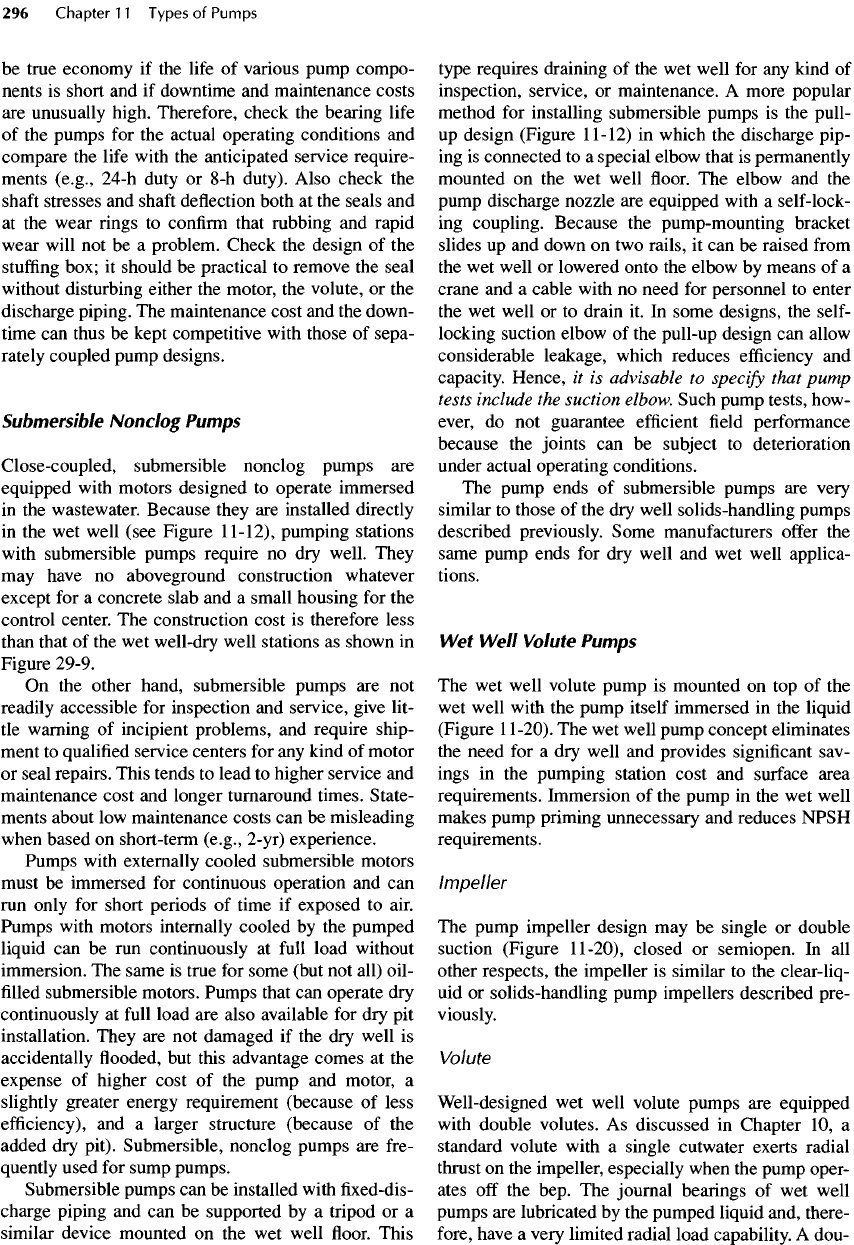
be
true economy
if the
life
of
various pump compo-
nents
is
short
and if
downtime
and
maintenance costs
are
unusually
high. Therefore, check
the
bearing
life
of
the
pumps
for the
actual operating conditions
and
compare
the
life
with
the
anticipated service require-
ments
(e.g., 24-h
duty
or 8-h
duty). Also check
the
shaft
stresses
and
shaft
deflection
both
at the
seals
and
at
the
wear rings
to
confirm
that rubbing
and
rapid
wear
will
not be a
problem. Check
the
design
of the
stuffing
box;
it
should
be
practical
to
remove
the
seal
without
disturbing either
the
motor,
the
volute,
or the
discharge piping.
The
maintenance cost
and the
down-
time
can
thus
be
kept competitive
with
those
of
sepa-
rately
coupled pump designs.
