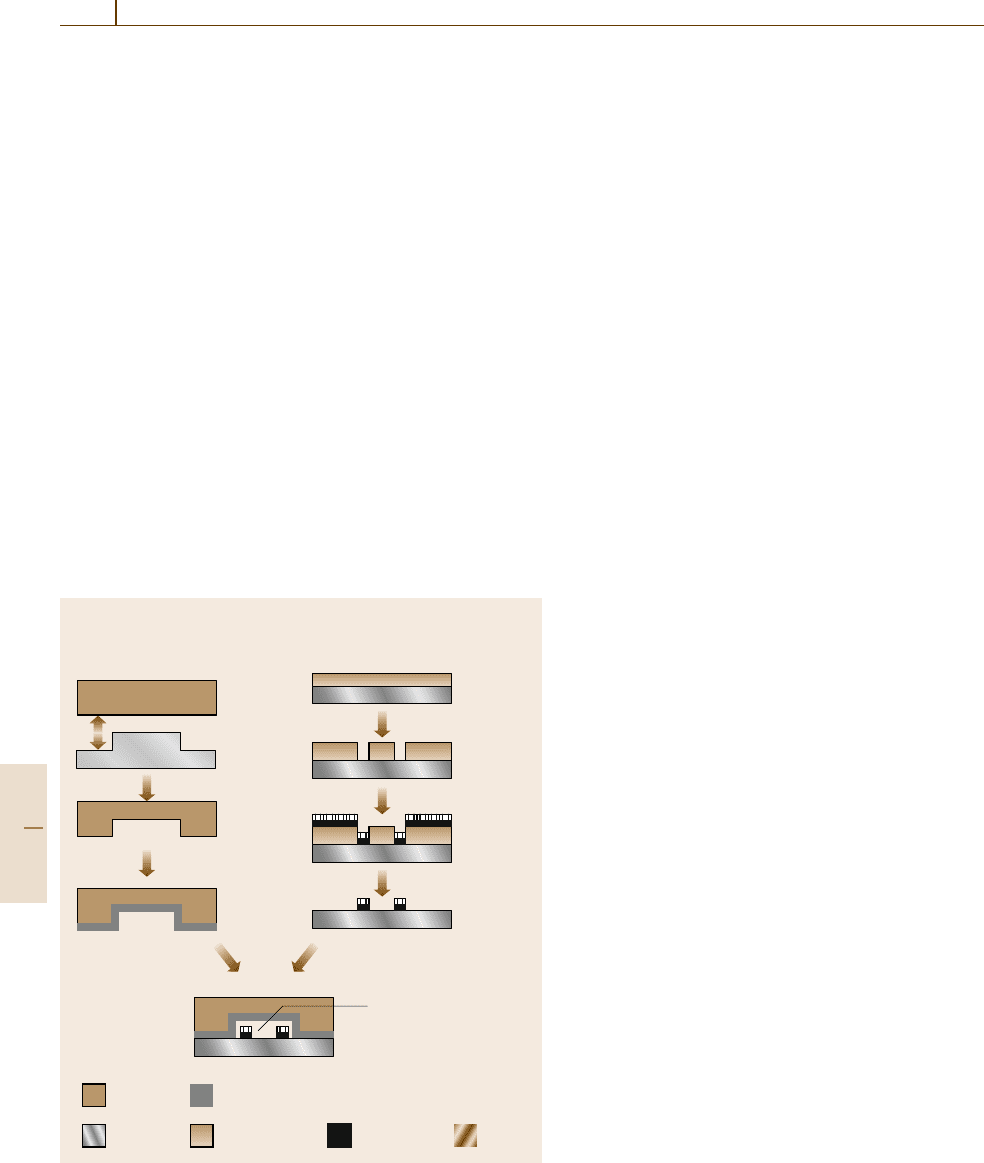
940 Part F Industrial Automation
structure with higher density induced a stronger DEP
force such that more CNTs could be attracted to the
microelectrodes. The gap distance between these mi-
croelectrodes is 5–10μm. The micropump pumped the
CNT suspension to the DEP chamber; a high frequency
AC voltage was applied to the finger-like microelec-
trodes so that metallic CNTs were attracted to them and
stayedintheDEP chamber. Semiconducting CNTs re-
mained in thesuspension and flowed out ofthe chamber.
Finally, the filtered suspension (with semiconducting
CNTs only) was transferred to an active nozzle for the
CNT deposition process. This will be described in the
next section.
The fabrication process of the DEP microcham-
ber is shown in Fig. 53.19. It was composed of two
different substrates. Polymethylmethacrylate (PMMA)
was used as the top substrate because it is electrically
and thermally insulating, optically transparent, and bio-
compatible. By using a hot embossing technique, the
PMMA substrate was patterned with a microchan-
nel (5mmL×1mmW×500 μm H) and a microcham-
ber (1cmL×5 mm W×500μm H) by replicating from
a fabricated metal mold. In order to protect the PMMA
Metal
mold
PMMA
Top substrate
Coat parylene C
UV glue bonding
Hot embossing of PMMA
substrate on metal mold
Bottom substrate
Spin on photoresist
on quartz substrate
Pattern and
develop PR
Deposit Ti and Au
Remove PR
Microchamber
PMMA Parylene C
Quartz Photoresist Titanium Gold
Fig. 53.19 The fabrication process of a DEP microchamber
substrate from the CNTs-alcoholsuspension, a parylene
C thin film layer was coated on the substrate, because
parylene resists chemical attack and is insoluble in all
organic solvents. Alternatively, quartz was used as the
bottom substrate,and arraysof the gold microelectrodes
were fabricated on the substrate by using a standard
photolithography process. A layer of AZ5214E pho-
toresist with thickness of 1.5μm was first spun onto
the 2
×1
quartz substrate. It was then patterned by
AB-M mask aligner and developed in an AZ300 de-
veloper. A layer of titanium with a thickness of 3nm
was deposited by thermal evaporator followed by de-
positing a layer of gold with thickness of 30nm. The
titanium provided a better adhesion between gold and
quartz. Afterwards, photoresist was removed in acetone
solution, and arrays of microelectrodes were formed on
the substrate. Finally, PMMA and quartz substrate were
bonded together by UV-glue to form a close cham-
ber. The fittings were connected at the ends of the
channel to form an inlet and an outlet for the DEP
chamber.
The separation performance of the DEP chamber
should be optimized for different nanoobjects. Several
parameters shouldbe considered in theprocess: thecon-
centration of nanoobjects in the suspension, the strength
of the DEP force, the flow rate of the suspension in
the DEP chamber, the structure of the channel, and the
microelectrodes of the DEP chamber.
53.3.4 Automated Robotic CNT Deposition
Workstation
In order to manipulate a specific type of CNTs precisely
and fabricate the CNT-based nanodevices effectively,
anewCNT deposition workstation has been devel-
oped as shown in Fig. 53.20. The system consists of
a microactive nozzle, a DEP microchamber, a DC mi-
crodiaphragm pump, and three micromanipulators. By
integrating these components into the deposition work-
station, a specific type of CNT can be deposited to
the desired position of the microelectrodes precisely
and automatically. The micron-sized active nozzle with
adiameterof10μm was fabricated from a micropipette
using a mechanical puller and is shown in Fig. 53.21.
It transferred the CNT suspension to the microelec-
trodes on a microchip, and a small droplet of the CNT
suspension (about 400 μm) was deposited on the mi-
crochip due to the small diameter of the active nozzle.
The volume of the droplet is critical because exces-
sive CNT suspension easily causes the formation of
multiple CNTs. The microactive nozzle was then con-
Part F 53.3