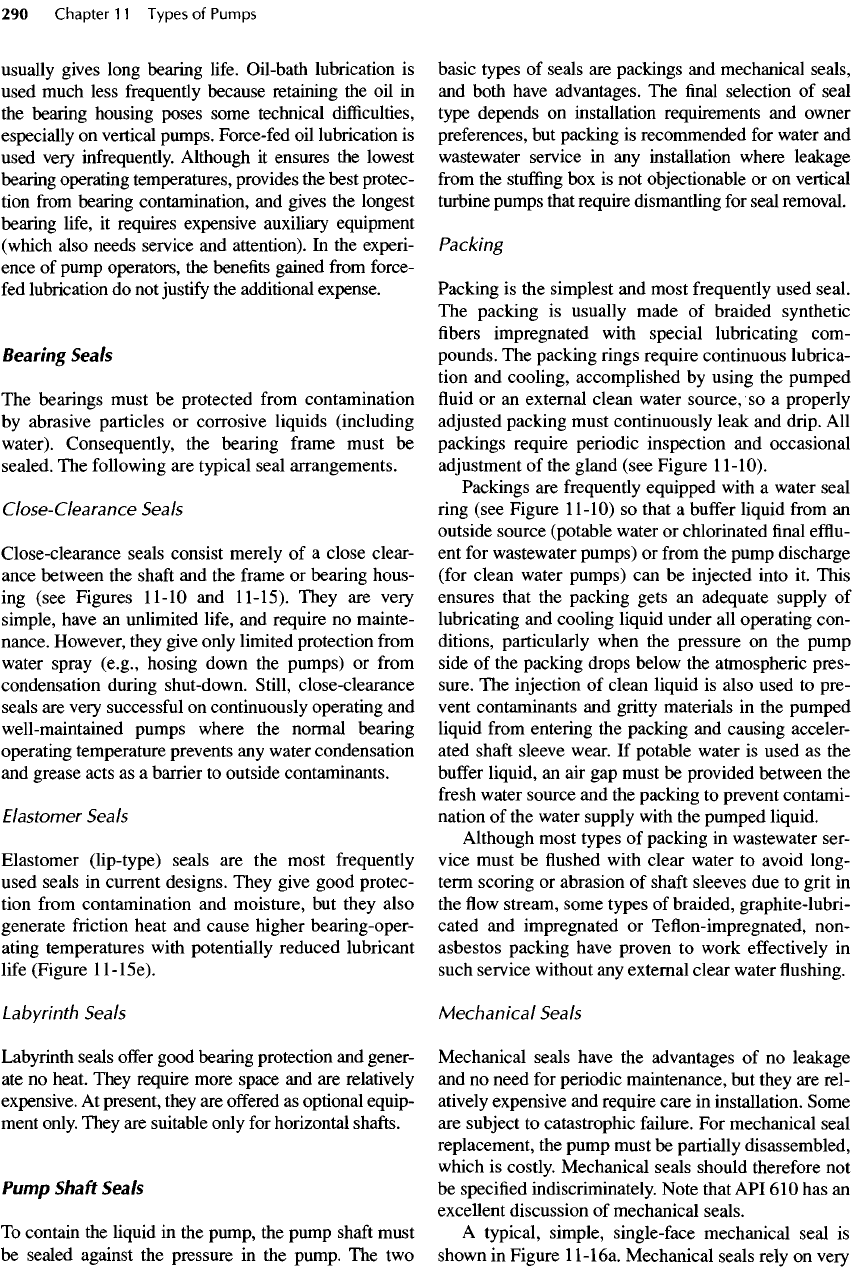
usually
gives long bearing
life.
Oil-bath lubrication
is
used
much less
frequently
because retaining
the oil in
the
bearing housing poses some technical
difficulties,
especially
on
vertical pumps. Force-fed
oil
lubrication
is
used
very
infrequently.
Although
it
ensures
the
lowest
bearing operating temperatures, provides
the
best protec-
tion
from
bearing contamination,
and
gives
the
longest
bearing
life,
it
requires expensive auxiliary equipment
(which
also needs service
and
attention).
In the
experi-
ence
of
pump operators,
the
benefits
gained
from
force-
fed
lubrication
do not
justify
the
additional expense.
Bearing Seals
The
bearings must
be
protected
from
contamination
by
abrasive particles
or
corrosive liquids (including
water).
