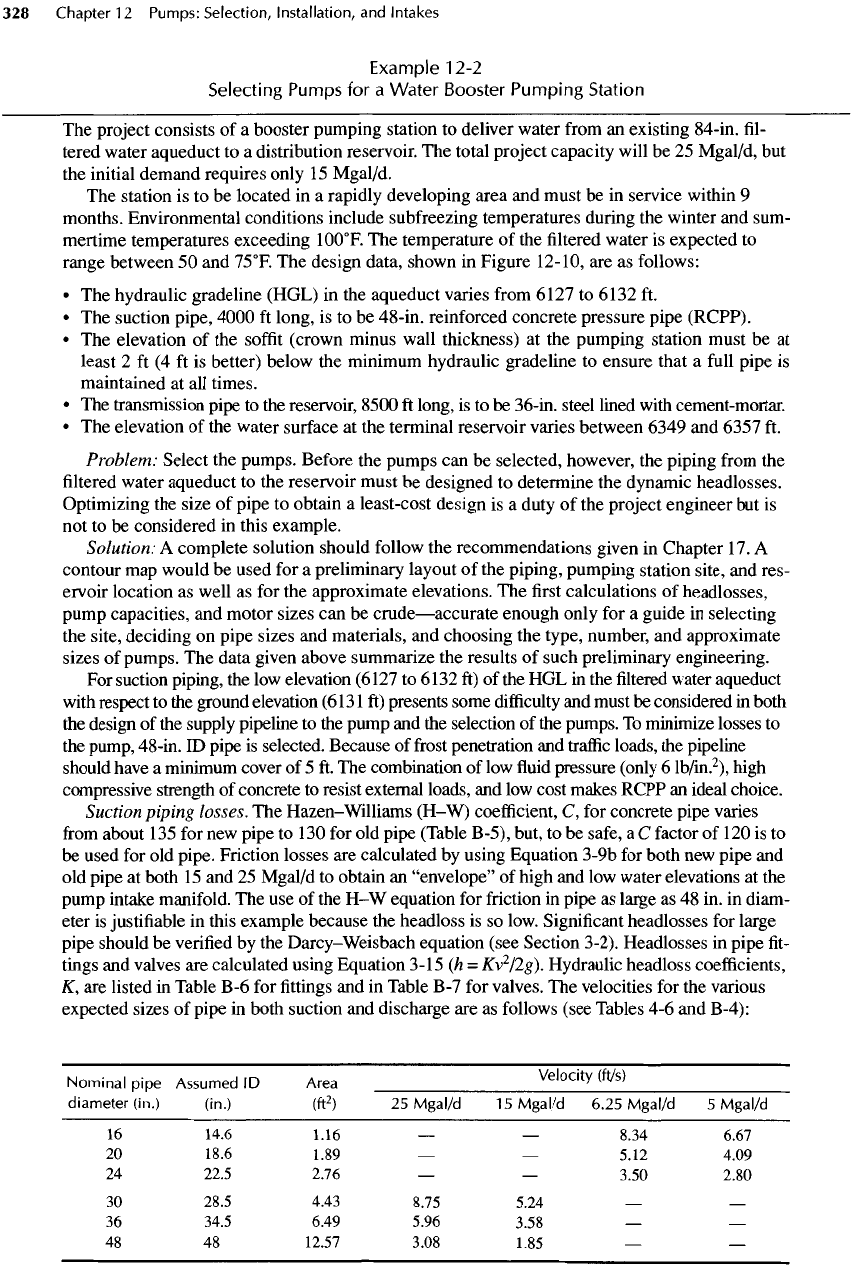
Example
12-2
Selecting
Pumps
for a
Water Booster Pumping Station
The
project consists
of a
booster pumping station
to
deliver water
from
an
existing 84-in.
fil-
tered water aqueduct
to a
distribution reservoir.
The
total project capacity will
be 25
Mgal/d,
but
the
initial demand requires only
15
Mgal/d.
The
station
is to be
located
in a
rapidly developing area
and
must
be in
service within
9
months. Environmental
conditions
include subfreezing temperatures during
the
winter
and
sum-
mertime temperatures exceeding
10O
0
F.
The
temperature
of the filtered
water
is
expected
to
range
between
50 and
75
0
F.
