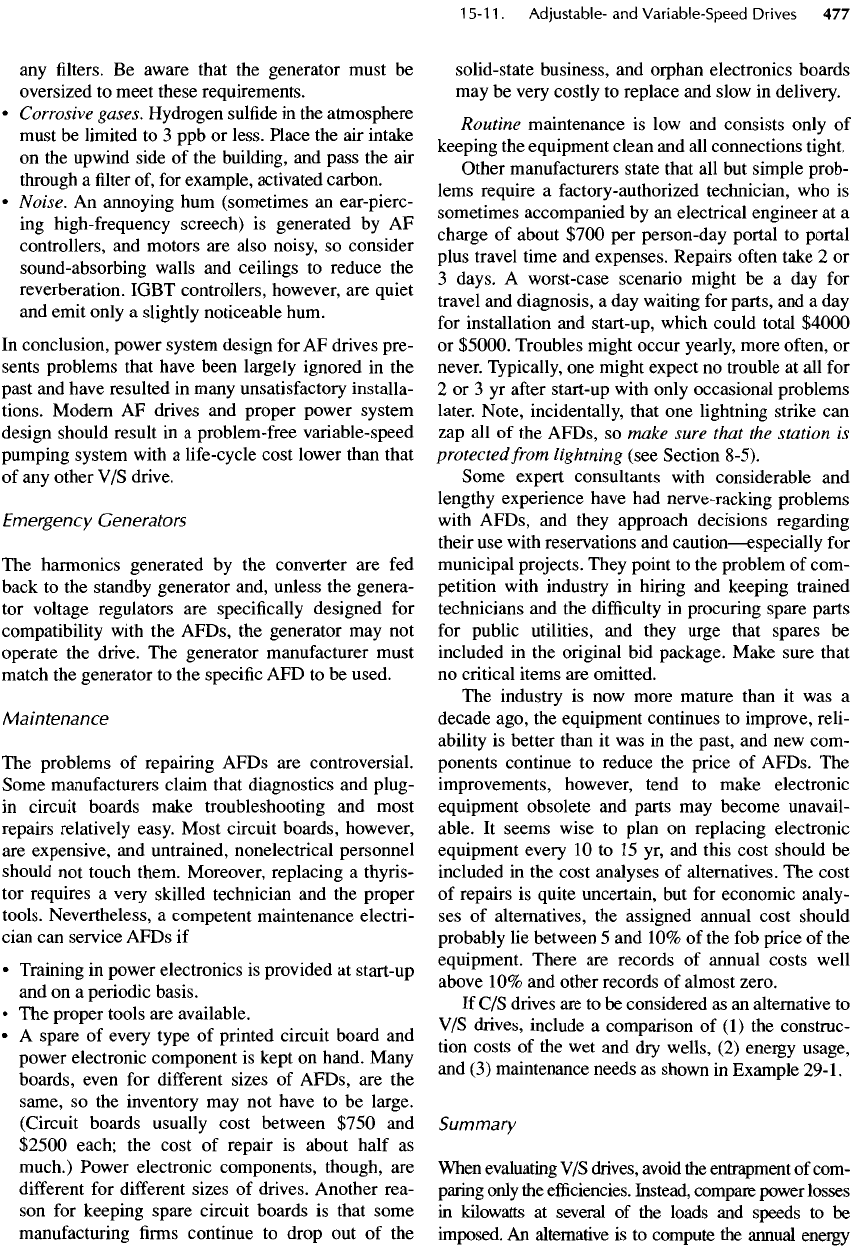
any
filters. Be
aware that
the
generator must
be
oversized
to
meet these requirements.
•
Corrosive
gases. Hydrogen
sulfide
in the
atmosphere
must
be
limited
to 3 ppb or
less. Place
the air
intake
on
the
upwind side
of the
building,
and
pass
the air
through
a filter of, for
example, activated carbon.
•
Noise.
An
annoying
hum
(sometimes
an
ear-pierc-
ing
high-frequency
screech)
is
generated
by AF
controllers,
and
motors
are
also noisy,
so
consider
sound-absorbing
walls
and
ceilings
to
reduce
the
reverberation. IGBT controllers, however,
are
quiet
and
emit only
a
slightly noticeable hum.
In
conclusion, power system design
for AF
drives pre-
sents
problems that have been largely ignored
in the
past
and
have resulted
in
many unsatisfactory installa-
tions. Modern
AF
drives
and
proper power system
design should result
in a
problem-free
variable-
speed
pumping
system with
a
life-cycle cost lower than that
of
any
other
V/S
drive.
