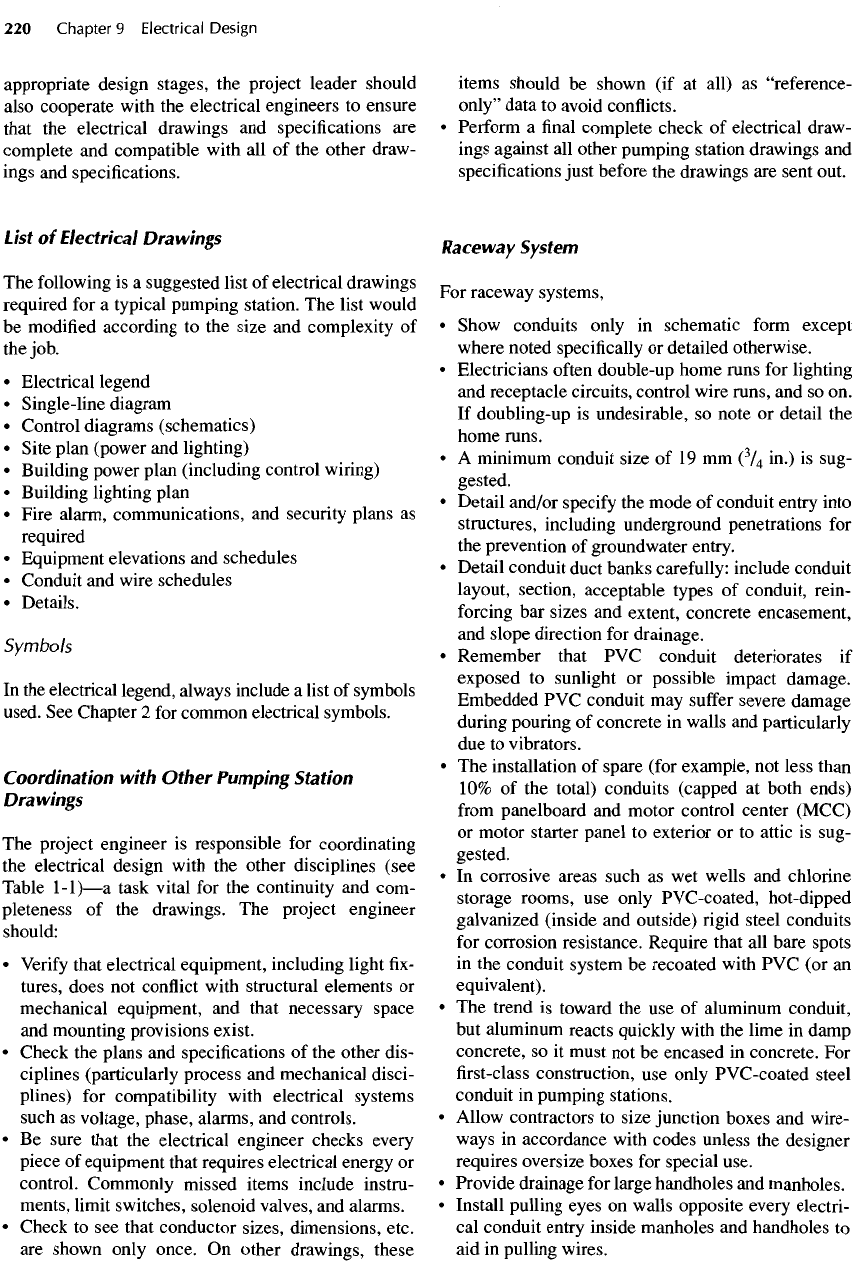
appropriate design stages,
the
project leader should
also cooperate
with
the
electrical engineers
to
ensure
that
the
electrical drawings
and
specifications
are
complete
and
compatible
with
all of the
other draw-
ings
and
specifications.
List
of
Electrical
Drawings
The
following
is a
suggested list
of
electrical drawings
required
for a
typical pumping station.