Submersible
Nonclog
Pumps
Close-coupled, submersible nonclog pumps
are
equipped
with
motors designed
to
operate immersed
in
the
wastewater. Because they
are
installed directly
in
the wet
well (see Figure
11-12),
pumping stations
with
submersible pumps require
no dry
well. They
may
have
no
aboveground construction whatever
except
for a
concrete slab
and a
small housing
for the
control center.
The
construction cost
is
therefore less
than
that
of the wet
well-dry well stations
as
shown
in
Figure 29-9.
On
the
other hand, submersible pumps
are not
readily accessible
for
inspection
and
service, give lit-
tle
warning
of
incipient problems,
and
require ship-
ment
to
qualified
service centers
for any
kind
of
motor
or
seal repairs. This tends
to
lead
to
higher service
and
maintenance
cost
and
longer turnaround times. State-
ments
about
low
maintenance costs
can be
misleading
when
based
on
short-term (e.g., 2-yr) experience.
Pumps
with
externally cooled submersible motors
must
be
immersed
for
continuous operation
and can
run
only
for
short periods
of
time
if
exposed
to
air.
Pumps
with
motors internally cooled
by the
pumped
liquid
can be run
continuously
at
full
load without
immersion.
The
same
is
true
for
some (but
not
all) oil-
filled
submersible motors. Pumps that
can
operate
dry
continuously
at
full
load
are
also available
for dry pit
installation. They
are not
damaged
if the dry
well
is
accidentally
flooded, but
this advantage comes
at the
expense
of
higher cost
of the
pump
and
motor,
a
slightly
greater energy requirement (because
of
less
efficiency),
and a
larger structure (because
of the
added
dry
pit). Submersible, nonclog pumps
are
fre-
quently
used
for
sump pumps.
Submersible pumps
can be
installed with
fixed-dis-
charge piping
and can be
supported
by a
tripod
or a
similar device mounted
on the wet
well
floor.
This
type
requires draining
of the wet
well
for any
kind
of
inspection, service,
or
maintenance.
A
more popular
method
for
installing submersible pumps
is the
pull-
up
design (Figure
11-12)
in
which
the
discharge pip-
ing
is
connected
to a
special
elbow that
is
permanently
mounted
on the wet
well
floor. The
elbow
and the
pump
discharge nozzle
are
equipped with
a
self-lock-
ing
coupling. Because
the
pump-mounting bracket
slides
up and
down
on two
rails,
it can be
raised
from
the wet
well
or
lowered onto
the
elbow
by
means
of a
crane
and a
cable with
no
need
for
personnel
to
enter
the
wet
well
or to
drain
it. In
some designs,
the
self-
locking suction elbow
of the
pull-up design
can
allow
considerable leakage, which reduces
efficiency
and
capacity. Hence,
it is
advisable
to
specify
that pump
tests
include
the
suction elbow. Such pump tests, how-
ever,
do not
guarantee
efficient
field
performance
because
the
joints
can be
subject
to
deterioration
under actual operating conditions.
The
pump ends
of
submersible pumps
are
very
similar
to
those
of the dry
well solids-handling pumps
described
previously. Some manufacturers
offer
the
same pump ends
for dry
well
and wet
well applica-
tions.
Wet
Well
Volute
Pumps
The wet
well volute pump
is
mounted
on top of the
wet
well with
the
pump itself immersed
in the
liquid
(Figure
1
1-20).
The wet
well pump concept eliminates
the
need
for a dry
well
and
provides
significant
sav-
ings
in the
pumping station cost
and
surface area
requirements. Immersion
of the
pump
in the wet
well
makes pump priming unnecessary
and
reduces NPSH
requirements.
Impeller
The
pump impeller design
may be
single
or
double
suction (Figure
11-20),
closed
or
semiopen.
In all
other respects,
the
impeller
is
similar
to the
clear-liq-
uid
or
solids-handling pump impellers described pre-
viously.
Volute
Well-designed
wet
well volute pumps
are
equipped
with
double volutes.
As
discussed
in
Chapter
10, a
standard volute with
a
single cutwater exerts radial
thrust
on the
impeller, especially when
the
pump oper-
ates
off the
bep.
The
journal bearings
of wet
well
pumps
are
lubricated
by the
pumped liquid and, there-
fore,
have
a
very limited radial load capability.
A
dou-