Emergency
Generators
The
harmonics generated
by the
converter
are fed
back
to the
standby generator and, unless
the
genera-
tor
voltage regulators
are
specifically
designed
for
compatibility with
the
AFDs,
the
generator
may not
operate
the
drive.
The
generator
manufacturer
must
match
the
generator
to the
specific
AFD to be
used.
Maintenance
The
problems
of
repairing AFDs
are
controversial.
Some
manufacturers
claim that diagnostics
and
plug-
in
circuit boards make troubleshooting
and
most
repairs relatively easy. Most circuit boards, however,
are
expensive,
and
untrained, nonelectrical personnel
should
not
touch them. Moreover, replacing
a
thyris-
tor
requires
a
very skilled technician
and the
proper
tools. Nevertheless,
a
competent maintenance electri-
cian
can
service AFDs
if
•
Training
in
power electronics
is
provided
at
start-up
and
on a
periodic basis.
• The
proper tools
are
available.
• A
spare
of
every type
of
printed circuit board
and
power electronic component
is
kept
on
hand. Many
boards, even
for
different
sizes
of
AFDs,
are the
same,
so the
inventory
may not
have
to be
large.
(Circuit
boards
usually
cost between
$750
and
$2500
each;
the
cost
of
repair
is
about half
as
much.)
Power electronic components, though,
are
different
for
different
sizes
of
drives. Another rea-
son
for
keeping spare circuit boards
is
that some
manufacturing
firms
continue
to
drop
out of the
solid-state business,
and
orphan electronics boards
may
be
very costly
to
replace
and
slow
in
delivery.
Routine maintenance
is low and
consists only
of
keeping
the
equipment clean
and all
connections tight.
Other manufacturers state that
all but
simple prob-
lems require
a
factory-authorized technician,
who is
sometimes accompanied
by an
electrical
engineer
at a
charge
of
about
$700
per
person-day portal
to
portal
plus travel time
and
expenses. Repairs
often
take
2 or
3
days.
A
worst-case scenario might
be a day for
travel
and
diagnosis,
a day
waiting
for
parts,
and a day
for
installation
and
start-up, which could total
$4000
or
$5000.
Troubles might occur yearly, more
often,
or
never. Typically,
one
might expect
no
trouble
at all for
2 or 3 yr
after
start-up with only occasional problems
later. Note, incidentally, that
one
lightning strike
can
zap all of the
AFDs,
so
make
sure
that
the
station
is
protected
from
lightning (see Section 8-5).
Some expert consultants with considerable
and
lengthy
experience have
had
nerve-racking problems
with
AFDs,
and
they approach decisions regarding
their
use
with reservations
and
caution
—
especially
for
municipal projects. They
point
to the
problem
of
com-
petition with industry
in
hiring
and
keeping trained
technicians
and the
difficulty
in
procuring spare parts
for
public utilities,
and
they urge that spares
be
included
in the
original
bid
package. Make sure that
no
critical
items
are
omitted.
The
industry
is now
more mature than
it was a
decade ago,
the
equipment continues
to
improve,
reli-
ability
is
better than
it was in the
past,
and new
com-
ponents continue
to
reduce
the
price
of
AFDs.
The
improvements, however, tend
to
make electronic
equipment
obsolete
and
parts
may
become unavail-
able.
It
seems wise
to
plan
on
replacing electronic
equipment every
10 to 15 yr, and
this cost should
be
included
in the
cost analyses
of
alternatives.
The
cost
of
repairs
is
quite uncertain,
but for
economic analy-
ses
of
alternatives,
the
assigned annual cost should
probably
lie
between
5 and 10% of the fob
price
of the
equipment.
There
are
records
of
annual costs well
above
10% and
other records
of
almost zero.
If
C/S
drives
are to be
considered
as an
alternative
to
V/S
drives, include
a
comparison
of (1) the
construc-
tion
costs
of the wet and dry
wells,
(2)
energy usage,
and
(3)
maintenance needs
as
shown
in
Example
29-1.
Summary
When
evaluating
V/S
drives, avoid
the
entrapment
of
com-
paring
only
the
efficiencies.
Instead, compare power losses
in
kilowatts
at
several
of the
loads
and
speeds
to be
imposed.
An
alternative
is to
compute
the
annual energy