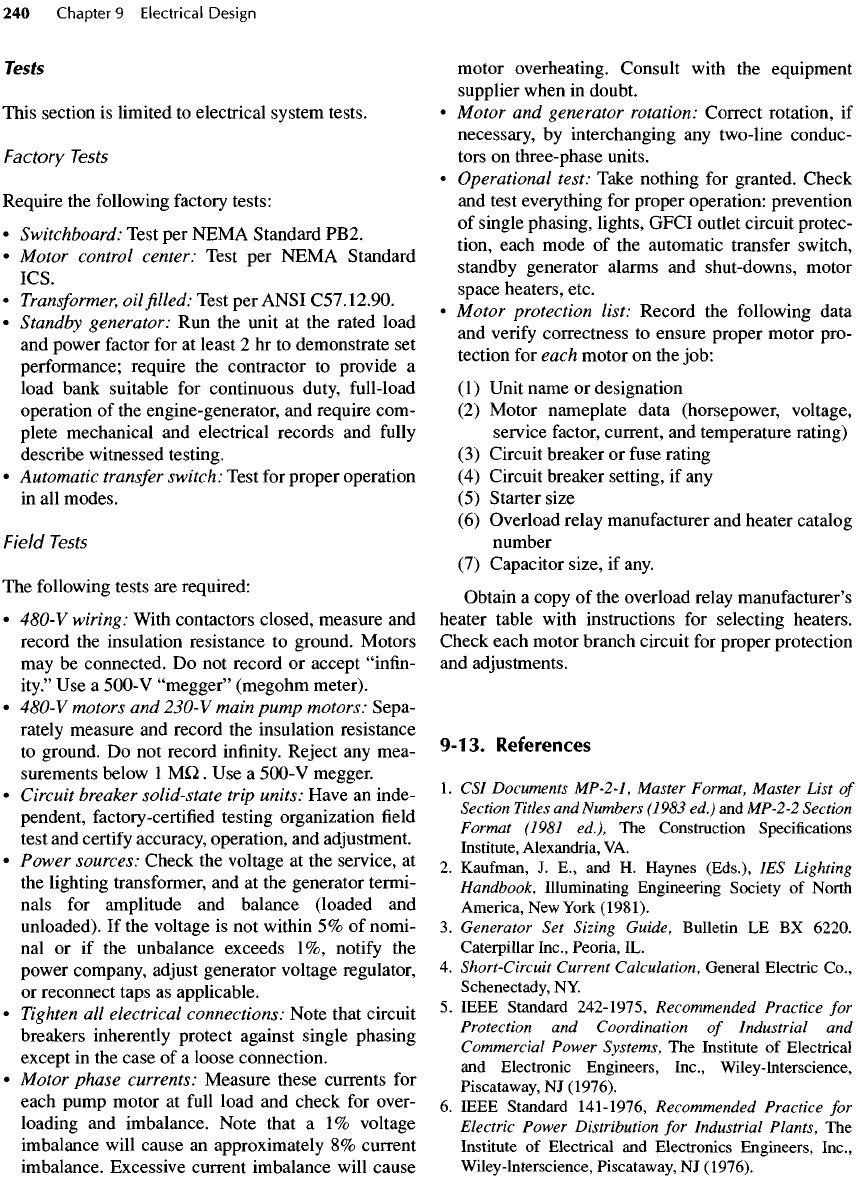
Tests
This
section
is
limited
to
electrical
system
tests.
Factory
Tests
Require
the
following
factory
tests:
•
Switchboard: Test
per
NEMA Standard PB2.
•
Motor control center: Test
per
NEMA Standard
ICS.
•
Transformer,
oil
filled: Test
per
ANSI
C57.
12.90.
•
Standby generator:
Run the
unit
at the
rated load
and
power
factor
for at
least
2 hr to
demonstrate
set
performance;
require
the
contractor
to
provide
a
load bank suitable
for
continuous duty, full-load
operation
of the
engine-generator,
and
require com-
plete mechanical
and
electrical records
and
fully
describe witnessed testing.
