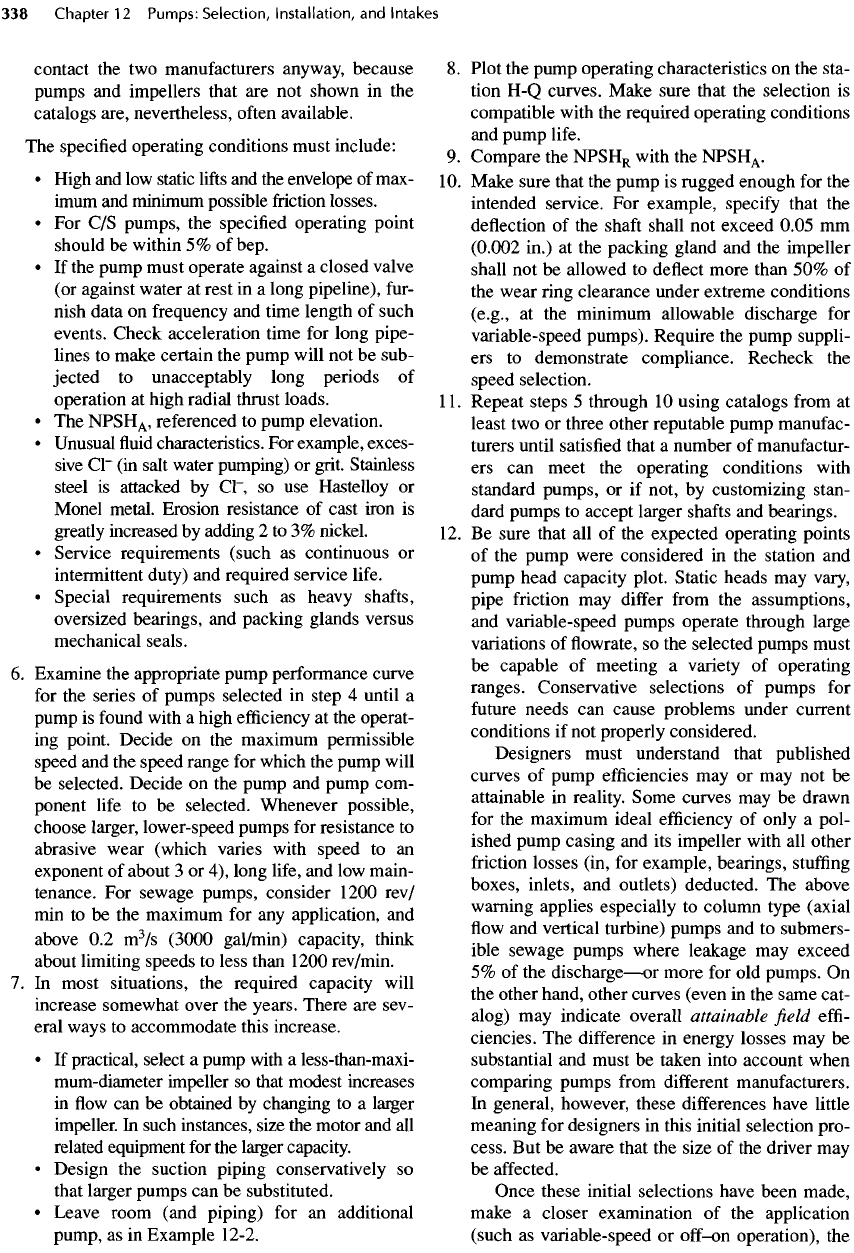
contact
the two
manufacturers anyway, because
pumps
and
impellers that
are not
shown
in the
catalogs are, nevertheless, often available.
The
specified operating conditions must include:
•
High
and low
static
lifts
and the
envelope
of
max-
imum
and
minimum possible
friction
losses.
• For C/S
pumps,
the
specified operating point
should
be
within
5% of
bep.
• If the
pump must operate against
a
closed valve
(or
against water
at
rest
in a
long pipeline), fur-
nish
data
on
frequency
and
time length
of
such
events. Check acceleration time
for
long pipe-
lines
to
make certain
the
pump will
not be
sub-
jected
to
unacceptably long periods
of
operation
at
high radial thrust loads.
• The
NPSH
A
,
referenced
to
pump elevation.
•
Unusual
fluid
characteristics.
