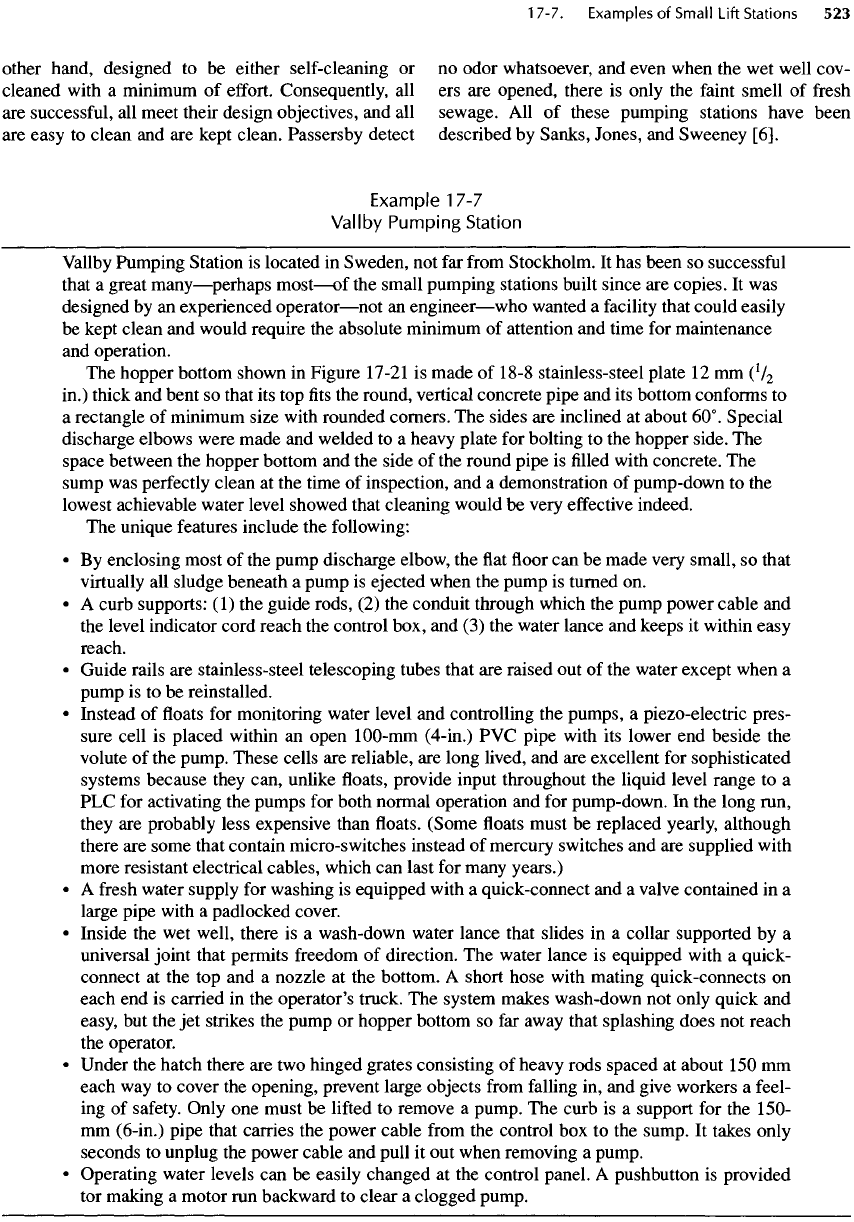
other hand, designed
to be
either self-cleaning
or
cleaned
with
a
minimum
of
effort.
Consequently,
all
are
successful,
all
meet their design objectives,
and all
are
easy
to
clean
and are
kept clean. Passersby detect
no
odor whatsoever,
and
even when
the wet
well cov-
ers are
opened, there
is
only
the
faint
smell
of
fresh
sewage.
All of
these pumping stations have been
described
by
Sanks,
Jones,
and
Sweeney
[6].
