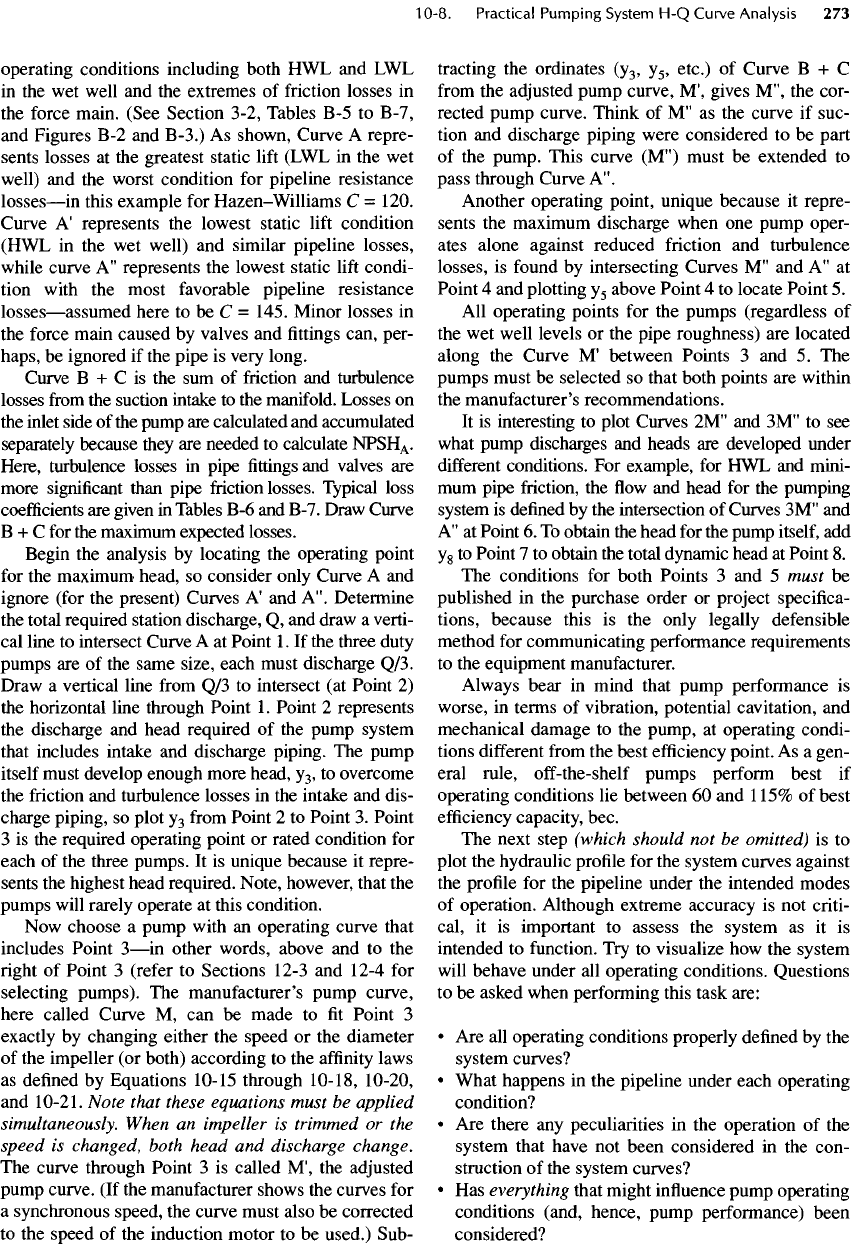
operating conditions including both
HWL and LWL
in
the wet
well
and the
extremes
of
friction
losses
in
the
force main. (See Section 3-2, Tables
B-5 to
B-7,
and
Figures
B
-2
and
B
-3.)
As
shown, Curve
A
repre-
sents losses
at the
greatest static
lift
(LWL
in the wet
well)
and the
worst condition
for
pipeline resistance
losses
—
in
this example
for
Hazen-
Williams
C=
120.
Curve
A'
represents
the
lowest static
lift
condition
(HWL
in the wet
well)
and
similar pipeline losses,
while
curve
A"
represents
the
lowest static
lift
condi-
tion with
the
most favorable
pipeline
resistance
losses
—
assumed
here
to be C =
145. Minor losses
in
the
force main caused
by
valves
and fittings
can, per-
haps,
be
ignored
if the
pipe
is
very long.
Curve
B + C is the sum of
friction
and
turbulence
losses
from
the
suction intake
to the
manifold. Losses
on
the
inlet side
of the
pump
are
calculated
and
accumulated
separately
because they
are
needed
to
calculate
NPSH
A
.
