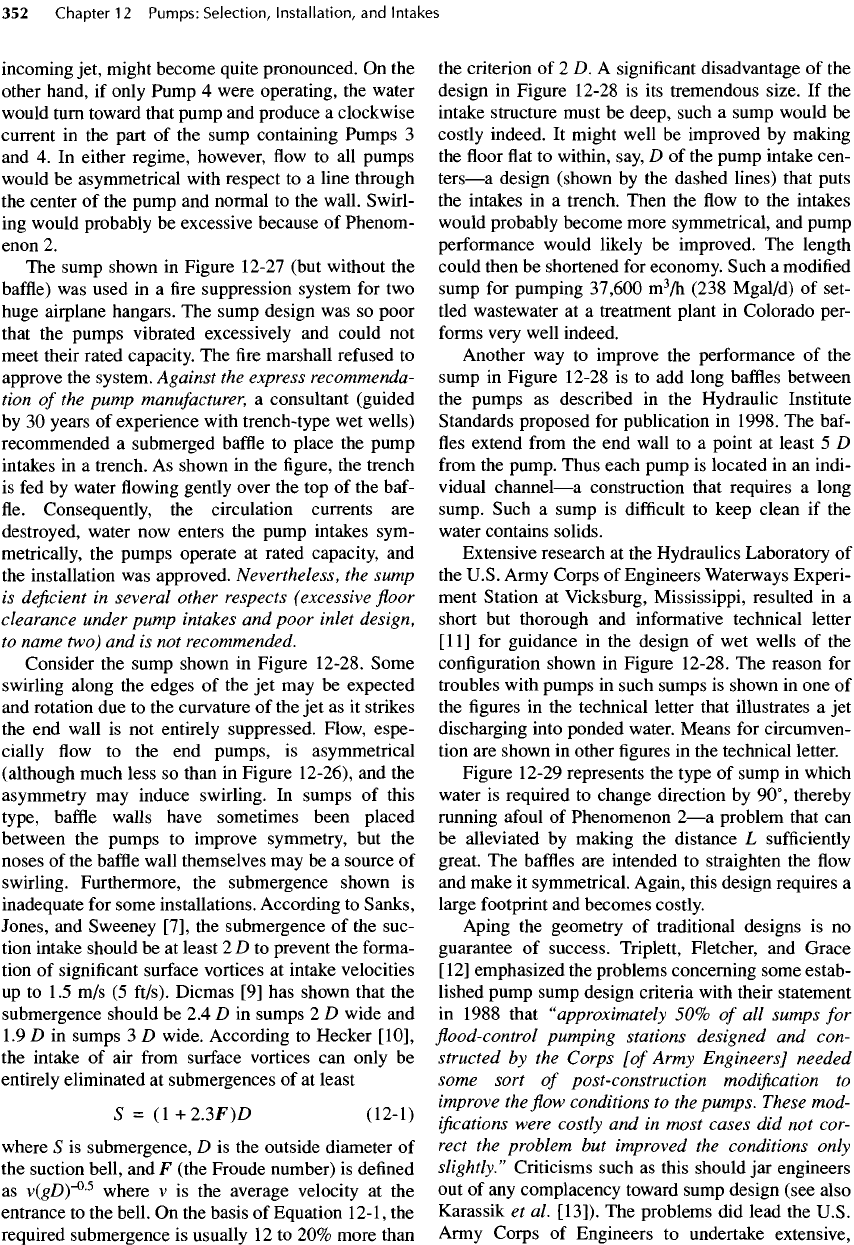
incoming jet, might become quite pronounced.
On the
other hand,
if
only Pump
4
were operating,
the
water
would
turn toward that pump
and
produce
a
clockwise
current
in the
part
of the
sump containing Pumps
3
and
4. In
either regime, however,
flow to all
pumps
would
be
asymmetrical
with
respect
to a
line through
the
center
of the
pump
and
normal
to the
wall. Swirl-
ing
would probably
be
excessive because
of
Phenom-
enon
2.
The
sump shown
in
Figure
12-27
(but without
the
baffle)
was
used
in a fire
suppression system
for two
huge
airplane hangars.
The
sump design
was so
poor
that
the
pumps vibrated excessively
and
could
not
meet their rated capacity.
The fire
marshall refused
to
approve
the
system. Against
the
express
recommenda-
tion
of the
pump
manufacturer,
a
consultant (guided
by
30
years
of
experience with trench-type
wet
wells)
recommended
a
submerged
baffle
to
place
the
pump
intakes
in a
trench.
As
shown
in the figure, the
trench
is
fed by
water
flowing
gently over
the top of the
baf-
fle.
Consequently,
the
circulation currents
are
destroyed, water
now
enters
the
pump intakes sym-
metrically,
the
pumps operate
at
rated capacity,
and
the
installation
was
approved.