Consequently,
the
bearing
frame
must
be
sealed.
The
following
are
typical seal arrangements.
Close-Clearance
Seals
Close-clearance seals consist merely
of a
close clear-
ance
between
the
shaft
and the
frame
or
bearing hous-
ing
(see Figures 11-10
and
11-15). They
are
very
simple, have
an
unlimited
life,
and
require
no
mainte-
nance.
However, they give only limited protection
from
water
spray (e.g., hosing down
the
pumps)
or
from
condensation during shut-down. Still, close-clearance
seals
are
very
successful
on
continuously operating
and
well-maintained
pumps where
the
normal bearing
operating
temperature prevents
any
water condensation
and
grease acts
as a
barrier
to
outside contaminants.
Elastomer Seals
Elastomer (lip-type) seals
are the
most
frequently
used
seals
in
current designs. They give good protec-
tion
from
contamination
and
moisture,
but
they also
generate
friction
heat
and
cause higher bearing-oper-
ating
temperatures with potentially reduced lubricant
life
(Figure
ll-15e).
Labyrinth Seals
Labyrinth
seals
offer
good bearing protection
and
gener-
ate
no
heat. They require more space
and are
relatively
expensive.
At
present, they
are
offered
as
optional equip-
ment
only. They
are
suitable only
for
horizontal
shafts.
Pump
Shaft
Seals
To
contain
the
liquid
in the
pump,
the
pump
shaft
must
be
sealed against
the
pressure
in the
pump.
The two
basic types
of
seals
are
packings
and
mechanical seals,
and
both have advantages.
The final
selection
of
seal
type
depends
on
installation requirements
and
owner
preferences,
but
packing
is
recommended
for
water
and
wastewater
service
in any
installation where leakage
from
the
stuffing
box is not
objectionable
or on
vertical
turbine
pumps that require dismantling
for
seal removal.
Packing
Packing
is the
simplest
and
most frequently used
seal.
The
packing
is
usually made
of
braided synthetic
fibers
impregnated with special lubricating com-
pounds.
The
packing rings require continuous lubrica-
tion
and
cooling, accomplished
by
using
the
pumped
fluid
or
an
external clean water source,
so a
properly
adjusted
packing must continuously leak
and
drip.
All
packings require periodic inspection
and
occasional
adjustment
of the
gland (see Figure
11-10).
Packings
are
frequently
equipped with
a
water seal
ring
(see Figure
11-10)
so
that
a
buffer
liquid
from
an
outside source (potable water
or
chlorinated
final
efflu-
ent for
wastewater pumps)
or
from
the
pump discharge
(for
clean water pumps)
can be
injected into
it.
This
ensures that
the
packing gets
an
adequate supply
of
lubricating
and
cooling liquid under
all
operating con-
ditions, particularly when
the
pressure
on the
pump
side
of the
packing drops below
the
atmospheric pres-
sure.
The
injection
of
clean liquid
is
also used
to
pre-
vent
contaminants
and
gritty materials
in the
pumped
liquid
from
entering
the
packing
and
causing acceler-
ated
shaft
sleeve wear.
If
potable water
is
used
as the
buffer
liquid,
an air gap
must
be
provided between
the
fresh
water source
and the
packing
to
prevent contami-
nation
of the
water supply with
the
pumped liquid.
Although most types
of
packing
in
wastewater ser-
vice must
be flushed
with clear water
to
avoid long-
term
scoring
or
abrasion
of
shaft
sleeves
due to
grit
in
the flow
stream, some types
of
braided, graphite-lubri-
cated
and
impregnated
or
Teflon-impregnated, non-
asbestos packing have proven
to
work
effectively
in
such
service without
any
external clear water
flushing.
Mechanical
Seals
Mechanical seals have
the
advantages
of no
leakage
and
no
need
for
periodic
maintenance,
but
they
are
rel-
atively
expensive
and
require care
in
installation. Some
are
subject
to
catastrophic failure.
For
mechanical seal
replacement,
the
pump must
be
partially disassembled,
which
is
costly. Mechanical seals should therefore
not
be
specified indiscriminately. Note that
API 610 has an
excellent discussion
of
mechanical seals.
A
typical, simple, single-face mechanical seal
is
shown
in
Figure
1
l-16a.
Mechanical seals rely
on
very