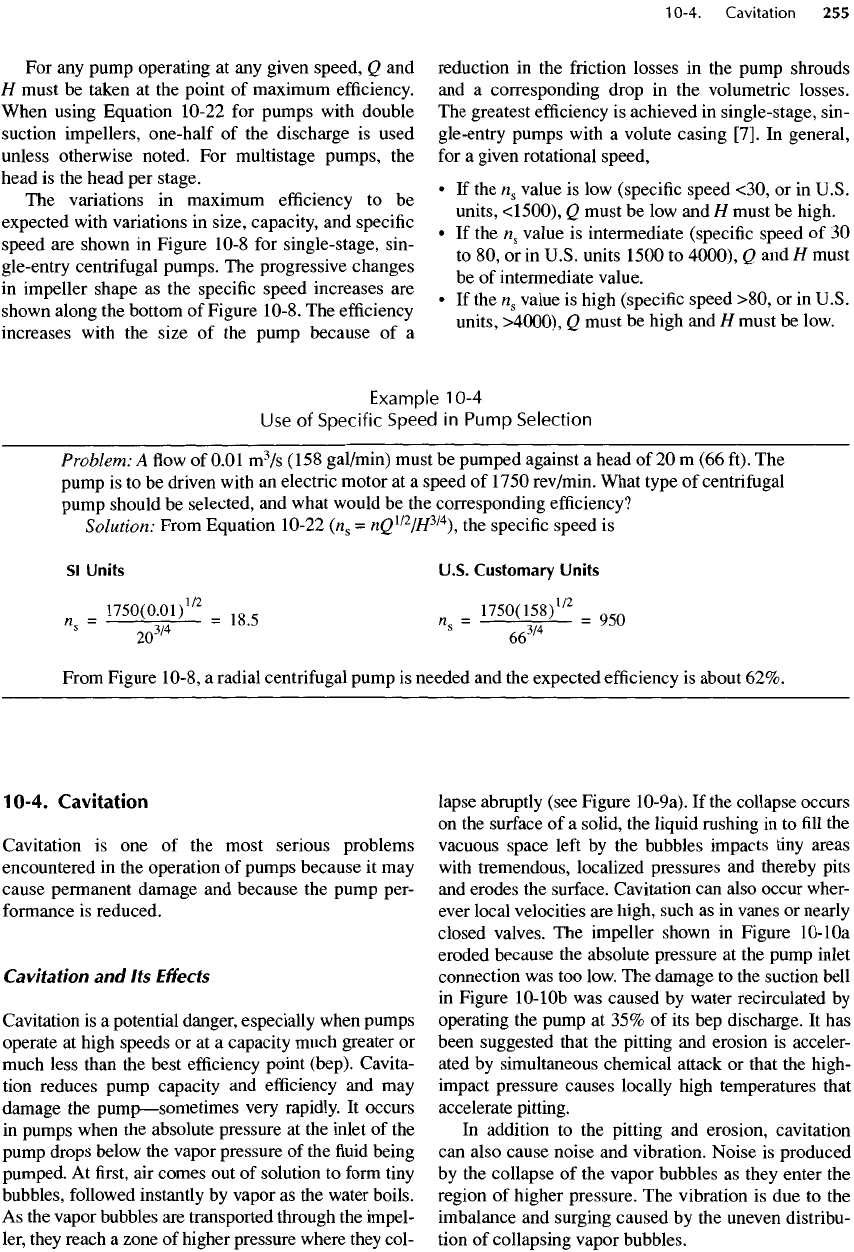
For any
pump operating
at any
given speed,
Q and
H
must
be
taken
at the
point
of
maximum
efficiency.
When using Equation 10-22
for
pumps with double
suction
impellers, one-half
of the
discharge
is
used
unless otherwise noted.
For
multistage pumps,
the
head
is the
head
per
stage.
The
variations
in
maximum
efficiency
to be
expected with variations
in
size, capacity,
and
specific
speed
are
shown
in
Figure 10-8
for
single-stage, sin-
gle-entry centrifugal pumps.