Example
1 7-7
Vallby Pumping Station
Vallby
Pumping Station
is
located
in
Sweden,
not far
from
Stockholm.
It has
been
so
successful
that
a
great
many—perhaps
most—of
the
small pumping stations built
since
are
copies.
It was
designed
by an
experienced
operator—not
an
engineer—who
wanted
a
facility
that could easily
be
kept clean
and
would require
the
absolute minimum
of
attention
and
time
for
maintenance
and
operation.
The
hopper bottom shown
in
Figure 17-21
is
made
of
18-8
stainless-steel plate
12 mm
(
l
/
2
in.) thick
and
bent
so
that
its top fits the
round, vertical concrete pipe
and its
bottom conforms
to
a
rectangle
of
minimum size with rounded corners.
The
sides
are
inclined
at
about 60°.
Special
discharge elbows were made
and
welded
to a
heavy plate
for
bolting
to the
hopper side.
The
space between
the
hopper bottom
and the
side
of the
round pipe
is filled
with concrete.
The
sump
was
perfectly clean
at the
time
of
inspection,
and a
demonstration
of
pump-down
to the
lowest achievable water level showed that cleaning would
be
very
effective
indeed.
The
unique features include
the
following:
• By
enclosing most
of the
pump discharge elbow,
the flat floor can be
made very small,
so
that
virtually
all
sludge beneath
a
pump
is
ejected when
the
pump
is
turned
on.
• A
curb supports:
(1)
the
guide rods,
(2) the
conduit through which
the
pump power cable
and
the
level indicator cord reach
the
control box,
and (3) the
water lance
and
keeps
it
within easy
reach.
•
Guide rails
are
stainless-steel telescoping tubes that
are
raised
out of the
water except when
a
pump
is to be
reinstalled.
•
Instead
of floats for
monitoring water level
and
controlling
the
pumps,
a
piezo-electric
pres-
sure
cell
is
placed within
an
open
100-mm
(4-in.)
PVC
pipe with
its
lower
end
beside
the
volute
of the
pump.
These
cells
are
reliable,
are
long lived,
and are
excellent
for
sophisticated
systems
because they can, unlike
floats,
provide input throughout
the
liquid level range
to a
PLC for
activating
the
pumps
for
both normal
operation
and for
pump-down.
In the
long run,
they
are
probably less expensive than
floats.
(Some
floats
must
be
replaced yearly, although
there
are
some that contain micro-switches instead
of
mercury switches
and are
supplied with
more resistant
electrical
cables,
which
can
last
for
many years.)
• A
fresh
water supply
for
washing
is
equipped with
a
quick-connect
and a
valve contained
in a
large pipe with
a
padlocked cover.
•
Inside
the wet
well, there
is a
wash-down water lance that slides
in a
collar supported
by a
universal
joint that permits freedom
of
direction.
The
water lance
is
equipped with
a
quick-
connect
at the top and a
nozzle
at the
bottom.
A
short hose with mating quick-connects
on
each
end is
carried
in the
operator's
truck.
The
system makes wash-down
not
only quick
and
easy,
but the jet
strikes
the
pump
or
hopper bottom
so far
away that splashing does
not
reach
the
operator.
•
Under
the
hatch there
are two
hinged grates consisting
of
heavy rods spaced
at
about
150
mm
each
way to
cover
the
opening, prevent large objects
from
falling
in, and
give workers
a
feel-
ing of
safety. Only
one
must
be
lifted
to
remove
a
pump.
The
curb
is a
support
for the
150-
mm
(6-in.) pipe that carries
the
power cable
from
the
control
box to the
sump.
It
takes only
seconds
to
unplug
the
power cable
and
pull
it out
when removing
a
pump.
•
Operating water levels
can be
easily changed
at the
control panel.
A
pushbutton
is
provided
tor
making
a
motor
run
backward
to
clear
a
clogged pump.