Nevertheless,
the
sump
is
deficient
in
several other
respects
(excessive
floor
clearance under pump intakes
and
poor
inlet design,
to
name two)
and is not
recommended.
Consider
the
sump shown
in
Figure 12-28. Some
swirling along
the
edges
of the jet may be
expected
and
rotation
due to the
curvature
of the jet as it
strikes
the
end
wall
is not
entirely suppressed. Flow, espe-
cially
flow to the end
pumps,
is
asymmetrical
(although much less
so
than
in
Figure 12-26),
and the
asymmetry
may
induce swirling.
In
sumps
of
this
type,
baffle
walls have sometimes been placed
between
the
pumps
to
improve symmetry,
but the
noses
of the
baffle
wall themselves
may be a
source
of
swirling.
Furthermore,
the
submergence shown
is
inadequate
for
some installations. According
to
Sanks,
Jones,
and
Sweeney [7],
the
submergence
of the
suc-
tion
intake should
be at
least
2 D to
prevent
the
forma-
tion
of
significant
surface vortices
at
intake velocities
up
to
1.5
m/s (5
ft/s).
Dicmas
[9] has
shown that
the
submergence should
be 2.4 D in
sumps
2 D
wide
and
1.9
D in
sumps
3 D
wide. According
to
Hecker
[10],
the
intake
of air
from
surface vortices
can
only
be
entirely eliminated
at
submergences
of at
least
S
=
(1+2.3F)D
(12-1)
where
S is
submergence,
D is the
outside diameter
of
the
suction bell,
and F
(the Froude number)
is
defined
as
v(gZ))~°
5
where
v is the
average
velocity
at the
entrance
to the
bell.
On the
basis
of
Equation
12-1,
the
required submergence
is
usually
12 to 20%
more than
the
criterion
of 2 Z). A
significant
disadvantage
of the
design
in
Figure 12-28
is its
tremendous size.
If the
intake structure must
be
deep,
such
a
sump would
be
costly indeed.
It
might well
be
improved
by
making
the floor flat to
within, say,
D of the
pump intake cen-
ters
—
a
design (shown
by the
dashed lines) that puts
the
intakes
in a
trench. Then
the flow to the
intakes
would probably become more symmetrical,
and
pump
performance would likely
be
improved.
The
length
could then
be
shortened
for
economy. Such
a
modified
sump
for
pumping
37,600
m
3
/h
(238
Mgal/d)
of
set-
tled wastewater
at a
treatment plant
in
Colorado per-
forms
very well indeed.
Another
way to
improve
the
performance
of the
sump
in
Figure 12-28
is to add
long
baffles
between
the
pumps
as
described
in the
Hydraulic Institute
Standards proposed
for
publication
in
1998.
The
baf-
fles
extend
from
the end
wall
to a
point
at
least
5 D
from
the
pump. Thus each pump
is
located
in an
indi-
vidual
channel
—
a
construction that requires
a
long
sump.
Such
a
sump
is
difficult
to
keep clean
if the
water contains solids.
Extensive research
at the
Hydraulics Laboratory
of
the
U.S.
Army Corps
of
Engineers Waterways Experi-
ment Station
at
Vicksburg,
Mississippi,
resulted
in a
short
but
thorough
and
informative technical letter
[11]
for
guidance
in the
design
of wet
wells
of the
configuration
shown
in
Figure 12-28.
The
reason
for
troubles with pumps
in
such sumps
is
shown
in one of
the
figures in the
technical
letter
that
illustrates
a jet
discharging into ponded water. Means
for
circumven-
tion
are
shown
in
other
figures in the
technical letter.
Figure 12-29 represents
the
type
of
sump
in
which
water
is
required
to
change direction
by
90°, thereby
running
afoul
of
Phenomenon
2
—
a
problem that
can
be
alleviated
by
making
the
distance
L
sufficiently
great.
The
baffles
are
intended
to
straighten
the flow
and
make
it
symmetrical. Again, this design requires
a
large footprint
and
becomes
costly.
Aping
the
geometry
of
traditional designs
is no
guarantee
of
success. Triplett, Fletcher,
and
Grace
[12] emphasized
the
problems concerning some estab-
lished pump sump design criteria with their statement
in
1988 that
"approximately
50% of all
sumps
for
flood-control
pumping stations designed
and
con-
structed
by the
Corps
[of
Army Engineers] needed
some sort
of
post-
construction
modification
to
improve
the flow
conditions
to the
pumps.
These
mod-
ifications
were
costly
and in
most cases
did not
cor-
rect
the
problem
but
improved
the
conditions
only
slightly."
Criticisms such
as
this should
jar
engineers
out
of any
complacency
toward sump
design
(see
also
Karassik
et
al
[13]).
The
problems
did
lead
the
U.S.
Army Corps
of
Engineers
to
undertake extensive,