The
progressive changes
in
impeller shape
as the
specific speed increases
are
shown
along
the
bottom
of
Figure 10-8.
The
efficiency
increases
with
the
size
of the
pump because
of a
reduction
in the
friction losses
in the
pump shrouds
and
a
corresponding drop
in the
volumetric losses.
The
greatest
efficiency
is
achieved
in
single-stage, sin-
gle-entry pumps with
a
volute casing
[7].
In
general,
for
a
given rotational speed,
• If the
n
s
value
is low
(specific speed <30,
or in
U.S.
units,
<1500),
Q
must
be low and H
must
be
high.
• If the
n
s
value
is
intermediate (specific speed
of 30
to 80, or in
U.S. units 1500
to
4000),
Q and H
must
be of
intermediate value.
• If the
n
s
value
is
high (specific speed >80,
or in
U.S.
units,
>4000),
Q
must
be
high
and H
must
be
low.
Example
10-4
Use of
Specific
Speed
in
Pump
Selection
Problem:
A flow of
0.01
m
3
/s
(158
gal/min)
must
be
pumped against
a
head
of 20
m
(66
ft).
The
pump
is to be
driven with
an
electric motor
at a
speed
of
1750 rev/min. What type
of
centrifugal
pump
should
be
selected,
and
what would
be the
corresponding
efficiency?
Solution:
From Equation 10-22
(n
s
=
nQ
1/2
///
3/4
),
the
specific speed
is
Sl
Units
U.S.
Customary
Units
„.
=
1750(O
3
Ol)
1
'
2
=
185
^
=
1750058)"
2
=
950
From Figure 10-8,
a
radial
centrifugal
pump
is
needed
and the
expected
efficiency
is
about 62%.
10-4.
Cavitation
Cavitation
is one of the
most serious problems
encountered
in the
operation
of
pumps because
it may
cause permanent damage
and
because
the
pump per-
formance
is
reduced.
Cavitation
and Its
Effects
Cavitation
is a
potential danger, especially when pumps
operate
at
high speeds
or at a
capacity much greater
or
much
less than
the
best
efficiency
point (bep). Cavita-
tion reduces pump capacity
and
efficiency
and may
damage
the
pump
—
sometimes
very rapidly.
It
occurs
in
pumps when
the
absolute pressure
at the
inlet
of the
pump
drops below
the
vapor pressure
of the fluid
being
pumped.
At first, air
comes
out of
solution
to
form
tiny
bubbles, followed instantly
by
vapor
as the
water
boils.
As
the
vapor bubbles
are
transported through
the
impel-
ler, they reach
a
zone
of
higher pressure where they col-
lapse abruptly (see Figure
10-9
a).
If the
collapse occurs
on
the
surface
of a
solid,
the
liquid rushing
in to fill the
vacuous
space
left
by the
bubbles impacts tiny areas
with
tremendous, localized pressures
and
thereby pits
and
erodes
the
surface. Cavitation
can
also occur wher-
ever
local velocities
are
high, such
as in
vanes
or
nearly
closed valves.
The
impeller shown
in
Figure
10-1Oa
eroded because
the
absolute pressure
at the
pump inlet
connection
was too
low.
The
damage
to the
suction bell
in
Figure
10-1Ob
was
caused
by
water recirculated
by
operating
the
pump
at 35% of its bep
discharge.
It has
been
suggested that
the
pitting
and
erosion
is
acceler-
ated
by
simultaneous chemical attack
or
that
the
high-
impact pressure causes locally high temperatures that
accelerate pitting.
In
addition
to the
pitting
and
erosion, cavitation
can
also cause noise
and
vibration. Noise
is
produced
by
the
collapse
of the
vapor bubbles
as
they enter
the
region
of
higher pressure.
The
vibration
is due to the
imbalance
and
surging caused
by the
uneven distribu-
tion
of
collapsing vapor bubbles.