The
design data, shown
in
Figure
12-10,
are as
follows:
• The
hydraulic gradeline (HGL)
in the
aqueduct varies
from
6121
to
6132
ft.
• The
suction pipe,
4000
ft
long,
is to be
48-in. reinforced concrete pressure pipe (RCPP).
• The
elevation
of the
soffit
(crown minus wall thickness)
at the
pumping station must
be at
least
2 ft (4 ft is
better)
below
the
minimum hydraulic
gradeline
to
ensure that
a
full
pipe
is
maintained
at all
times.
• The
transmission pipe
to the
reservoir,
8500
ft
long,
is to be
36-in.
steel lined with cement-mortar.
• The
elevation
of the
water surface
at the
terminal reservoir varies between 6349
and
6357
ft.
Problem: Select
the
pumps. Before
the
pumps
can be
selected, however,
the
piping
from
the
filtered
water
aqueduct
to the
reservoir must
be
designed
to
determine
the
dynamic headlosses.
Optimizing
the
size
of
pipe
to
obtain
a
least-cost design
is a
duty
of the
project engineer
but is
not
to be
considered
in
this example.
Solution:
A
complete solution should follow
the
recommendations given
in
Chapter
17.
A
contour
map
would
be
used
for a
preliminary layout
of the
piping, pumping station site,
and
res-
ervoir location
as
well
as for the
approximate elevations.
The first
calculations
of
headlosses,
pump
capacities,
and
motor sizes
can be
crude—accurate
enough only
for a
guide
in
selecting
the
site, deciding
on
pipe sizes
and
materials,
and
choosing
the
type, number,
and
approximate
sizes
of
pumps.
The
data given above summarize
the
results
of
such preliminary engineering.
For
suction piping,
the low
elevation (6127
to
6132
ft) of the HGL in the filtered
water aqueduct
with
respect
to the
ground elevation
(6131
ft)
presents some
difficulty
and
must
be
considered
in
both
the
design
of the
supply pipeline
to the
pump
and the
selection
of the
pumps.
To
minimize losses
to
the
pump, 48-in.
ID
pipe
is
selected. Because
of frost
penetration
and
traffic
loads,
the
pipeline
should
have
a
minimum cover
of 5 ft. The
combination
of low fluid
pressure (only
6
lb/in.
2
),
high
compressive strength
of
concrete
to
resist external loads,
and low
cost makes RCPP
an
ideal choice.
Suction
piping losses.
The
Hazen-Williams
(H-W)
coefficient,
C, for
concrete
pipe
varies
from
about
135 for new
pipe
to
130
for old
pipe (Table B-5), but,
to be
safe,
a C
factor
of 120 is to
be
used
for old
pipe.
Friction
losses
are
calculated
by
using Equation
3-9b
for
both
new
pipe
and
old
pipe
at
both
15 and 25
Mgal/d
to
obtain
an
"envelope"
of
high
and low
water elevations
at the
pump
intake manifold.
The use of the H-W
equation
for
friction
in
pipe
as
large
as 48 in. in
diam-
eter
is
justifiable
in
this example because
the
headloss
is so
low. Significant headlosses
for
large
pipe should
be
verified
by the
Darcy-Weisbach equation
(see
Section 3-2). Headlosses
in
pipe
fit-
tings
and
valves
are
calculated using Equation
3-15
(h =
Kv
2
/2g).
Hydraulic headloss coefficients,
K,
are
listed
in
Table
B-6
for fittings and in
Table
B-7
for
valves.
The
velocities
for the
various
expected sizes
of
pipe
in
both suction
and
discharge
are as
follows (see Tables
4-6 and
B-4):
Nominal
pipe
Assumed
ID
A?!Velocity
(ft/s)
diameter
(in.)
(in.)
(ft
2
)
25
Mgal/d
15
Mgal/d 6.25 Mgal/d
5
Mgal/d
16
14.6 1.16
— —
8.34 6.67
20
18.6 1.89
— —
5.12 4.09
24
22.5 2.76
— —
3.50 2.80
30
28.5 4.43 8.75 5.24
— —
36
34.5 6.49 5.96 3.58
— —
48
48
12.57 3.08 1.85
— —