For
example, exces-
sive
Cl~ (in
salt water pumping)
or
grit. Stainless
steel
is
attacked
by
Cl~,
so use
Hastelloy
or
Monel
metal. Erosion resistance
of
cast iron
is
greatly
increased
by
adding
2 to 3%
nickel.
•
Service requirements (such
as
continuous
or
intermittent duty)
and
required service
life.
•
Special requirements such
as
heavy
shafts,
oversized bearings,
and
packing glands versus
mechanical seals.
6.
Examine
the
appropriate pump performance curve
for
the
series
of
pumps selected
in
step
4
until
a
pump
is
found
with
a
high
efficiency
at the
operat-
ing
point. Decide
on the
maximum permissible
speed
and the
speed range
for
which
the
pump will
be
selected. Decide
on the
pump
and
pump com-
ponent
life
to be
selected. Whenever possible,
choose larger, lower-speed pumps
for
resistance
to
abrasive wear (which varies with speed
to an
exponent
of
about
3 or 4),
long
life,
and low
main-
tenance.
For
sewage pumps, consider 1200 rev/
min
to be the
maximum
for any
application,
and
above
0.2
m
3
/s
(3000
gal/min)
capacity, think
about limiting speeds
to
less than
1200
rev/min.
7. In
most situations,
the
required capacity will
increase somewhat over
the
years. There
are
sev-
eral ways
to
accommodate this increase.
• If
practical, select
a
pump
with
a
less-than-maxi-
mum-diameter
impeller
so
that modest increases
in
flow can be
obtained
by
changing
to a
larger
impeller.
In
such instances, size
the
motor
and all
related equipment
for the
larger capacity.
•
Design
the
suction piping conservatively
so
that
larger pumps
can be
substituted.
•
Leave room (and piping)
for an
additional
pump,
as in
Example 12-2.
8.
Plot
the
pump operating characteristics
on the
sta-
tion
H-Q
curves. Make sure that
the
selection
is
compatible with
the
required
operating conditions
and
pump life.
9.
Compare
the
NPSH
R
with
the
NPSH
A
.
10.
Make sure that
the
pump
is
rugged enough
for the
intended service.
For
example,
specify
that
the
deflection
of the
shaft
shall
not
exceed 0.05
mm
(0.002
in.)
at the
packing gland
and the
impeller
shall
not be
allowed
to
deflect
more than
50% of
the
wear ring clearance under extreme conditions
(e.g.,
at the
minimum allowable discharge
for
variable-speed pumps). Require
the
pump suppli-
ers
to
demonstrate compliance. Recheck
the
speed selection.
11.
Repeat steps
5
through
10
using catalogs
from
at
least
two or
three
other reputable pump manufac-
turers until
satisfied
that
a
number
of
manufactur-
ers can
meet
the
operating conditions with
standard pumps,
or if
not,
by
customizing stan-
dard pumps
to
accept larger
shafts
and
bearings.
12.
Be
sure that
all of the
expected operating points
of
the
pump were considered
in the
station
and
pump head capacity plot. Static heads
may
vary,
pipe
friction
may
differ
from
the
assumptions,
and
variable-
speed
pumps operate through large
variations
of flowrate, so the
selected pumps must
be
capable
of
meeting
a
variety
of
operating
ranges. Conservative selections
of
pumps
for
future
needs
can
cause problems under current
conditions
if not
properly
considered.
Designers must understand that published
curves
of
pump
efficiencies
may or may not be
attainable
in
reality. Some curves
may be
drawn
for
the
maximum ideal
efficiency
of
only
a
pol-
ished pump casing
and its
impeller with
all
other
friction
losses (in,
for
example, bearings,
stuffing
boxes, inlets,
and
outlets) deducted.
The
above
warning applies especially
to
column type (axial
flow
and
vertical turbine) pumps
and to
submers-
ible sewage pumps where leakage
may
exceed
5%
of the
discharge
—
or
more
for old
pumps.
On
the
other hand, other curves (even
in the
same cat-
alog)
may
indicate overall attainable
field
effi-
ciencies.
The
difference
in
energy losses
may be
substantial
and
must
be
taken into account when
comparing pumps
from
different
manufacturers.
In
general, however, these
differences
have little
meaning
for
designers
in
this initial selection pro-
cess.
But be
aware that
the
size
of the
driver
may
be
affected.
Once these initial selections have been made,
make
a
closer examination
of the
application
(such
as
variable-speed
or
off-on
operation),
the