The
list would
be
modified
according
to the
size
and
complexity
of
the
job.
•
Electrical legend
•
Single-line diagram
•
Control diagrams (schematics)
•
Site plan (power
and
lighting)
•
Building power plan (including control wiring)
•
Building lighting plan
•
Fire alarm, communications,
and
security plans
as
required
•
Equipment elevations
and
schedules
•
Conduit
and
wire schedules
•
Details.
Symbols
In
the
electrical
legend, always include
a
list
of
symbols
used.
See
Chapter
2 for
common electrical symbols.
Coordination
with Other
Pumping
Station
Drawings
The
project engineer
is
responsible
for
coordinating
the
electrical design with
the
other disciplines (see
Table
1-1)
—
a
task vital
for the
continuity
and
com-
pleteness
of the
drawings.
The
project engineer
should:
•
Verify
that electrical equipment, including light fix-
tures,
does
not
conflict
with structural elements
or
mechanical
equipment,
and
that necessary space
and
mounting provisions exist.
•
Check
the
plans
and
specifications
of the
other dis-
ciplines (particularly process
and
mechanical disci-
plines)
for
compatibility with electrical systems
such
as
voltage, phase, alarms,
and
controls.
• Be
sure that
the
electrical engineer checks every
piece
of
equipment that requires electrical energy
or
control. Commonly missed items include instru-
ments, limit switches, solenoid valves,
and
alarms.
•
Check
to see
that conductor sizes, dimensions, etc.
are
shown only once.
On
other drawings, these
items should
be
shown
(if at
all)
as
"reference-
only"
data
to
avoid
conflicts.
•
Perform
a final
complete check
of
electrical draw-
ings against
all
other pumping station drawings
and
specifications
just before
the
drawings
are
sent out.
Raceway
System
For
raceway systems,
•
Show conduits only
in
schematic
form
except
where noted specifically
or
detailed otherwise.
•
Electricians
often
double-up home runs
for
lighting
and
receptacle circuits, control wire runs,
and so on.
If
doubling-up
is
undesirable,
so
note
or
detail
the
home runs.
• A
minimum conduit size
of 19 mm
(
3
/4
in.)
is
sug-
gested.
•
Detail and/or
specify
the
mode
of
conduit entry into
structures,
including underground penetrations
for
the
prevention
of
groundwater entry.
•
Detail conduit duct banks carefully: include conduit
layout,
section, acceptable types
of
conduit, rein-
forcing
bar
sizes
and
extent, concrete encasement,
and
slope direction
for
drainage.
•
Remember that
PVC
conduit deteriorates
if
exposed
to
sunlight
or
possible impact damage.
Embedded
PVC
conduit
may
suffer
severe damage
during pouring
of
concrete
in
walls
and
particularly
due
to
vibrators.
• The
installation
of
spare (for example,
not
less than
10%
of the
total) conduits (capped
at
both ends)
from
panelboard
and
motor control center (MCC)
or
motor starter panel
to
exterior
or to
attic
is
sug-
gested.
• In
corrosive areas such
as wet
wells
and
chlorine
storage rooms,
use
only PVC-coated, hot-dipped
galvanized
(inside
and
outside) rigid steel conduits
for
corrosion resistance. Require that
all
bare spots
in the
conduit system
be
recoated with
PVC (or an
equivalent).
• The
trend
is
toward
the use of
aluminum conduit,
but
aluminum reacts quickly with
the
lime
in
damp
concrete,
so it
must
not be
encased
in
concrete.
For
first-class
construction,
use
only PVC-coated steel
conduit
in
pumping stations.
•
Allow contractors
to
size junction boxes
and
wire-
ways
in
accordance with codes unless
the
designer
requires oversize boxes
for
special use.
•
Provide drainage
for
large handholes
and
manholes.
•
Install pulling eyes
on
walls
opposite
every
electri-
cal
conduit entry inside manholes
and
handholes
to
aid in
pulling wires.