Here, turbulence losses
in
pipe
fittings and
valves
are
more
significant
than pipe
friction
losses. Typical loss
coefficients
are
given
in
Tables
B-6 and
B-7. Draw Curve
B
+ C for the
maximum expected losses.
Begin
the
analysis
by
locating
the
operating point
for
the
maximum
head,
so
consider only Curve
A and
ignore (for
the
present) Curves
A
1
and
A".
Determine
the
total required station discharge,
Q, and
draw
a
verti-
cal
line
to
intersect Curve
A at
Point
1.
If the
three duty
pumps
are of the
same size, each must discharge
Q/3.
Draw
a
vertical line
from
Q/3 to
intersect
(at
Point
2)
the
horizontal line through Point
1
.
Point
2
represents
the
discharge
and
head required
of the
pump system
that
includes intake
and
discharge piping.
The
pump
itself must develop enough more head,
y
3
,
to
overcome
the
friction
and
turbulence losses
in the
intake
and
dis-
charge piping,
so
plot
y
3
from
Point
2 to
Point
3.
Point
3 is the
required operating point
or
rated
condition
for
each
of the
three pumps.
It is
unique because
it
repre-
sents
the
highest head required. Note, however, that
the
pumps
will rarely operate
at
this condition.
Now
choose
a
pump with
an
operating curve that
includes Point
3
—
in
other words, above
and to the
right
of
Point
3
(refer
to
Sections 12-3
and
12-4
for
selecting pumps).
The
manufacturer's pump curve,
here called Curve
M, can be
made
to fit
Point
3
exactly
by
changing either
the
speed
or the
diameter
of
the
impeller
(or
both) according
to the
affinity
laws
as
defined
by
Equations 10-15 through
10-18,
10-20,
and
10-21.
Note that these
equations
must
be
applied
simultaneously.
When
an
impeller
is
trimmed
or the
speed
is
changed, both head
and
discharge
change.
The
curve through Point
3 is
called
M',
the
adjusted
pump
curve.
(If the
manufacturer shows
the
curves
for
a
synchronous speed,
the
curve must also
be
corrected
to the
speed
of the
induction motor
to be
used.) Sub-
tracting
the
ordinates
(y
3
,
y
5
,
etc.)
of
Curve
B + C
from
the
adjusted pump curve,
M',
gives
M",
the
cor-
rected pump curve. Think
of
M"
as the
curve
if
suc-
tion
and
discharge piping were considered
to be
part
of
the
pump. This curve (M") must
be
extended
to
pass through Curve
A".
Another operating point, unique because
it
repre-
sents
the
maximum discharge when
one
pump oper-
ates alone against reduced
friction
and
turbulence
losses,
is
found
by
intersecting Curves
M"
and
A"
at
Point
4 and
plotting
y
5
above
Point
4 to
locate
Point
5.
All
operating points
for the
pumps (regardless
of
the
wet
well levels
or the
pipe roughness)
are
located
along
the
Curve
M'
between
Points
3 and 5. The
pumps
must
be
selected
so
that both points
are
within
the
manufacturer's recommendations.
It
is
interesting
to
plot Curves
2M"
and
3M"
to see
what
pump discharges
and
heads
are
developed under
different
conditions.
For
example,
for HWL and
mini-
mum
pipe
friction,
the flow and
head
for the
pumping
system
is
defined
by the
intersection
of
Curves
3M"
and
A"
at
Point
6. To
obtain
the
head
for the
pump itself,
add
y
8
to
Point
7 to
obtain
the
total dynamic head
at
Point
8.
The
conditions
for
both Points
3 and 5
must
be
published
in the
purchase order
or
project specifica-
tions, because this
is the
only legally defensible
method
for
communicating performance requirements
to the
equipment manufacturer.
Always
bear
in
mind that pump performance
is
worse,
in
terms
of
vibration, potential cavitation,
and
mechanical damage
to the
pump,
at
operating condi-
tions
different
from
the
best
efficiency
point.
As a
gen-
eral rule, off-the-shelf pumps perform best
if
operating conditions
lie
between
60 and
115%
of
best
efficiency
capacity,
bee.
The
next
step
(which should
not be
omitted)
is to
plot
the
hydraulic
profile
for the
system curves against
the
profile
for the
pipeline under
the
intended modes
of
operation. Although extreme accuracy
is not
criti-
cal,
it is
important
to
assess
the
system
as it is
intended
to
function.
Try to
visualize
how the
system
will behave under
all
operating conditions. Questions
to
be
asked when performing this task are:
• Are all
operating conditions properly
defined
by the
system
curves?
•
What happens
in the
pipeline
under each operating
condition?
• Are
there
any
peculiarities
in the
operation
of the
system that have
not
been
considered
in the
con-
struction
of the
system curves?
• Has
everything that might
influence
pump operating
conditions (and, hence, pump performance) been
considered?