•
Automatic
transfer
switch: Test
for
proper operation
in
all
modes.
Field
Tests
The
following
tests
are
required:
•
480
-V
wiring: With contactors closed, measure
and
record
the
insulation resistance
to
ground. Motors
may
be
connected.
Do not
record
or
accept
"infin-
ity."
Use a
500-V
"megger"
(megohm meter).
•
480-V
motors
and
230-V
main pump motors:
Sepa-
rately measure
and
record
the
insulation resistance
to
ground.
Do not
record
infinity.
Reject
any
mea-
surements
below
1
MQ
.
Use a
500-V
megger.
•
Circuit breaker solid-state
trip
units: Have
an
inde-
pendent,
factory-certified
testing organization
field
test
and
certify
accuracy, operation,
and
adjustment.
•
Power sources: Check
the
voltage
at the
service,
at
the
lighting transformer,
and at the
generator termi-
nals
for
amplitude
and
balance (loaded
and
unloaded).
If the
voltage
is not
within
5% of
nomi-
nal or if the
unbalance exceeds
1%,
notify
the
power
company,
adjust
generator voltage regulator,
or
reconnect taps
as
applicable.
•
Tighten
all
electrical connections: Note that circuit
breakers inherently protect against single phasing
except
in the
case
of a
loose connection.
•
Motor phase currents: Measure these currents
for
each pump motor
at
full
load
and
check
for
over-
loading
and
imbalance. Note that
a 1%
voltage
imbalance will cause
an
approximately
8%
current
imbalance. Excessive current imbalance will cause
motor overheating. Consult with
the
equipment
supplier when
in
doubt.
•
Motor
and
generator rotation: Correct rotation,
if
necessary,
by
interchanging
any
two-line conduc-
tors
on
three-phase units.
•
Operational test: Take nothing
for
granted. Check
and
test everything
for
proper operation: prevention
of
single phasing, lights, GFCI outlet circuit protec-
tion, each mode
of the
automatic transfer switch,
standby
generator alarms
and
shut-downs, motor
space heaters, etc.
•
Motor protection list: Record
the
following data
and
verify
correctness
to
ensure proper motor pro-
tection
for
each motor
on the
job:
(1)
Unit name
or
designation
(2)
Motor nameplate data (horsepower, voltage,
service
factor,
current,
and
temperature rating)
(3)
Circuit breaker
or
fuse
rating
(4)
Circuit breaker setting,
if any
(5)
Starter size
(6)
Overload relay manufacturer
and
heater catalog
number
(7)
Capacitor size,
if
any.
Obtain
a
copy
of the
overload relay manufacturer's
heater table with instructions
for
selecting heaters.
Check each motor branch circuit
for
proper protection
and
adjustments.
9-13.
References
1.
CSI
Documents
MP
-2-1,
Master Format, Master List
of
Section
Titles
and
Numbers (1983 ed.)
andMP-2-2
Section
Format (1981
ed.),
The
Construction Specifications
Institute, Alexandria,
VA.
2.
Kaufman,
J.
E.,
and H.
Haynes
(Eds.),
IES
Lighting
Handbook, Illuminating
Engineering
Society
of
North
America,
New
York
(1981).
3.
Generator
Set
Sizing Guide, Bulletin
LE BX
6220.
Caterpillar
Inc.,
Peoria,
IL.
4.
Short-Circuit Current Calculation,
General
Electric
Co.,
Schenectady,
NY.
5.
IEEE
Standard
242-1975,
Recommended Practice
for
Protection
and
Coordination
of
Industrial
and
Commercial Power Systems,
The
Institute
of
Electrical
and
Electronic
Engineers,
Inc.,
Wiley-lnterscience,
Piscataway,
NJ
(1976).
6.
IEEE
Standard
141-1976,
Recommended Practice
for
Electric
Power
Distribution
for
Industrial
Plants,
The
Institute
of
Electrical
and
Electronics
Engineers,
Inc.,
Wiley-lnterscience,
Piscataway,
NJ
(1976).